
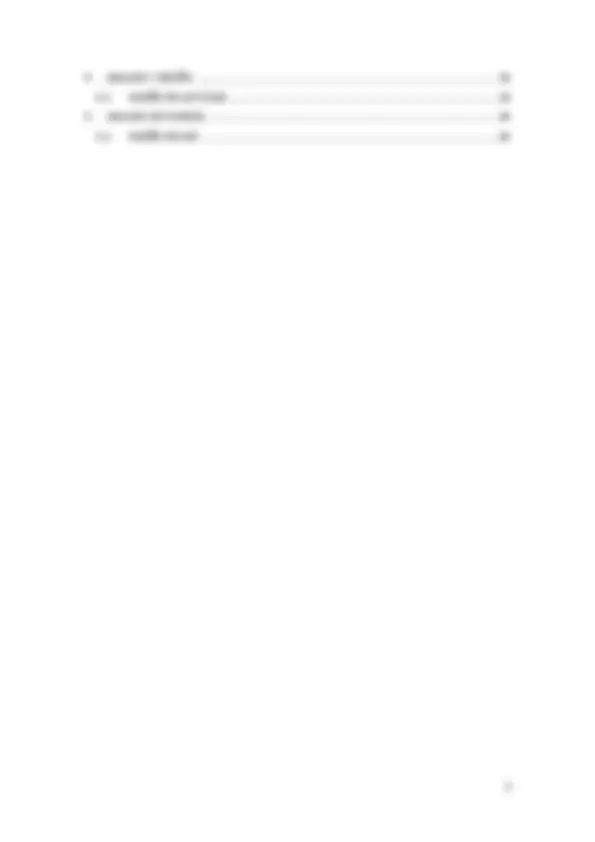
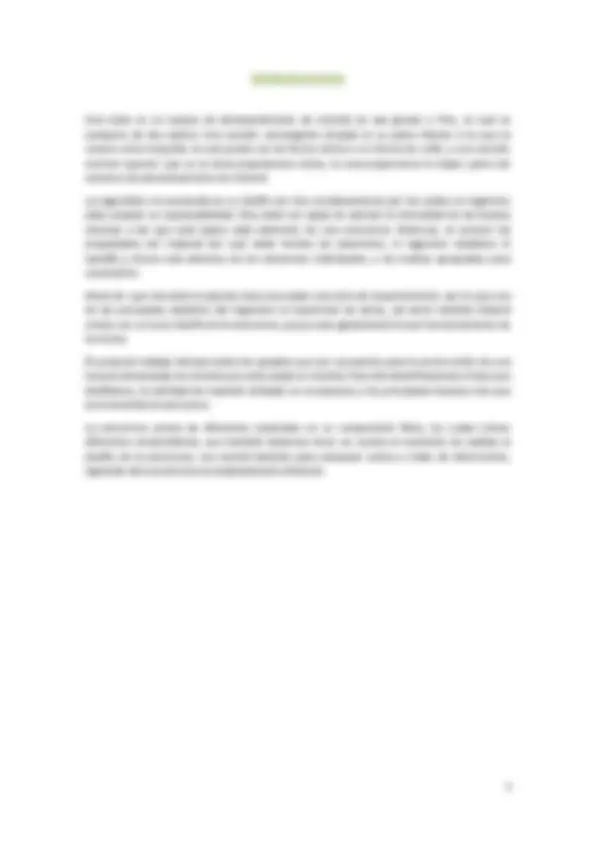
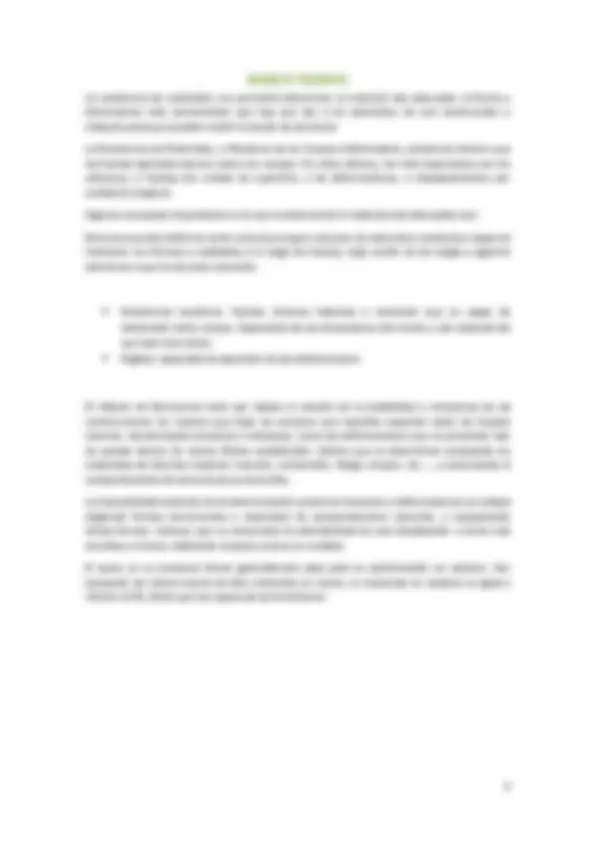
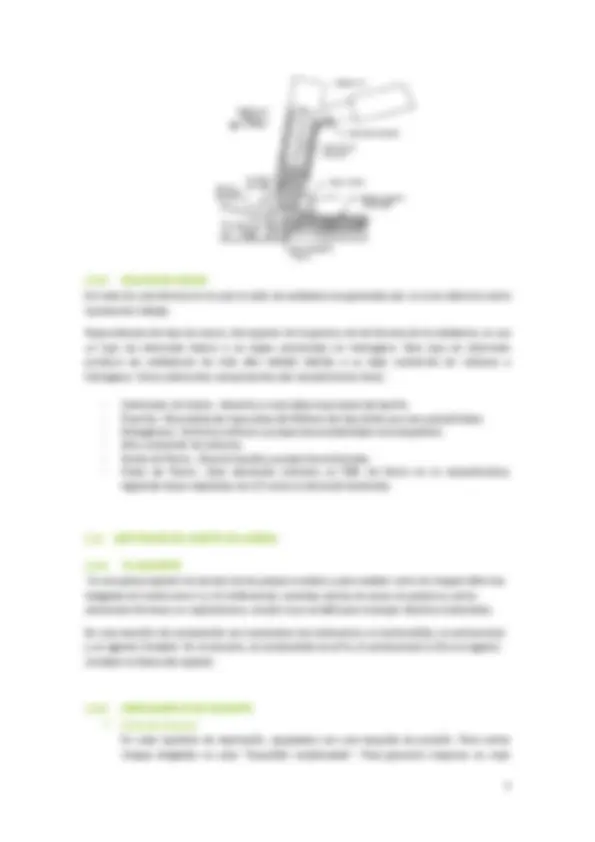
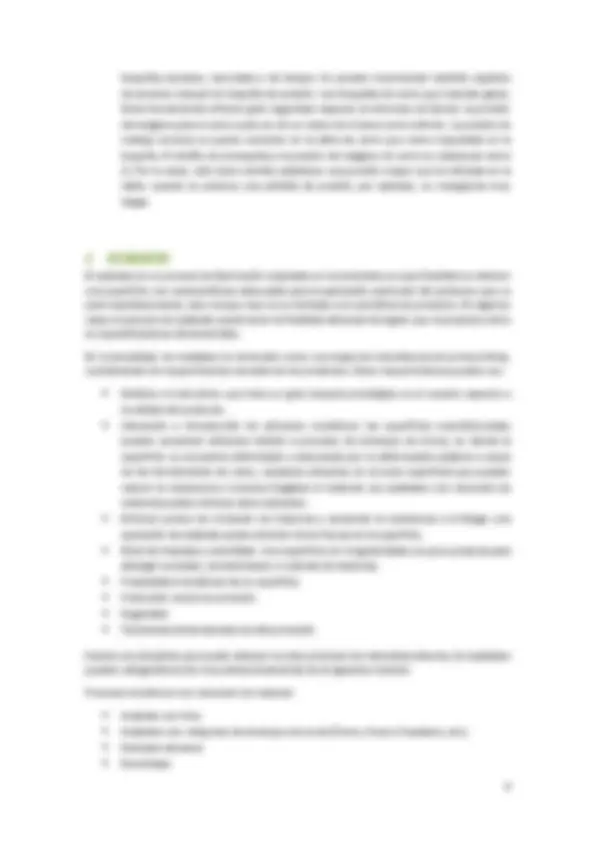
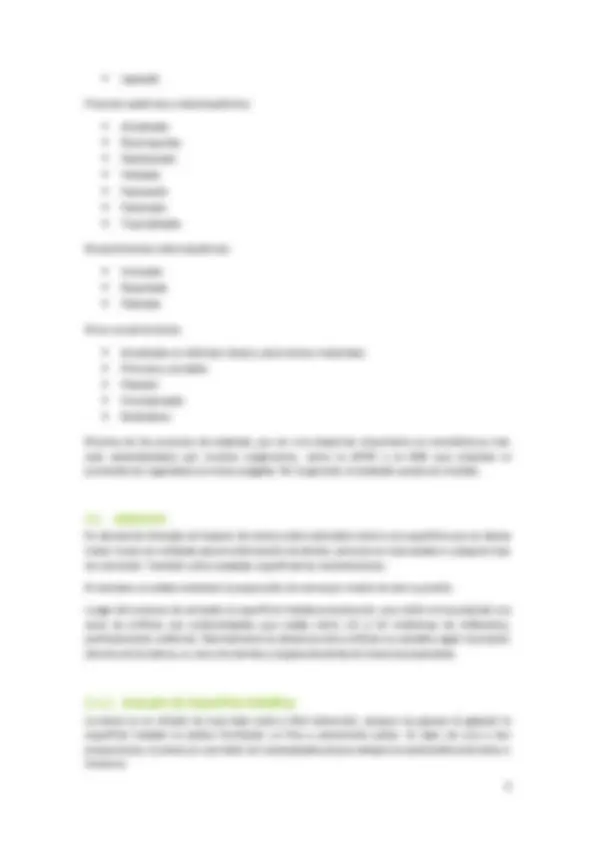
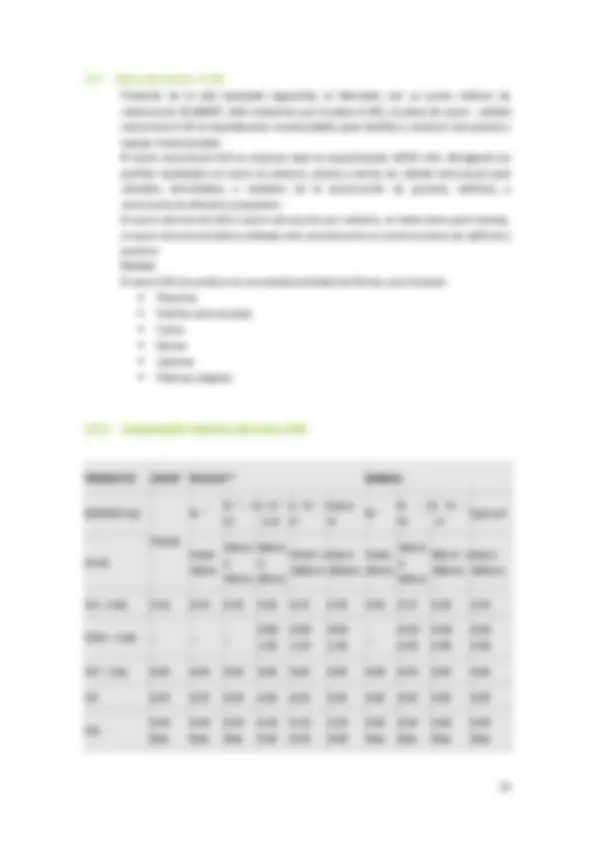
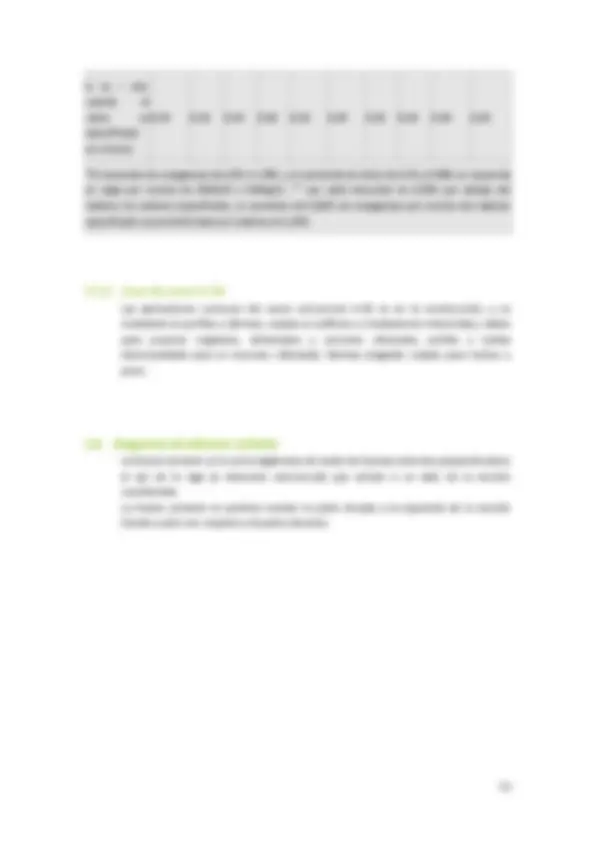
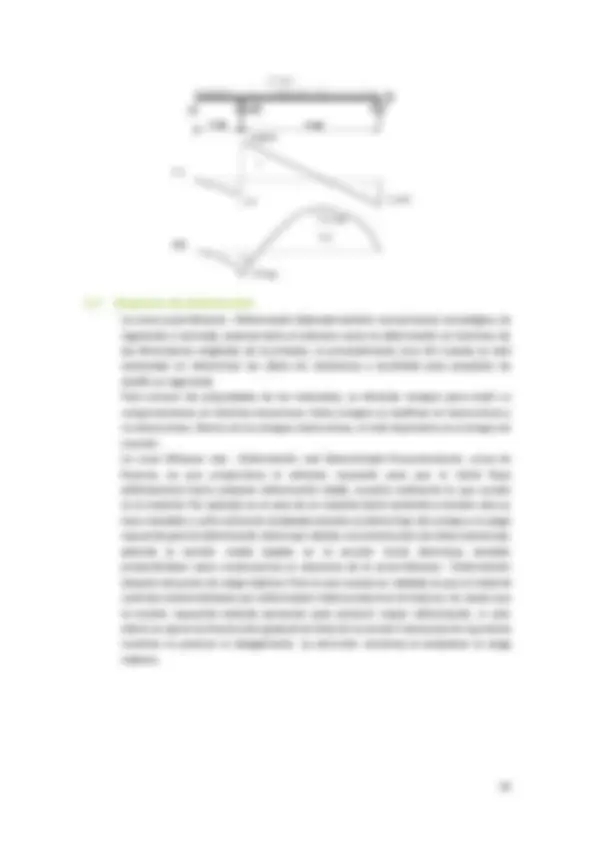
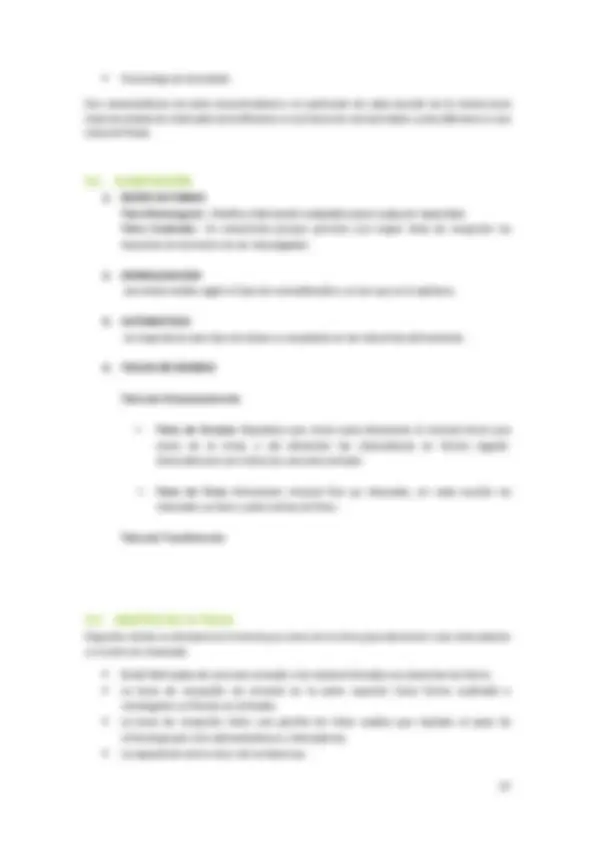
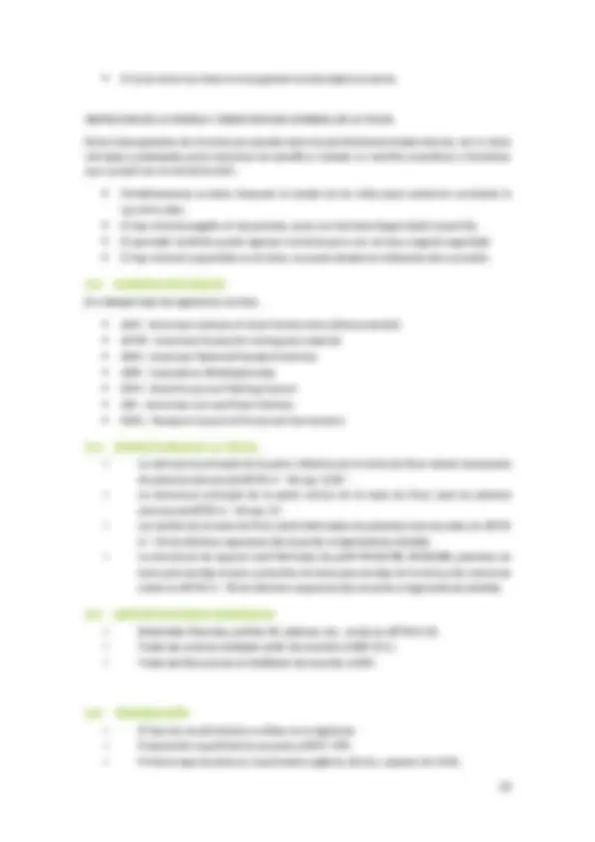
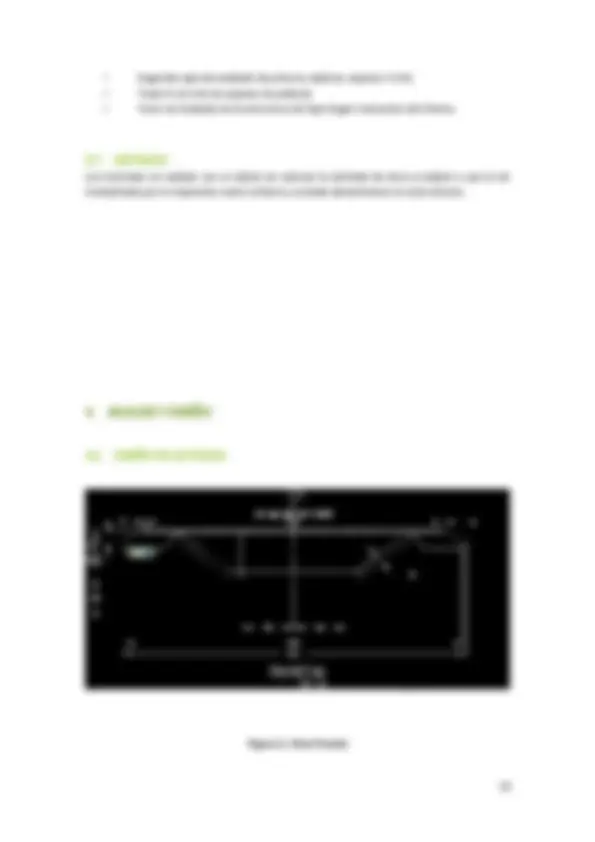
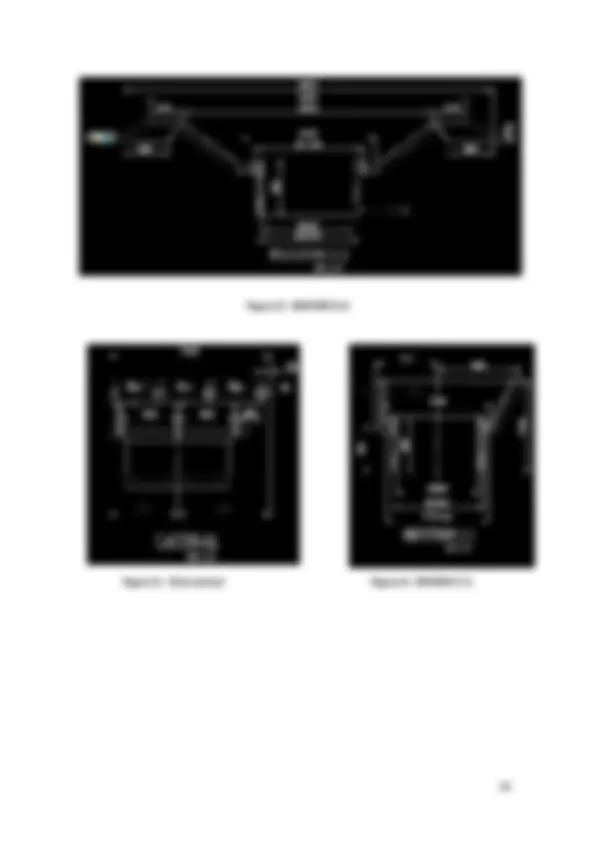
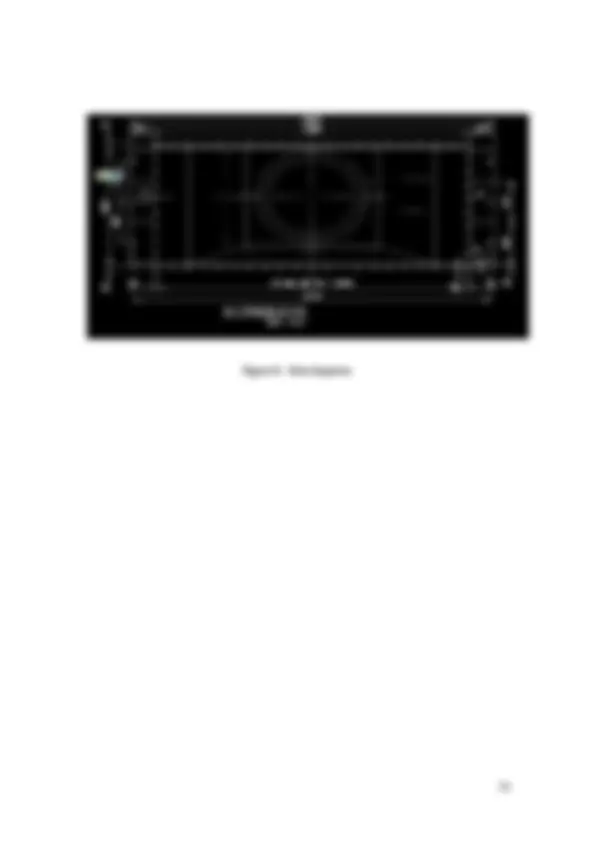
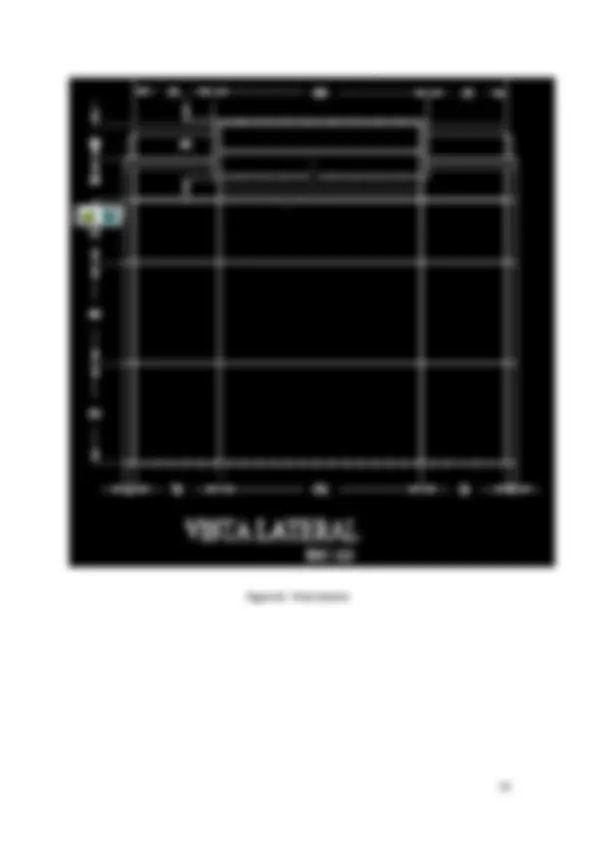
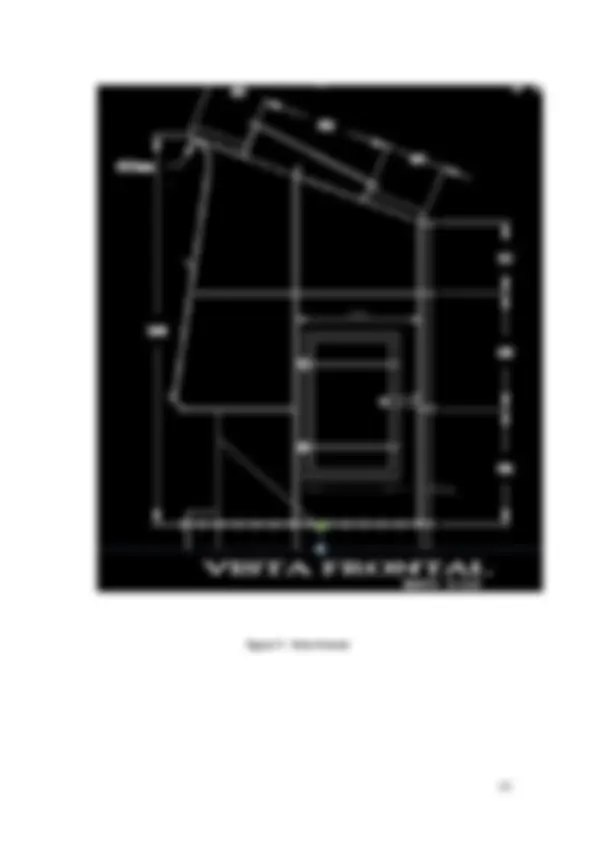
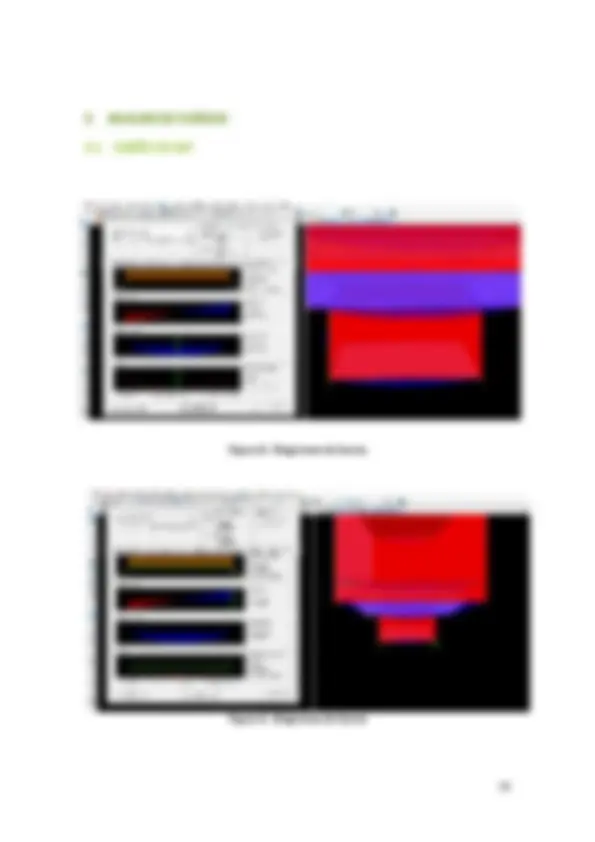
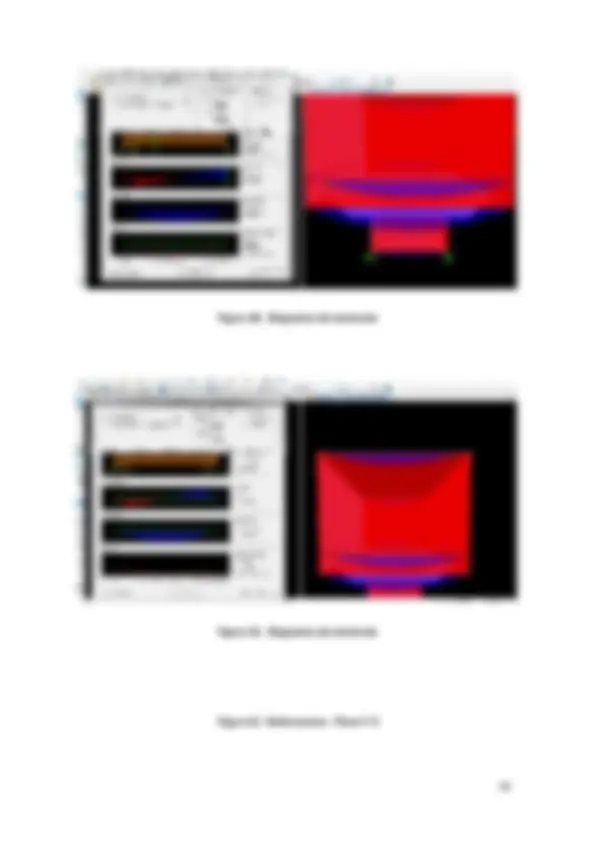
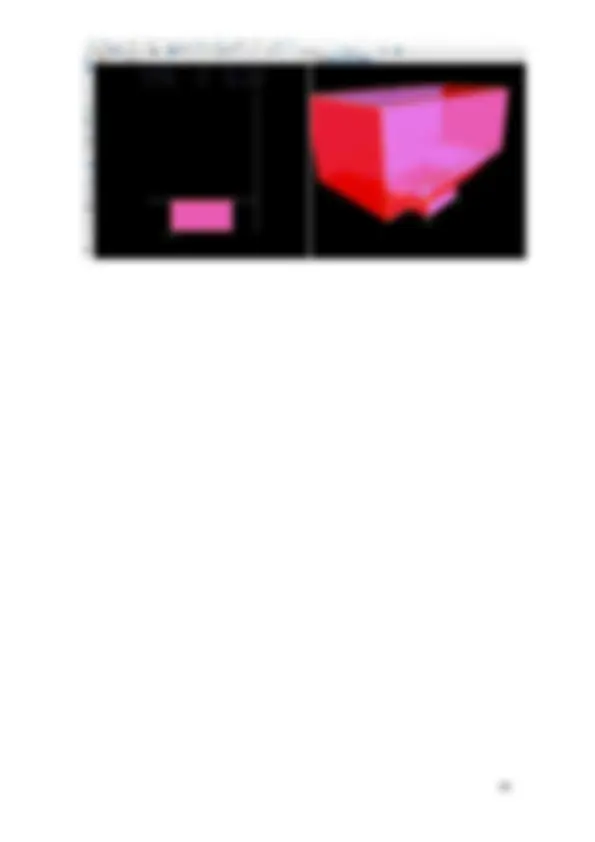
Prepara tus exámenes y mejora tus resultados gracias a la gran cantidad de recursos disponibles en Docsity
Gana puntos ayudando a otros estudiantes o consíguelos activando un Plan Premium
Prepara tus exámenes
Prepara tus exámenes y mejora tus resultados gracias a la gran cantidad de recursos disponibles en Docsity
Prepara tus exámenes con los documentos que comparten otros estudiantes como tú en Docsity
Los mejores documentos en venta realizados por estudiantes que han terminado sus estudios
Estudia con lecciones y exámenes resueltos basados en los programas académicos de las mejores universidades
Responde a preguntas de exámenes reales y pon a prueba tu preparación
Consigue puntos base para descargar
Gana puntos ayudando a otros estudiantes o consíguelos activando un Plan Premium
Comunidad
Pide ayuda a la comunidad y resuelve tus dudas de estudio
Descubre las mejores universidades de tu país según los usuarios de Docsity
Ebooks gratuitos
Descarga nuestras guías gratuitas sobre técnicas de estudio, métodos para controlar la ansiedad y consejos para la tesis preparadas por los tutores de Docsity
documento para el diseño de tolvas para mineria
Tipo: Guías, Proyectos, Investigaciones
1 / 27
Esta página no es visible en la vista previa
¡No te pierdas las partes importantes!
Una tolva es un equipo de almacenamiento de mineral ya sea grueso o fino, la cual se compone de dos partes: Una sección convergente situada en su parte inferior a la que se conoce como boquilla, la cual puede ser de forma cónica o en forma de cuña, y una sección vertical superior que es la tolva propiamente dicha, la cual proporciona la mayor parte del volumen de almacenamiento de mineral.
La seguridad y la economía en un diseño son dos consideraciones por las cuales un ingeniero debe aceptar su responsabilidad. Este debe ser capaz de calcular la intensidad de las fuerzas internas a las que está sujeto cada elemento de una estructura. Entonces, al conocer las propiedades del material del cual están hechos los elementos, el ingeniero establece el tamaño y forma más efectivos de los elementos individuales, y los medios apropiados para conectarlos.
Antes de que una obra se ejecute tiene que pasar una serie de requerimientos por lo que una de las principales objetivos del ingeniero es supervisar las obras, así como también deberá contar con un buen diseño de la estructura ,ya que esto garantizará el buen funcionamiento de la misma.
El presente trabajo indicara todos los pasados que son necesarios para la construcción de una tova de almacenaje de mineral que será usada en minería. Para ello identificaremos el tipo que diseñamos, la cantidad de material utilizado en el proyecto y las principales fuerzas a las que será sometida la estructura.
La estructura consta de diferentes materiales en su composición física, los cuales tienen diferentes características, que también debemos tener en cuenta al momento de realizar el diseño de la estructura, nos servirá también para comparar costos y tratar de disminuirlos, logrando así una estructura completamente eficiente.
La resistencia de materiales nos permitirá determinar el material más adecuado, la forma y dimensiones más convenientes que hay que dar a los elementos de una construcción o máquina para que puedan resistir la acción de las fuerza
La Resistencia de Materiales, o Mecánica de los Cuerpos Deformables, estudia los efectos que las fuerzas aplicadas ejercen sobre los cuerpos. De estos efectos, los más importantes son los esfuerzos, o fuerzas por unidad de superficie, y las deformaciones, o desplazamientos por unidad de longitud.
Algunos conceptos importantes en lo que es determinar el material más adecuados son:
Estructura puede definirse como estructura aquel conjunto de elementos resistentes capaz de mantener sus formas y cualidades a lo largo del tiempo, bajo acción de las cargas y agentes exteriores a que ha de estar sometido:
Resistencia mecánica: Fuerzas internas máximas o tensiones que es capaz de desarrollar dicho cuerpo. Dependerá de las dimensiones del mismo y del material del que este este hecho Rigidez: capacidad de oposición de las deformaciones
El Cálculo de Estructuras tiene por objeto el estudio de la estabilidad y resistencia de las construcciones de manera que bajo las acciones que aquellas soportan tanto las fuerzas internas -denominadas tensiones o esfuerzos- como las deformaciones que se presentan han de quedar dentro de ciertos límites establecidos. Límites que se determinan ensayando los materiales de diversas maneras -tracción, compresión, fatiga, choque, etc...-, y observando el comportamiento de estructuras ya conocidas.
La imposibilidad existente de la determinación exacta de tensiones y deformaciones se soslaya eligiendo formas estructurales y materiales de comportamiento conocido, o equiparando dichas formas -siempre que se compruebe la admisibilidad de esta idealización- a otras más sencillas; e incluso realizando ensayos previos en modelos
El acero es un producto férreo generalmente apto para la conformación en caliente. Con excepción de ciertos aceros de alto contenido en cromo, el contenido en carbono es igual o inferior al 2%, límite que los separa de las fundiciones.
a. Soldadura ordinaria o de aleación : Método utilizado para unir metales con aleaciones metálicas que se funden a temperaturas relativamente bajas: b. Soldaduras blandas (soldering): son aleaciones de plomo y estaño y, en ocasiones, pequeñas cantidades de bismuto. La temperatura de fusión del metal de aportación es inferior a los 450 º C. c. Soldaduras duras (brazing): se emplean aleaciones de plata, cobre y cinc (soldadura de plata) o de cobre y cinc (latón 60/40). Tiene su punto de fusión superior a los 450 ºC y menor que la temperatura de fusión del metal base. d. Soldadura al arco: La fusión del metal se produce como consecuencia del calor generado por un arco voltaico que se hace saltar entre el electrodo y el metal base, pudiéndose alcanzar temperaturas que superan los 4.000 °C. Puede ser: Con electrodo no consumible de grafito Con electrodo metálico consumible Por arco sumergido. e. Electrodo celulósico : Electrodo celulósico con silicato de sodio y con características de penetración mejoradas; propiedades mecánicas sobresalientes, resaltando su resistencia a la tensión. Recomendado para soldar en todas posiciones en pasos múltiples o sencillos. Fácil desprendimiento de escoria y limpieza rápida.
Dependiendo de la posición relativa entre el electrodo y la pieza, se pueden definir las siguientes posiciones de soldeo:
De todas las anteriores, la soldadura plana es la más deseable ejecutar por su mayor comodidad. Para ejecutar la soldadura vertical ascendente, es necesario dotar con un movimiento oscilatorio al electrodo. Las soldaduras ejecutadas en cornisa o en techo son las llamadas soldaduras en posición, las cuales no son deseables debido a su gran dificultad de ejecución.
Se trata de una técnica en la cual el calor de soldadura es generado por un arco eléctrico entre la pieza de trabajo.
Dependiendo del tipo de acero, del espesor de la pared y de las formas de la soldadura, se usa un tipo de electrodo básico o en bajos contenidos en hidrogeno. Este tipo de electrodo produce las soldaduras de más alta calidad debido a su bajo contenido de carbono e hidrogeno. Como elementos componentes del revestimiento tiene:
Se usa para preparar los bordes de las piezas a soldar y para realizar corte de chapas (láminas delgadas de metal entre 1 y 12 milímetros), tuberías, barras de acero al carbono y otros elementos ferrosos en reparaciones, siendo muy versátil para manejar distintos materiales.
En una reacción de combustión son necesarios tres elementos: el combustible, el comburente y un agente iniciador. En el oxicorte, el combustible es el Fe, el comburente el O2 y el agente iniciador la llama del soplete.
A. Oxicorte manual: Se usan sopletes de aspiración, equipados con una boquilla de presión. Para cortar chapas delgadas se usan “boquillas escalonadas”. Para grosores mayores se usan
Lapeado
Procesos químicos y electroquímicos
Anodizado Electropulido Galvanizado Iridizado Pasivación Pavonado Tropicalizado
Recubrimientos electroquímicos
Cromado Niquelado Plateado
Otros recubrimientos
Anodizado en distintas clases y para ciertos materiales. Pinturas y esmaltes Plastisol Porcelanizado Estándares
Muchos de los procesos de acabado, por ser una etapa tan importante en manufactura, han sido estandarizados por muchos organismos, como la ASTM y la AMS que emplean el promedio de rugosidad y la micro pulgada. Por lo general, el acabado puede ser medido.
Se denomina Arenado al impacto de arena a alta velocidad contra una superficie que se desea tratar. Suele ser utilizado para la eliminación de óxidos, pinturas en mal estado o cualquier tipo de corrosión. También como acabado superficial de revestimientos.
El arenado se realiza mediante la proyección de arena por medio de aire a presión.
Luego del proceso de arenado la superficie tratada presenta (en una visión microscópica) una serie de orificios con profundidades que varían entre 1,5 a 3,5 milésimas de milímetros, perfectamente uniforme. Normalmente la distancia entre orificios es variable según la presión del aire de la tobera, su cono de barrido y la granulometría de la arena proyectada.
La arena es un silicato de muy bajo costo y fácil obtención, aunque sus granos al golpear la superficie tratada se parten formando un fino y penetrante polvo. Al cabo de una o dos proyecciones, la arena en uso debe ser reemplazada porque adopta la característica del talco o la harina.
A la arena a utilizar se la clasifica según la norma ASTM; pasándola por una malla Tyller de tejido metálico de calibres 16 (que permite el paso de granos de arena de 1,18 mm) hasta un mínimo de calibre 30 (pasan granos de hasta 0,6 mm). Normalmente estos granos proyectados con aire a una presión superior a los 6 kgrs/cm2 producirán unas depresiones de 1,5 micras al golpear contra la superficie tratada y partirse.
Si bien puede utilizarse arena de origen marino será indispensable en tal caso lavarla y secarla antes de usar y; posteriormente lavar la superficie arenada con soluciones para remover y neutralizar cualquier vestigio de sal. Es más común el uso de arena proveniente de lecho fluvial.
Se deberá seleccionar cuidadosamente la granulometría, por los siguientes motivos:
Es indispensable que la arena a utilizar esté bien seca para que fluya muy bien en la tolva de “gravedad” que normalmente se utiliza para expulsarla hacia la tobera, caso contrario se obturarán las líneas y se demorará la tarea.
Como la granulometría, la presión del aire suministrado y el pico de la tobera de salida nos definen la profundidad o tamaño de los orificios que producirá la arena en su impacto contra la superficie, y que puede llegar en algunos casos hasta 3,5 milésimas de milímetro; será importante definir previamente el tamaño de los granos constitutivos de la arena a emplear.
El granallado es una técnica de tratamiento de limpieza superficial por impacto con el cual se puede lograr un acabado superficial y simultáneamente una correcta terminación superficial.
Consiste en la proyección de partículas abrasivas (granalla) a gran velocidad (65 - 110 m/s) que, al impactar con la pieza tratada, produce la eliminación de los contaminantes de la superficie.
En líneas generales, es utilizado para:
Limpieza de piezas de fundición ferrosas y no ferrosas, piezas forjadas, etc Decapado mecánico de alambres, barras, chapas, etc Shot Peening (aumenta la resistencia a la fatiga de resortes, elásticos, engranajes, etc.), Limpieza y preparación de superficies donde serán aplicados revestimientos posteriores anticorrosivos (pintura, cauchos, recubrimientos electrolíticos o mecánicos, etc.
Según la norma ISO 12944 el tipo de pintado debe ser según la categoría de corrosión. Según las condiciones de ambiente y el tipo de aplicación que realizara la tolva, hemos determinado
Imprimación etilsilicata de zinc 1x C-Pox Primer IZS Intermedio epoxi 1x C-Pox S130 FD Poliuretano 1x C-Pox Thane RPS HS
Producto de la más avanzada ingeniería, es fabricado con un punto mínimo de cedencia de 36,000PSI. Más resistente que la placa A-283, la placa de acero - calidad estructural A-36 es ampliamente recomendable para diseñar y construir estructuras y equipo menos pesado. El acero estructural A36 se produce bajo la especificación ASTM A36. Abrigando los perfiles moldeados en acero al carbono, placas y barras de calidad estructural para clavados, atornillados, o soldados de la construcción de puentes, edificios, y estructuras de diferente propósitos. El acero estructural A36 o acero estructural con carbono, es hasta hace poco tiempo, el acero estructural básico utilizado más comúnmente en construcciones de edificios y puentes Formas El acero A36 se produce en una amplia variedad de formas, que incluyen: Planchas Perfiles estructurales Tubos Barras Láminas Platinas, ángulos
ESPESOR (in)
TODAS
Sobre 4”
Sobre 4”
(mm)
Hasta 20mm
20mm a 40mm
40mm a 65mm
65mm a 100mm
Sobre 100mm
Hasta 20mm
20mm a 40mm
40mm a 100mm
Sobre 100mm
%C – máx. 0.26 0.25 0.25 0.26 0.27 0.29 0.26 0.27 0.28 0.
%Mn – máx. … … …
%P – máx. 0.04 0.04 0.04 0.04 0.04 0.04 0.04 0.04 0.04 0.
%S 0.05 0.05 0.05 0.05 0.05 0.05 0.05 0.05 0.05 0.
%Si
Max
Max
Max
Max
Max
Max
Max
% Cu – mín. cuando el cobre es especificado en el acero
*El contenido de manganeso de 0.85 a 1.35%, y el contenido de silicio de 0.15 a 0.40% es requerido en vigas por encima de 426lb/ft o 634kg/m. ** por cada reducción de 0,01% por debajo del máximo de carbono especificado, un aumento del 0,06% de manganeso por encima del máximo especificado se permitirá hasta un máximo de 1,35%
Las aplicaciones comunes del acero estructural A-36 es en la construcción, y es moldeado en perfiles y láminas, usadas en edificios e instalaciones industriales; cables para puentes colgantes, atirantados y concreto reforzado; varillas y mallas electrosoldada para el concreto reforzado; láminas plegadas usadas para techos y pisos.
La fuerza cortante es la suma algebraica de todas las fuerzas externas perpendiculares al eje de la viga (o elemento estructural) que actúan a un lado de la sección considerada. La fuerza cortante es positiva cuando la parte situada a la izquierda de la sección tiende a subir con respecto a la parte derecha.
Diagrama esfuerzo-deformación obtenido a partir del ensayo normal a la tensión de una manera dúctil. El punto P indica el límite de proporcionalidad; E, el límite elástico Y, la resistencia de fluencia convencional determinada por corrimiento paralelo (offset) según la deformación seleccionada OA; U; la resistencia última o máxima, y F, el esfuerzo de fractura o ruptura. El punto P recibe el nombre de límite de proporcionalidad (o límite elástico proporcional). Éste es el punto en que la curva comienza primero a desviarse de una línea recta. El punto E se denomina límite de elasticidad (o límite elástico verdadero). No se presentará ninguna deformación permanente en la probeta si la carga se suprime en este punto. Entre P y E el diagrama no tiene la forma de una recta perfecta aunque el material sea elástico. Por lo tanto, la ley de Hooke, que expresa que el esfuerzo es directamente proporcional a la deformación, se aplica sólo hasta el límite elástico de proporcionalidad.
Las vigas son importantes elementos estructurales y mecánicos en ingeniería. El objetivo de este capítulo es determinar los esfuerzos en esos miembros por flexión. Las vigas son comúnmente elementos prismáticos, largos y rectos. Destacando las vigas de acero y aluminio que juegan un papel destacado en la ingeniería estructural como en la mecánica y, las vigas de madera se emplean en la construcción residencial. En la mayor parte de los casos, las cargas son perpendiculares al eje de la viga y normalmente son barras rectas y largas que tienen secciones transversales constantes. La carga transversal de una viga puede consistir en cargas concentradas, en un carga distribuida o una combinación de ambas. Normalmente se clasifican según el modo en que están soportadas (apoyadas) :
Establecer límites para la cantidad de deflexión que pueda sufrir una viga o eje cuando se somete a una carga. Para ello se debe determinar la deflexión y la pendiente. Antes de determinar la pendiente en un punto de una viga, es útil bosquejar la forma flexionada de la viga al cargarla para visualizar los resultados calculados. El diagrama de deflexión del eje longitudinal que pasa por el centroide de cada área transversal de la viga se llama curva elástica. Los soportes que resisten una fuerza (pasador) restringen el desplazamiento y los que resisten un momento (pared fija) restringen la rotación o la pendiente y también el desplazamiento.
Se denomina tolva a un dispositivo similar a un embudo de gran tamaño destinado al depósito y canalización de materiales granulares o pulverizados, entre otros. En ocasiones, se monta sobre un chasis que permite el transporte.
Generalmente es de forma cónica y siempre es de paredes inclinadas como las de un gran cono, de tal forma que la carga se efectúa por la parte superior y forma un cono, la descarga se realiza por una compuerta inferior.
Son muy utilizadas en la construcción de vías férreas, instalaciones industriales, minería, agricultura.
Es necesario tener un criterio aproximado sobre diseño de almacenamiento de minerales. Se sabe que las tolvas de gruesos generalmente tienen la forma de paralelepípedo con un plano inclinado en el fondo para facilitar la descarga y son mayormente de concreto, las de finos son cilíndricas con el fondo cónico y de fierro. Independiente de la concepción de ingeniería de un proyecto de tolva, se desea puntualizar algunos criterios que todo ingeniero debería conocer como concepto básico.
Inclinación del Fondo de Tolvas
El ángulo mínimo de inclinación de una tolva depende de:
Granulometría del mineral Porcentaje de finos
Si la luz entre los rieles es muy grande la chancadora se atora.
Estos trozos grandes de mineral que quedan sobre la parrilla denominados bancos, son a veces retirados y plasteados para reducirlos de tamaño o instalar un martillo neumático o hidráulico que cumpla con la misma función.
Periódicamente se debe chequear el estado de los rieles para mantener constante la luz entre ellos. Si hay mineral pegado en las paredes, picar con barretas largas desde la parrilla. El operador también puede ingresar a la tolva pero con correa y soga de seguridad. Si hay mineral suspendido en la tolva, se puede desatorar utilizando aire a presión.
Se trabajan bajo las siguientes normas:
AISC : American Institute of steel Construction (última edición) ASTM : American Society for testing and material ANSI : American National Standard Institute AWS : Association Welding Society SSPC : Steel Structures Painting Council AISI : American Iron and Steel Institute RCSC : Research Council of Structural Connections
Los metrados se realizan con el objeto de calcular la cantidad de obra a realizar y que al ser multiplicado por el respectivo costo unitario y sumado obtendremos el costo directo.
Figura 1. Vista Frontal