
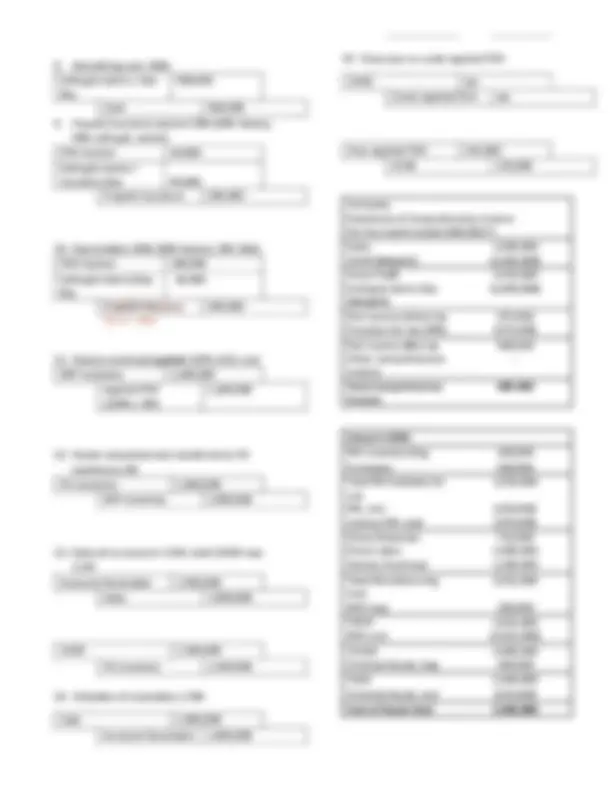
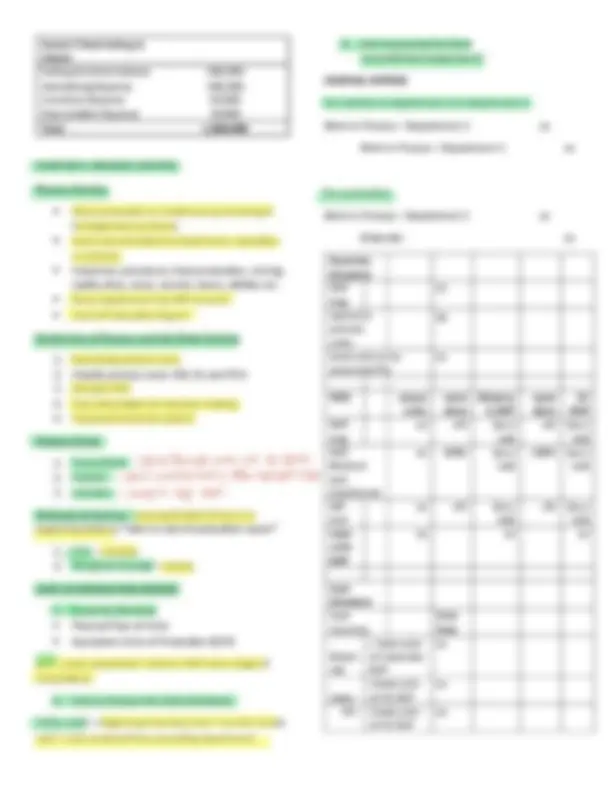
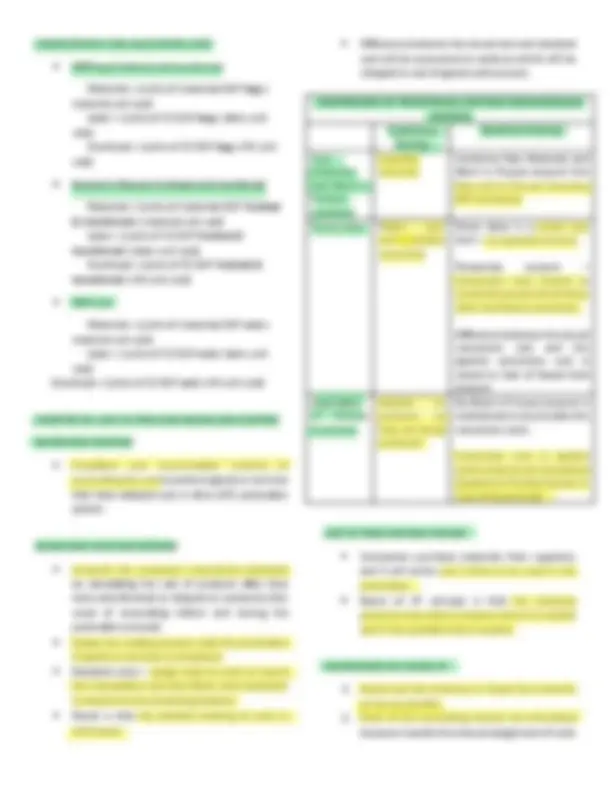
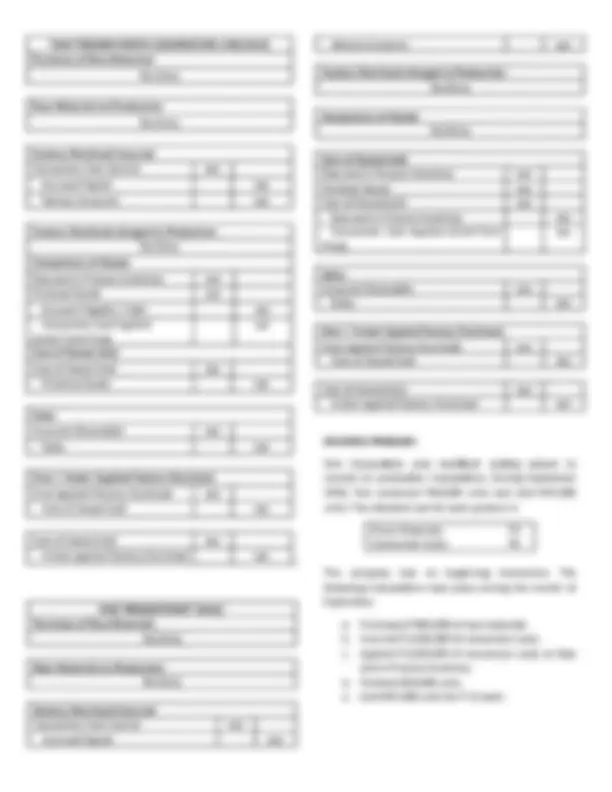
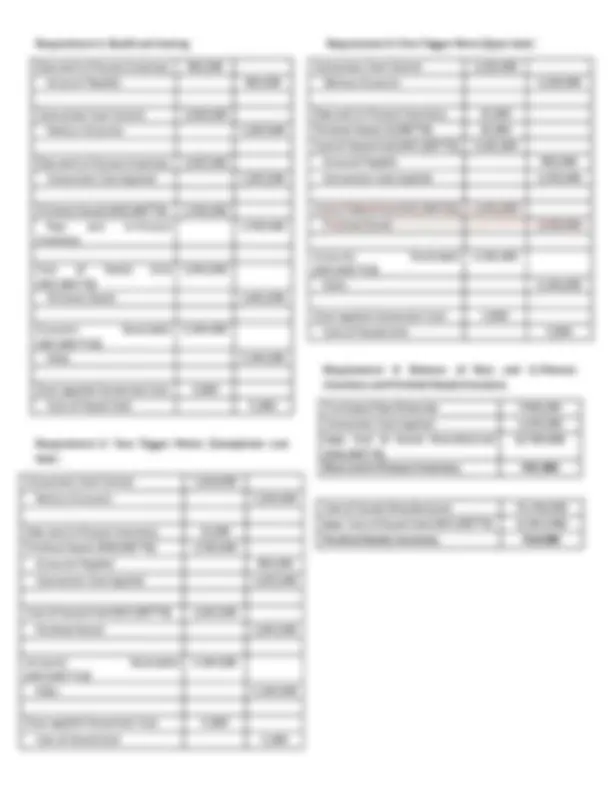
Study with the several resources on Docsity
Earn points by helping other students or get them with a premium plan
Prepare for your exams
Study with the several resources on Docsity
Earn points to download
Earn points by helping other students or get them with a premium plan
Community
Ask the community for help and clear up your study doubts
Discover the best universities in your country according to Docsity users
Free resources
Download our free guides on studying techniques, anxiety management strategies, and thesis advice from Docsity tutors
Summary or highlights the important notes for cost accounting to process costing with minimal example problem.
Typology: Summaries
Uploaded on 04/04/2024
1 document
1 / 9
This page cannot be seen from the preview
Don't miss anything!
Computation of COGS in manufacturing business: RM Inventory Beg. xx Purchases xx Total RM Available for use xx RM, end (xx) Indirect RM used (xx) Direct Materials xx Direct Labor xx Factory Overhead xx Total Manufacturing Cost xx WIP, beg xx TGPIP xx WIP, end (xx) COGM xx Finished Goods, beg xx TGAS xx Finished Goods, end (xx) Cost of Goods Sold xx EXAMPLE PROBLEM: Inventory balances on Aug. 1, 2030, the start of the fiscal year, were as follows: (7/31 end) RM inventory 160, WIP inventory 100, FG inventory 240,
FOH Control (indirect)
WTAX payable 50, Accrued payroll 1,357, Record labor charged to production WIP inventory (direct) 1,000, FOH Control (indirect) 450, Payroll 1,450,
WTAX payable 22, Accrued payroll 453, Record labor charged to production Selling & Admin Salaries
Payroll 500,
Sched 2 Total Selling & Admin Selling & Admin Salaries 500, Advertising Expense 500, Insurance Expense 40, Depreciation Expense 20, Total 1,060, CHAPTER 9: PROCESS COSTING Process Costing Mass production or continuous processing of homogeneous products Cost is accumulated by department, operation or process. Industries: petroleum, food production, mining, textile, tires, wires, cement, beers, utilities etc. Every department has WIP account. Cost of Production Report Similarities of Process and Job-Order Costing
beg xx x% (au x wd) x% (au x wd) WIP finished and transferred xx 100% (au x wd) 100% (au x wd) WP end xx x% (au x wd) x% (au x wd) total units EUP xx xx xx Cost Schedule Cost incurred Unit Cost Mater ials / total units of materials EUP xx Labor /total units of CC EUP xx OH /total units of CC EUP xx
WIP beg finished and transferred Materials = (units of materials EUP beg x material unit cost) Labor = (units of CC EUP beg x labor unit cost) Overhead = (units of CC EUP beg x OH unit cost) Started in Process finished and transferred Materials = (units of materials EUP finished & transferred x material unit cost) Labor = (units of CC EUP finished & transferred x labor unit cost) Overhead = (units of CC EUP finished & transferred x OH unit cost) WIP end Materials = (units of materials EUP end x material unit cost) Labor = (units of CC EUP end x labor unit cost) Overhead = (units of CC EUP end x OH unit cost) CHAPTER 10: JUST IN TIME AND BACKFLUSH COSTING BACKFLUSH COSTING Simplified cost accumulation method of accounting the cost to produce goods or services that have adopted just in time (JIT) production system. BACKFLUSH COSTING METHOD Accounts the company’s inventories backward by calculating the cost of products after they were sold, finished or shipped to customers (the usual of accounting before and during the production process) Delays the costing process until the production of goods or services is completed. Standard costs – assign costs to units to record the transactions and then flush costs backward to determine the remaining balance. Result is that the detailed tracking of costs is eliminated. Difference between the actual cost and standard cost will be accounted as variance which will be charged to cost of goods sold account. COMPARISON OF TRADITIONAL COSTING AND BACKFLUSH COSTING Traditional Costing Backflush Costing Raw Materials and Work in Process Inventory Separate accounts Combines Raw Materials and Work in Process account into Raw and In Process Inventory (RIP Inventory) Direct Labor Major cost and separately accounted Direct labor is a minor cost item – no separate account. Temporary account – Conversion Cost Control to record the actual cost of direct labor and factory overhead. Difference between the actual conversion cost and the applied conversion cost is closed to Cost of Goods Sold account Application of Factory Overhead Applied to products as they are being produced No Work in Process account is maintained to accumulate the conversion costs. Conversion cost is applied when products are completed (Applied to Finished Goods or Cost of Goods Sold) JUST IN TIME COSTING SYSTEM Companies purchase materials from suppliers, and it will arrive just in time to be used in the production. Basics of JIT concept is that the company produces only what is needed, when it is needed and in the quantity that is needed. ADVANTAGES OF USING JIT
Cost of Goods Sold Cost of Goods Sold xxx Finished Goods Inventory xxx Sales Accounts Receivable xxx Sales xxx Over / Under Applied Factory Overhead Over-applied Factory Overhead xxx Cost of Goods Sold xxx Cost of Goods Sold xxx Under-applied Factory Overhead xxx THREE TRIGGER POINTS Purchase of Raw Materials Raw and In Process Inventory xxx Account Payable / Cash xxx Raw Materials to Production No Entry Factory Overhead Incurred Conversion Cost Control xxx Accrued Payroll xxx Various Accounts xxx Factory Overhead charged to Production No Entry Completion of Goods Finished Goods xxx Raw and In Process Inventory xxx Conversion Cost Applied (UnitsUnit Price) xxx Cost of Goods Sold Cost of Goods Sold xxx Finished Goods xxx Sales Accounts Receivable xxx Sales xxx Over / Under Applied Factory Overhead Over-applied Factory Overhead xxx Cost of Goods Sold xxx Cost of Goods Sold xxx Under-applied Factory Overhead xxx TWO TRIGGER POINTS (PURCHASE AND SALE) Purchase of Raw Materials Raw and In Process Inventory xxx Account Payable / Cash xxx Raw Materials to Production No Entry Factory Overhead Incurred Conversion Cost Control xxx Accrued Payroll xxx Various Accounts xxx Factory Overhead charged to Production No Entry Completion of Goods No Entry Cost of Goods Sold Finished Goods xxx Cost of Goods Sold xxx Raw and In Process Inventory xxx Conversion Cost Applied (UnitsUnit Price) xxx Sales Accounts Receivable xxx Sales xxx Over / Under Applied Factory Overhead Over-applied Factory Overhead xxx Cost of Goods Sold xxx Cost of Goods Sold xxx Under-applied Factory Overhead xxx
Purchase of Raw Materials No Entry Raw Materials to Production No Entry Factory Overhead Incurred Conversion Cost Control xxx Accrued Payroll xxx Various Accounts xxx Factory Overhead charged to Production No Entry Completion of Goods Raw and In Process Inventory xxx Finished Goods xxx Account Payable / Cash xxx Conversion Cost Applied (UnitsUnit Price) xxx Cost of Goods Sold Cost of Goods Sold xxx Finished Goods xxx Sales Accounts Receivable xxx Sales xxx Over / Under Applied Factory Overhead Over-applied Factory Overhead xxx Cost of Goods Sold xxx Cost of Goods Sold xxx Under-applied Factory Overhead xxx ONE TRIGGER POINT (SALE) Purchase of Raw Materials No Entry Raw Materials to Production No Entry Factory Overhead Incurred Conversion Cost Control xxx Accrued Payroll xxx Various Accounts xxx Factory Overhead charged to Production No Entry Completion of Goods No Entry Cost of Goods Sold Raw and In Process Inventory xxx Finished Goods xxx Cost of Goods Sold xxx Raw and In Process Inventory xxx Conversion Cost Applied (UnitsUnit Price) xxx Sales Accounts Receivable xxx Sales xxx Over / Under Applied Factory Overhead Over-applied Factory Overhead xxx Cost of Goods Sold xxx Cost of Goods Sold xxx Under-applied Factory Overhead xxx EXAMPLE PROBLEM: Tom Corporation uses backflush costing system to records its production transactions. During September 2030, Tom produced 450,000 units and sold 447, units. The standard cost for each product is: Direct Materials P Conversion Costs P The company had no beginning inventories. The following transactions took place during the month of September. a. Purchased P906,000 of raw materials. b. Incurred P1,820,000 of conversion costs. c. Applied P1,825,000 of conversion costs to Raw and In-Process Inventory. d. Finished 450,000 units. e. Sold 447,000 units for P 12 each.