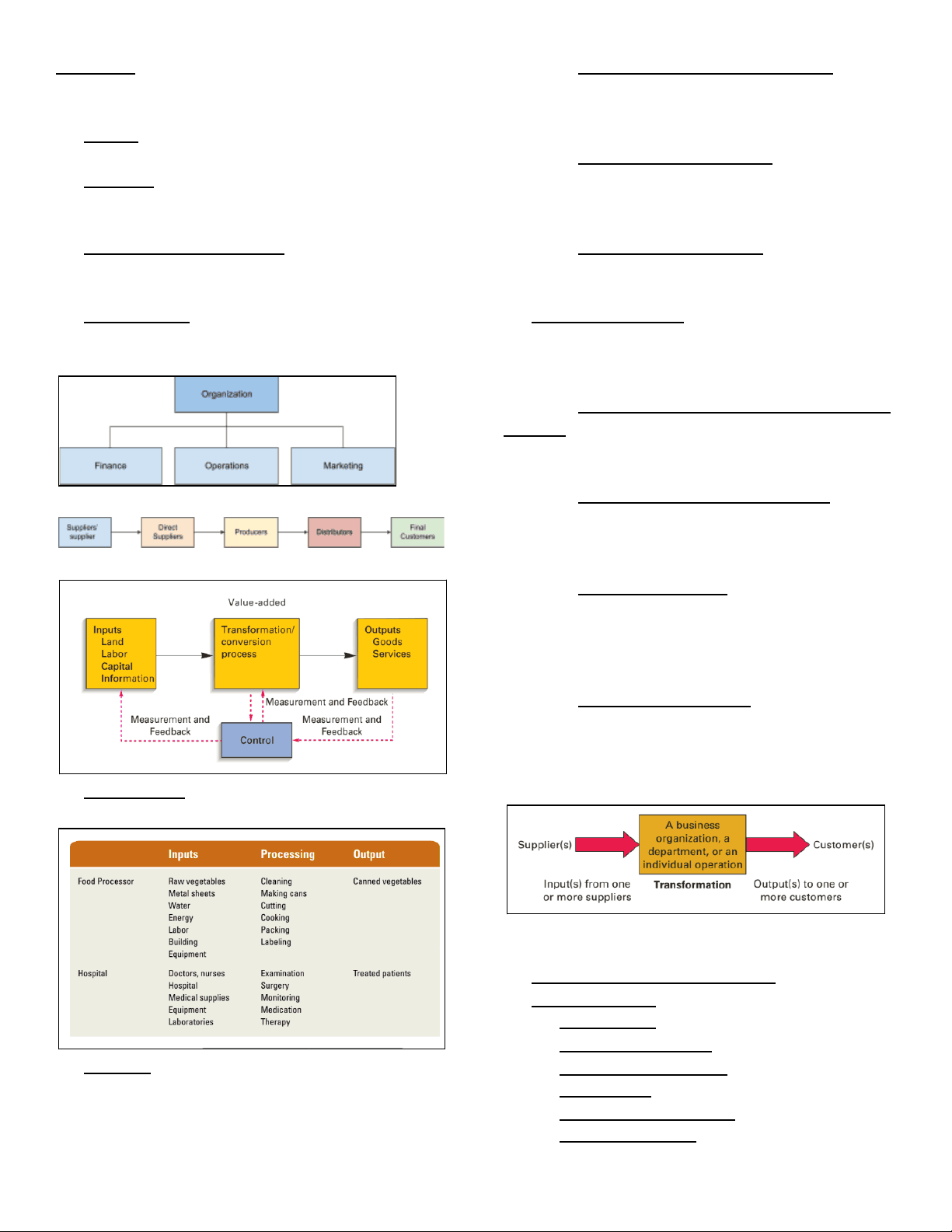
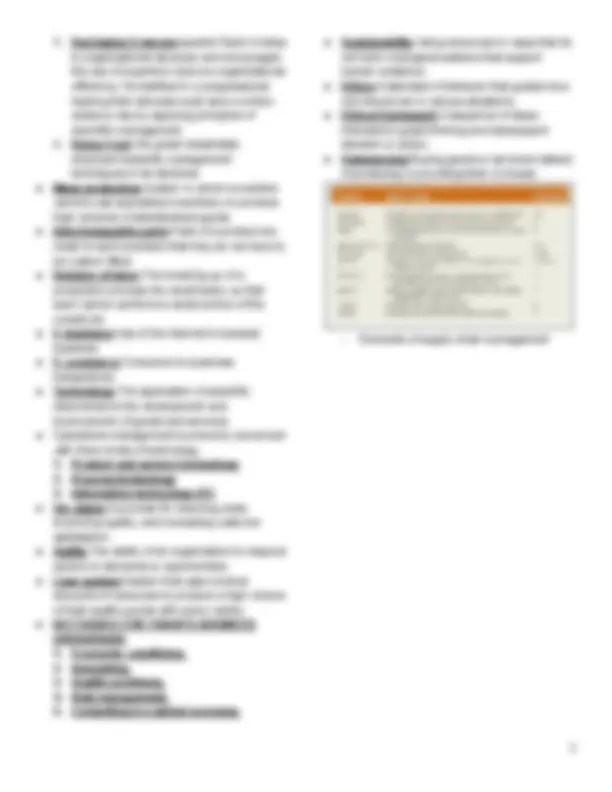
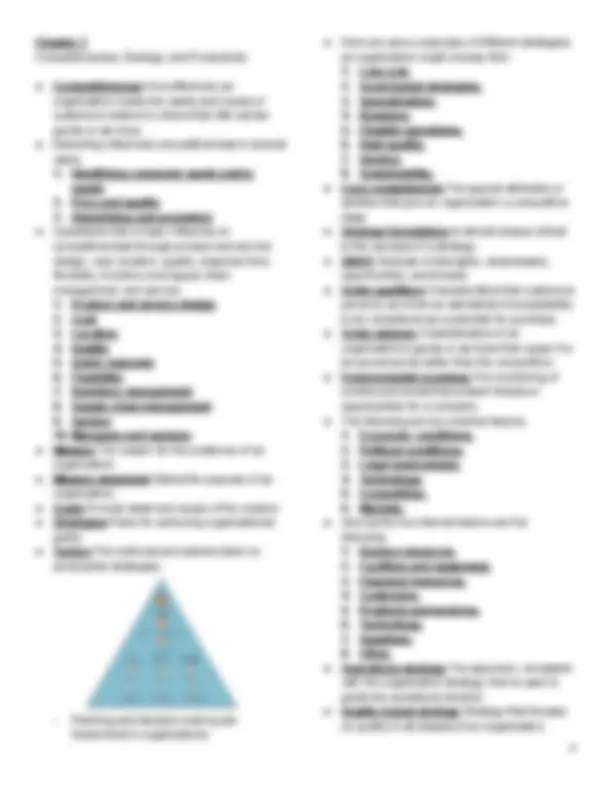
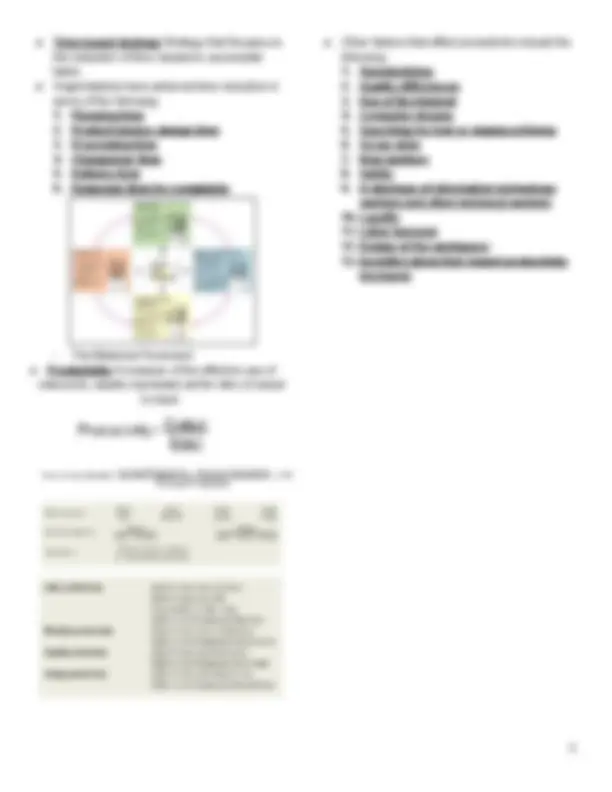
Study with the several resources on Docsity
Earn points by helping other students or get them with a premium plan
Prepare for your exams
Study with the several resources on Docsity
Earn points to download
Earn points by helping other students or get them with a premium plan
Community
Ask the community for help and clear up your study doubts
Discover the best universities in your country according to Docsity users
Free resources
Download our free guides on studying techniques, anxiety management strategies, and thesis advice from Docsity tutors
covers the field of management and the basic unit of it
Typology: Study notes
1 / 7
This page cannot be seen from the preview
Don't miss anything!
On special offer
Chapter 1 Introduction to Operations Management โ Goods Physical items produced by business organizations. โ Services Activities that provide some combination of time, location, form, and psychological value. โ Operations management The management of systems or processes that create goods and/or provide services. โ Supply chain A sequence of activities and organizations involved in producing and delivering a good or service.
**7. Motivating and training employees
Chapter 2 Competitiveness, Strategy, and Productivity โ Competitiveness How effectively an organization meets the wants and needs of customers relative to others that offer similar goods or services. โ Marketing influences competitiveness in several ways,
1. Identifying consumer wants and/or **needs
โ Time-based strategy Strategy that focuses on the reduction of time needed to accomplish tasks. โ Organizations have achieved time reduction in some of the following:
**1. Planning time