
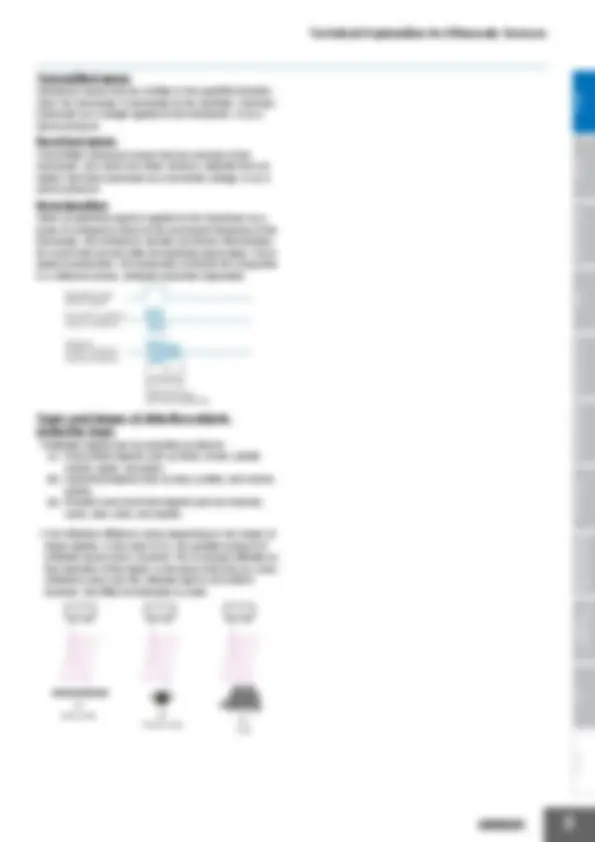
Prepara tus exámenes y mejora tus resultados gracias a la gran cantidad de recursos disponibles en Docsity
Gana puntos ayudando a otros estudiantes o consíguelos activando un Plan Premium
Prepara tus exámenes
Prepara tus exámenes y mejora tus resultados gracias a la gran cantidad de recursos disponibles en Docsity
Prepara tus exámenes con los documentos que comparten otros estudiantes como tú en Docsity
Los mejores documentos en venta realizados por estudiantes que han terminado sus estudios
Estudia con lecciones y exámenes resueltos basados en los programas académicos de las mejores universidades
Responde a preguntas de exámenes reales y pon a prueba tu preparación
Consigue puntos base para descargar
Gana puntos ayudando a otros estudiantes o consíguelos activando un Plan Premium
Comunidad
Pide ayuda a la comunidad y resuelve tus dudas de estudio
Descubre las mejores universidades de tu país según los usuarios de Docsity
Ebooks gratuitos
Descarga nuestras guías gratuitas sobre técnicas de estudio, métodos para controlar la ansiedad y consejos para la tesis preparadas por los tutores de Docsity
A technical explanation of ultrasonic sensors, their features, operating principle, and classifications. Ultrasonic sensors use piezoelectric ceramics to generate electromotive force and detect objects based on the reflection of ultrasonic waves. Reflective and through-beam sensors, their differences, and the impact of temperature and multi-reflection on detection. It also explains the concepts of limit zone, non-sensitive zone, uncertainty zone, and directional characteristics.
Tipo: Guías, Proyectos, Investigaciones
1 / 3
Esta página no es visible en la vista previa
¡No te pierdas las partes importantes!
Sensors
Switches
Safety Components
Relays
Control Components
Automation Systems
Motion / Drives
Environment Measure EquipmentEnergy Conservation Support /
Power Supplies / In Addition
Others
Common
CSM_Ultrasonic_TG_E_1_
The Reflective Ultrasonic Sensor (Distance-adjustable or Zone-setting Convergent Reflective Sensor) sends ultrasonic waves from an emitter toward a sensing object, then receives the reflected waves with a detector. The Sensor uses the resulting information to determine the presence of an object, or to measure the distance to the object. This type of Sensor determines the distance from the Sensor to an object based on the time required from when the ultrasonic waves are sent until they are received using the speed of sound. There are also Through-beam Sensors that detect the presence of an object by detecting the attenuation or interrupted condition of ultrasonic waves caused by an object passing between the emitter and detector.
1. Colors Do Not Influence Detection Unlike photoelectric sensors, Ultrasonic Sensors can detect an object without being influenced by its colors. For example, if two objects have the same shape, even if one is transparent, such as glass, and the other is black plastic, they can both be detected with the same settings. 2. Detecting Objects over a Wide Area Ultrasonic Sensors detect reflection from a wider area than photoelectric sensors, so they can check a wide area all at the same time. 3. Non-Contact Detection Because Ultrasonic Sensors detect sensing objects without touching them, they do not scratch the sensing objects.
Piezoelectric ceramics are used for ultrasonic transmission and reception.
What Are Piezoelectric Ceramics? Piezoelectric ceramics generate electromotive force between the electrodes in proportion to the amount of mechanical force applied to the element. The reverse is also true. If voltage is applied between the electrodes, mechanical displacement is generated proportional to that voltage. From the magnitude of the electromotive force, the presence of an object is detected and the distance from the Sensor to the object is measured.
Classification by Sensing Method
Through-beam
Detects the attenuation or interrupted condition of the ultrasonic beam caused by the object passing between the Emitter and Detector. Typical model: E4E
Reflective
Convergent reflective (Distance adjustable)
Detects only the beam reflected from the object existing within the sensing distance range set with the distance adjuster. Typical model: E4C-UDA
Convergent reflective (Zone setting)
Detects only the beam reflected from the object existing in the sensing range set with the distance selector. Typical model: E4PA-N
Piezoelectric ceramic
SUS
Voltage
Air compression waves Polyvinyl chloride tube
Lead wire
Displacement [mm]
Time Vibrating membrane movement
Voltage [mV]
Time Piezoelectric ceramic electromotive force
Emitter Detector
Sensing object
Unstable range*
Distance adjustment
Sensing object
Sensing object
20 30 40 50 60 70cm A B C E
Unstable range*
D
Sensors
Switches
Safety Components
Relays
Control Components
Automation Systems
Motion / Drives
Environment Measure EquipmentEnergy Conservation Support /
Power Supplies / In Addition
Others
Common
where θ is the air temperature (°C). The speed of sound changes as the air temperature changes, and this results in temperature-based distance measurement error.
Ultrasound waves move straight forward in a uniform medium, and are reflected and transmitted at the boundary between differing media. This phenomenon is affected by the type and shape of the media. A human body in air causes considerable reflection and can be easily detected.
This occurs when ultrasound waves that have already reflected from the detection object once reflect from the sensor head surface, nearby walls, or the ceiling back to the detection object, and then back to the sensor. For example, in the case of double reflection, the same ultrasound waves are received as a single reflection but at twice the distance.
Not only the maximum detection distance but also the minimum detection distance can be adjusted, in connection with or independently of the maximum distance. This detection range is called the limit zone (zone limit).
The non-sensitive zone is the interval between the surface of the sensor head and the minimum detection distance resulting from detection distance adjustment. The uncertainty zone is the area close to the sensor where detection is not possible due to the sensor head configuratin and reverberations. Detection may occur in the uncertainty zone due to multi- reflection between the sensor and the object.
The ratio of the sound output (needed to transmit the specified sound energy to the target object) of the non-directivity emitter to the sound output of the directivity emitter is called the directivity gain. As the frequency and vibration area increase, the directivity grows sharper and sound waves are emitted with greater efficiency. The directivity of a sensor unit used as an ultrasound switch is 8° to 30° (sound pressure half-angle). The directivity is also strongly affected by the shape of the sensor horn and the vibration mode of the transducer, and thus the sensor unit shape, operation frequency, and transducer type are selected to provide the desired operation range.
An index of directivity. The half angle is the angle from the center of the tranducer where the sound level (sound strength) is a maximum, to the point where the sound level is 1/2 the maximum (the sound decrease is symmetical, thus the angle is actually twice the above angle).
Directivity is indicated using a graph showing the sound level as a length from the center as the angle is shifted away from the angle of the transducer center, where the sound level (sound strength) is a maximum. As the angle increases from the center, the directivity decreases, and then after a certain point increases. This is called the side lobe, and can result in stray reflection off peripheral objects that will affect the detection characteristics.
This is a device which uses electrical energy to generate ultrasound waves, and which also converts ultrasound vibrational energy into electrical signals. A barium titanate transducer applying piezoelectric effect is normally used in ultrasound switches. The shape can be a disk or a tube.
This is a reflector that concentrates and emits ultrasound waves in a certain direction and also receives waves. The shape and dimensions of the horn determine the directivity characteristics of the sensor.
Ultrasonic Sensor Sensing object
Detection range Undetection range
Maximum sensing distance
Minimum sensing distance
Minimum sensing distance (fixed)
Unstable range
θ : Sound pressure half angle
Side Lobe
Directional characteristics
Horn