
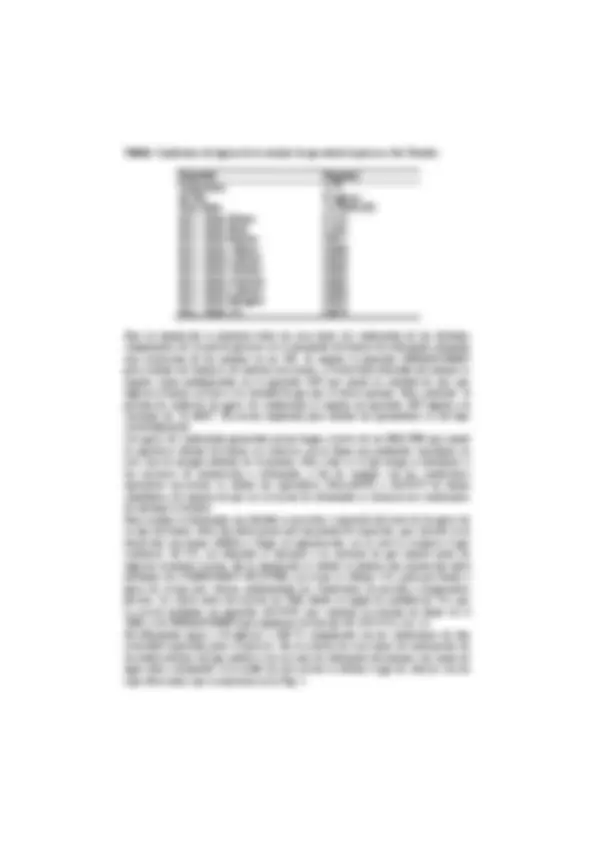
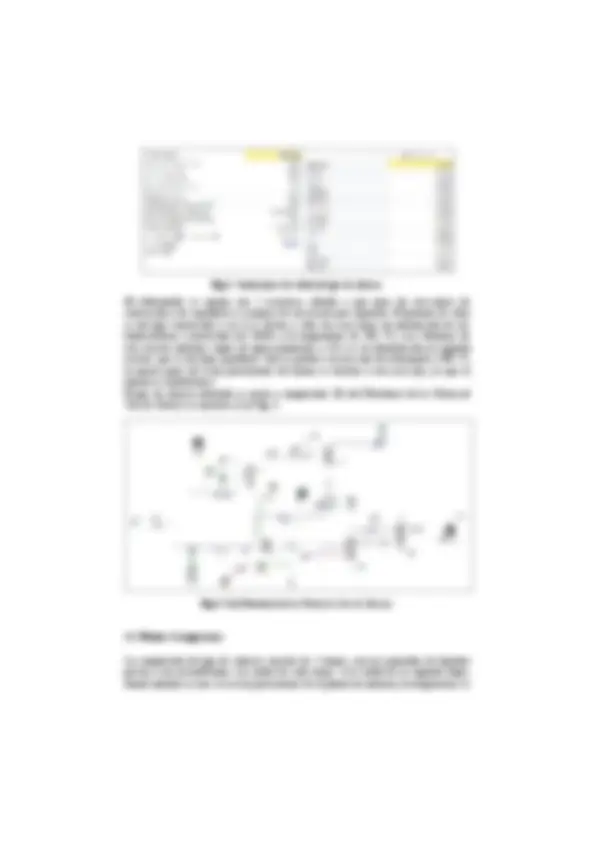
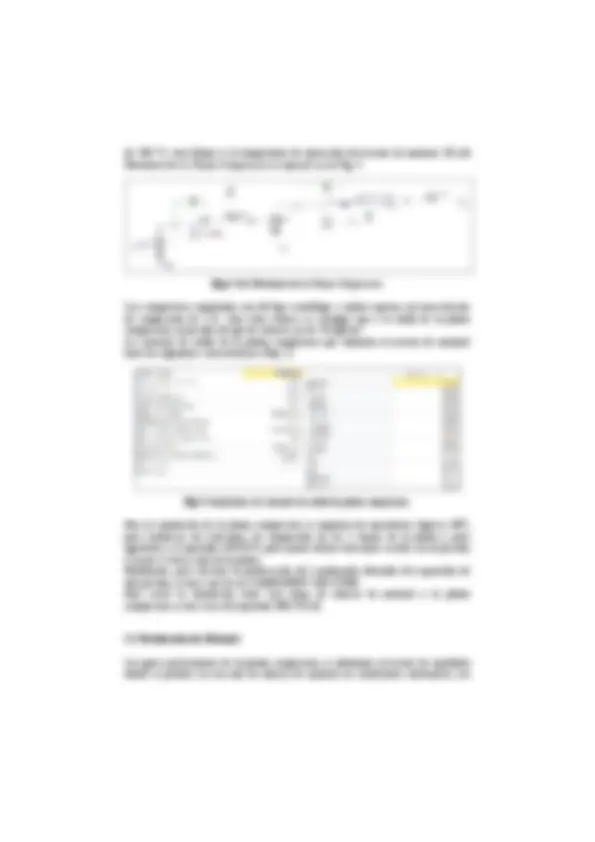
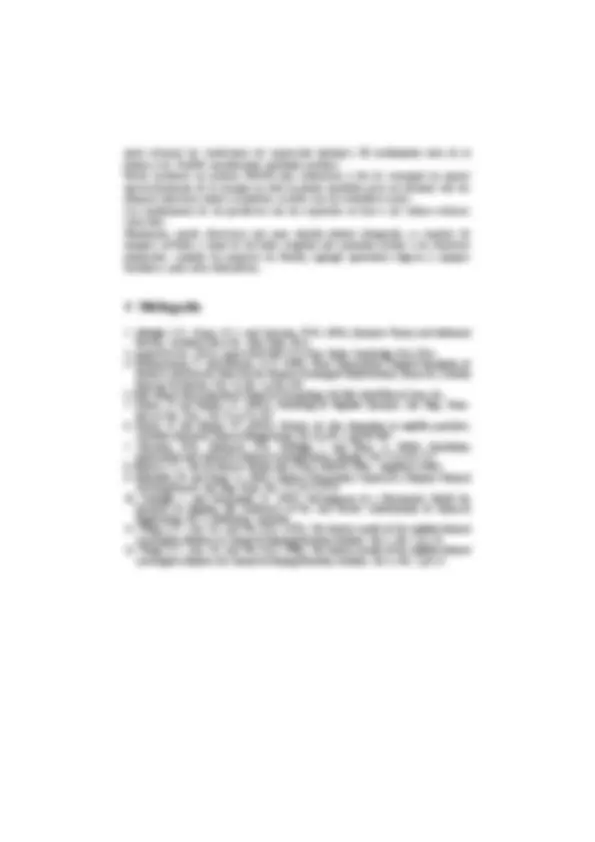
Prepara tus exámenes y mejora tus resultados gracias a la gran cantidad de recursos disponibles en Docsity
Gana puntos ayudando a otros estudiantes o consíguelos activando un Plan Premium
Prepara tus exámenes
Prepara tus exámenes y mejora tus resultados gracias a la gran cantidad de recursos disponibles en Docsity
Prepara tus exámenes con los documentos que comparten otros estudiantes como tú en Docsity
Los mejores documentos en venta realizados por estudiantes que han terminado sus estudios
Estudia con lecciones y exámenes resueltos basados en los programas académicos de las mejores universidades
Responde a preguntas de exámenes reales y pon a prueba tu preparación
Consigue puntos base para descargar
Gana puntos ayudando a otros estudiantes o consíguelos activando un Plan Premium
Comunidad
Pide ayuda a la comunidad y resuelve tus dudas de estudio
Descubre las mejores universidades de tu país según los usuarios de Docsity
Ebooks gratuitos
Descarga nuestras guías gratuitas sobre técnicas de estudio, métodos para controlar la ansiedad y consejos para la tesis preparadas por los tutores de Docsity
consiste en la simulación de una planta completa de producción de metanol a partir de gas natural; teniendo en cuenta los grados de libertad y la lógica de resolución del simulador utilizado. En este caso se pretende encontrar el diseño de proceso óptimo para cada sector de planta, como así también encontrar la mejor respuesta del proceso a los cambios de las variables de operación. Para ello se estudian los puntos relevantes de la simulación y se analiza el impacto que presentan en el modelo em
Tipo: Monografías, Ensayos
1 / 8
Esta página no es visible en la vista previa
¡No te pierdas las partes importantes!
Juan Lezama^1 , Dardo Mentesana^1 , Leonel Benitez^2 , Liliana Ale Ruiz^3
(^1) Facultad de Ingeniería, Universidad Nacional de Salta, Av. Bolivia 5150, Salta (^2) INIQUI (CONICET – UNSa), CIUNSa, Facultad de Ingeniería, Universidad Nacional de Salta, Av. Bolivia 5150, Salta (^3) Consejo de Investigaciones (CIUNSa) Facultad de Ingeniería, Universidad Nacional de Salta,Av. Bolivia 5150, Salta laleruiz@unsa.edu.ar
Resumen. El presente trabajo consiste en la simulación de una planta completa de producción de metanol a partir de gas natural; teniendo en cuenta los grados de libertad y la lógica de resolución del simulador utilizado. En este caso se pretende encontrar el diseño de proceso óptimo para cada sector de planta, como así también encontrar la mejor respuesta del proceso a los cambios de las variables de operación. Para ello se estudian los puntos relevantes de la simulación y se analiza el impacto que presentan en el modelo empleado. Con todos los resultados obtenidos se pretende determinar un rendimiento final del proceso y compararlo con las predicciones teóricas del mismo. Palabras Clave: Simulación, Proceso, Síntesis, Metanol, Hysys, Petroquímica, Gas Natural.
Actualmente, todo el metanol producido mundialmente se sintetiza mediante un proceso catalítico a partir de gas de síntesis (monóxido de carbono e hidrógeno). Esta reacción emplea altas temperaturas (300-400°C) y presiones (200-300 atm). Los catalizadores generalmente usados son óxido de cinc u óxido de cromo (III). El gas de síntesis es una mezcla de monóxido de carbono e hidrógeno y puede obtenerse mediante dos procesos productivos, la oxidación parcial y el reformado con vapor. Los mismos se seleccionan en base a la disponibilidad de materia prima y a la aplicación a la que esté destinado, ya sea producción de amoníaco y derivados u oxo procesos. Si la materia prima es gas natural el proceso más ampliamente usado para la obtención del gas de síntesis es el reformado con vapor de agua. La simulación permite estimar, de manera rápida y simple, la respuesta del proceso frente a variaciones en las condiciones de operación, esto posibilita determinar las variables más sensibles del modelo usado y definir los puntos críticos del mismo. En este trabajo se simula una planta, con todas las etapas involucradas, de síntesis de metanol a partir de gas natural. Para ello, en primer lugar se simula la obtención de gas de síntesis, luego la compresión del mismo y finalmente la producción de metanol grado combustible. Para la resolución del diseño planteado se utilizó el simulador Aspen HYSYS V8.3, tratando de incorporar en lo posible todas las herramientas del mismo para facilitar los cálculos y decisiones tomadas.
La simulación del proceso está organizada en tres etapas bien diferenciadas: Planta de gas de síntesis , Planta compresora y Planta de metanol. Cada etapa se estudia por separado de las restantes pero conformando una sola línea productiva, como se muestra en la Fig. 1.
Fig.1. Flowsheet global del proceso simulado (Aspen Hysys V8.2).
2.1 Planta de Gas de Síntesis (Syn-Gas)
Para llevar a cabo la síntesis del metanol a partir de gas natural se requiere, previo a la etapa de reacción de formación del mismo, generar gas de síntesis en la relación estequiométrica especificada (H 2 : [CO+CO 2 ] ≈ 2,3). Para conseguir esto se requiere operar en condiciones de elevada severidad, en un solo reformador. El caudal de la corriente de alimentación (Gas Tratado) a la planta es de 2, MMSCFD; se destinan 2 MMSCFD al proceso de reformado con vapor para obtener gas de síntesis, y el gas restante se usa como combustible en el horno de reformado catalítico primario. Las condiciones de la corriente de gas que ingresa al proceso se especifican en la Tabla 1. Todas las corrientes que ingresan al reformador lo hacen a 10 kgf/cm^2 , para lo que se utiliza una válvula reductora de presión, donde sea necesario. El vapor de agua que ingresa al reformador debe ser recalentado a 500 ºC, a la presión de operación. A esta temperatura se produce la metanación de los hidrocarburos que componen la mezcla gaseosa. La relación de alimentación vapor:hidrocarburo elegida es de 1:1, con la cual se obtiene el mejor rendimiento en gas de síntesis generado, cumpliendo además con la relación H 2 :[CO+CO 2 ]. En el hogar del horno de reformado se trabaja con un exceso de aire en la alimentación del 10%, controlando que a la salida los gases de combustión tengan una presión similar a la del gas natural destinado al reformado (10 kgf/cm^2 ). Estos gases alcanzan una temperatura máxima de 1900 ºC, bajando hasta 260 ºC aproximadamente, luego de ceder su carga térmica al reactor.
Fig.2. Condiciones de salida del gas de síntesis.
El reformador se simula con 2 reactores, debido a que para las reacciones de conversión y de equilibrio se requiere de un reactor por separado. El primero de ellos es del tipo conversión y en él se llevan a cabo las reacciones de metanación de los hidrocarburos (conversión del 100% a la temperatura de 500 ºC). Los efluentes de este reactor (metano, vapor de agua remanente y CO 2 ) es la alimentación al segundo reactor, que es del tipo equilibrio. Allí se produce la reacción de reformado a 900 ºC, la mayor parte del calor proveniente del horno se destina a esta reacción, ya que la misma es endotérmica. El gas de síntesis obtenido se envía a compresión. El sub Flowsheet de la Planta de Gas de Síntesis se muestra en la Fig. 3.
Fig.3. Sub Flowsheet de la Planta de Gas de Síntesis.
2.2 Planta Compresora
La compresión del gas de síntesis consiste de 2 etapas, con un separador de líquidos previo y un aeroenfriador a la salida de cada etapa. A la salida de la segunda etapa, donde también se une el reciclo proveniente de la planta de metanol, la temperatura es
de 200 ºC; esta última es la temperatura de operación del reactor de metanol. El sub Flowsheet de la Planta Compresora se muestra en la Fig. 4.
Fig.4. Sub Flowsheet de la Planta Compresora.
Los compresores empleados son del tipo centrífugo y ambos operan con una relación de compresión de 2,24. Con estos valores se consigue que a la salida de la planta compresora, la presión del gas de síntesis sea de 50 kgf/cm^2. La corriente de salida de la planta compresora que alimenta al reactor de metanol tiene las siguientes características (Fig. 5).
Fig.5. Condiciones de corriente de salida de planta compresora.
Para la simulación de la planta compresora se emplean los operadores lógicos SET, para establecer las relaciones de compresión de las 2 etapas de la planta y para igualarlas y el operador ADJUST, para ajustar dichas relaciones acorde con la presión a la que se desea salir de la planta. Finalmente, para efectuar la purificación del condensado obtenido del separador de alta presión, se hace uso de un COMPONENT SPLITTER. Para cerrar la simulación entre esta etapa de síntesis de metanol y la planta compresora se hace uso del operador RECYCLE.
2.3 Producción de Metanol
Los gases provenientes de la planta compresora se alimentan al reactor de equilibrio donde se produce la reacción de síntesis de metanol en condiciones isotérmicas, las
Se analizan los rendimientos de cada planta productiva, como así también el rendimiento global de toda la sección y la cantidad de energía neta requerida para lograr los objetivos del proceso, obteniendo una buena performance de la simulación. En la Tabla 2 se muestran las composiciones de los gases de entrada y de salida de la planta como así también el rendimiento de la misma. El calor requerido para mantener la reacción en las condiciones de alta severidad debe ser de 2,5x10^7 kJ/h. En la planta de Compresión se requiere un consumo energético de 603,1 kW en la primera etapa y de 606,3 kW en la segunda, dando un total de 1.209,4 kW netos. Se tiene en cuenta que la eficiencia adiabática de los compresores es de un 75%. En cuanto a la planta de metanol se hace también un análisis de rendimiento tomando como base las corrientes de gases que entran a la planta compresora y que salen del separador ideal final. No se mide en este caso el rendimiento del reactor en sí mismo, ya que en ese caso debería considerarse la corriente de reciclo. El análisis se muestra en la tabla 3.
Tabla 2. Rendimiento de la planta de gas de síntesis.
Composición de HC y CO 2 del gas natural Composición de H 2 , CO y CO 2 del gas de síntesis C1 0,7424 H 2 0, C2 0,2385 CO 0, C3 0,0057 CO 2 0, iC4 0,0008 Total productos 0, nC4 0, iC5 0, nC5 0, nC6 0, CO 2 0, Total reactivos 0,9971 (^) RENDIMIENTO 86,82%
Tabla 3. Rendimiento de la planta de metanol.
Composición de H 2 , CO y CO 2 del gas de síntesis H 2 0, CO 0, CO 2 0, Total productos 0, Flujo molar 7,667 MMSCFD Composición de la corriente de metanol crudo CH 3 OH 0, Flujo molar 0,8485 MMSCFD RENDIMIENTO 12,28%
En esta etapa de la planta se debe extraer un flujo de calor de 6,956x10^6 kJ/h en el reactor de equilibrio (debido a la exotermicidad de la reacción) y 3,744x10^6 del cooler
(para alcanzar las condiciones de separación óptimas). El rendimiento neto de la planta es de 10,66% considerando cantidades molares. Puede realizarse un análisis PINCH más exhaustivo, a fin de conseguir un mayor aprovechamiento de la energía en toda la planta simulada, pero no obstante ello los números muestran valores aceptables, acordes con los estándares reales. Los rendimientos de los productos son los esperados en base a los valores teóricos conocidos. Finalmente, puede observarse que para simular plantas integradas, se requiere de tiempos elevados y toma de decisión compleja que permitan arribar a los objetivos planteados: cambiar los paquetes de fluidos, agregar operadores lógicos y equipos auxiliares, entre otras alternativas.