
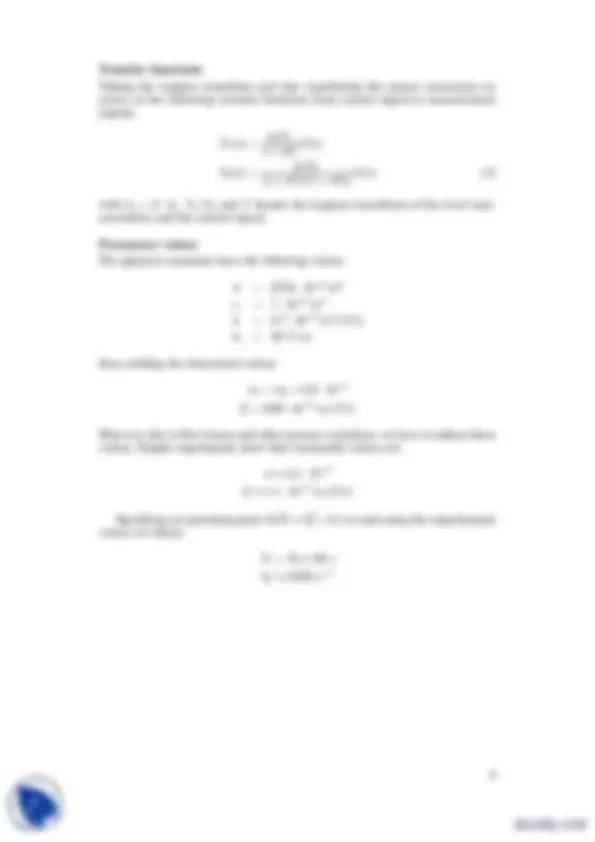
Study with the several resources on Docsity
Earn points by helping other students or get them with a premium plan
Prepare for your exams
Study with the several resources on Docsity
Earn points to download
Earn points by helping other students or get them with a premium plan
Community
Ask the community for help and clear up your study doubts
Discover the best universities in your country according to Docsity users
Free resources
Download our free guides on studying techniques, anxiety management strategies, and thesis advice from Docsity tutors
This handout is related to Fluid Mechanics course. It was distributed by Sajiv Janam at AMET University. It includes: Modeling, Double-tank, Process, Derivation, Linearization, Differential, Equations, Laplace, Transforms, Nonlinear
Typology: Exercises
1 / 2
This page cannot be seen from the preview
Don't miss anything!
We will here briefly derive the transfer functions from control signal to measure- ment signal for the Double-tank process. First, nonlinear differential equations that describe the system are stated. These are linearized around a chosen oper- ating point, and Laplace transforms are taken to obtain the transfer functions. Finally, parameter values are given.
Derivation and linearization of differential equations
Mass balance and Bernoulli’s law give the following differential equation for a tank with cross-section A and outflow area a.
dh dt
− a
2 gh + q (^) in
We now assume that the flow generated by the pump is proportional to the applied voltage, i.e.
q (^) pump ku
This is motivated by the fact that the time constant of the pump is "small" as compared to the tank dynamics. In the same way, assume that the level measurement signal y is proportional to the true level h. Thus we write
y k (^) c h
Since the outflow from the upper tank is the inflow to the lower tank we get the following system of nonlinear differential equations describing the tank process
dh 1 dt
− α (^1)
2 gh 1 + β u
dh 2 dt
α (^1)
2 gh 1 − α (^2)
2 gh 2 ( 1 )
where h 1 and h 2 are the water levels in the upper and lower tank respectively. We also define α (^) i aA^ i (^) i and β (^) Ak 1.
Linearizing around an operating point^1 ( h^01 , h^02 ) yields
d ∆ h 1 dt
∆ h 1 + β ∆ u
d ∆ h 2 dt
∆ h 1 −
∆ h 2 ( 2 )
where we have introduced
α (^1)
2 h^01 g
α (^2)
2 h^02 g
(^1) Note that from ( 1 ) we have the condition h^01 h^02 (
α (^2) α 1 )
(^2).
Transfer functions
Taking the Laplace transform and also considering the sensor conversion we arrive at the following transfer functions from control signal to measurement signals
Y 1 ( s )
k (^) p T 1 1 + sT 1
U ( s )
Y 2 ( s )
k (^) p T 2 ( 1 + sT 1 )( 1 + sT 2 )
U ( s ) ( 3 )
with k (^) p β ⋅ k (^) c. Y 1 , Y 2 and U denote the Laplace transforms of the level mea- surements and the control signal.
Parameter values
The physical constants have the following values
A 2734 ⋅ 10 −^6 m^2 a 7 ⋅ 10 −^6 m^2 k 2. 7 ⋅ 10 −^6 m^3 /( V s ) k (^) c 50 V / m
thus yielding the theoretical values
α 1 α 2 2. 6 ⋅ 10 −^3 β 0. 99 ⋅ 10 −^3 m /( V s )
However, due to flow losses and other process variations, we have to adjust these values. Simple experiments show that reasonable values are
α 2. 1 ⋅ 10 −^3 β 1. 1 ⋅ 10 −^3 m /( V s )
Specifying an operating point of h^01 h^02 0 .1 m and using the experimental values we obtain
T 1 T 2 68 s k (^) p 0. 055 s −^1