
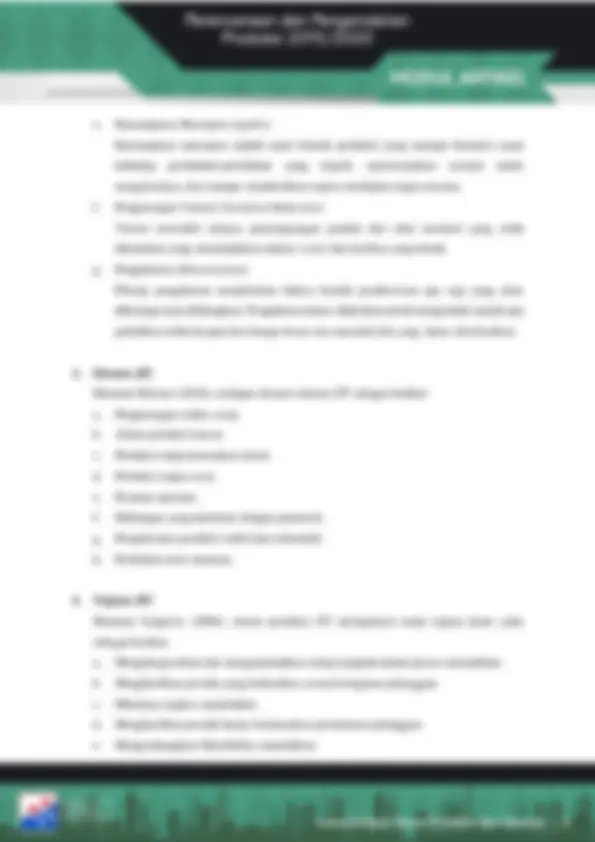
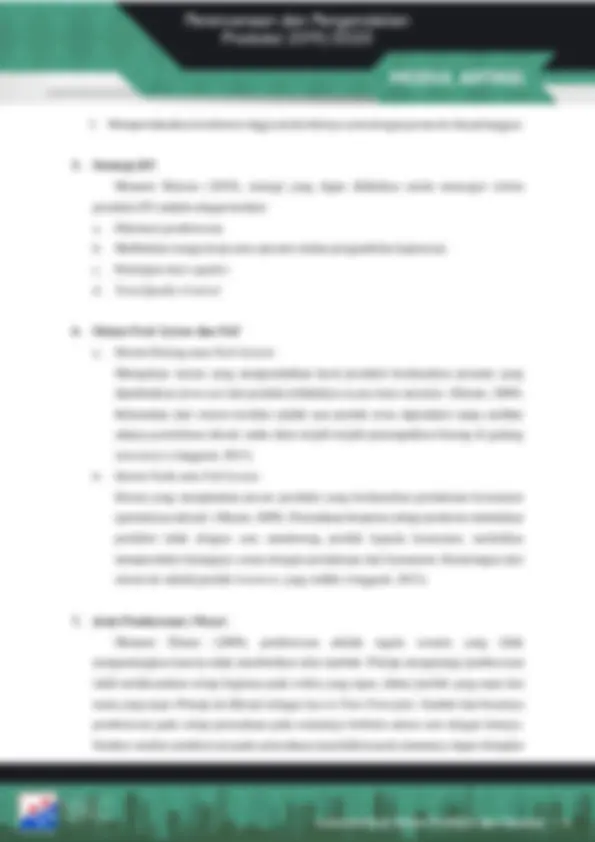
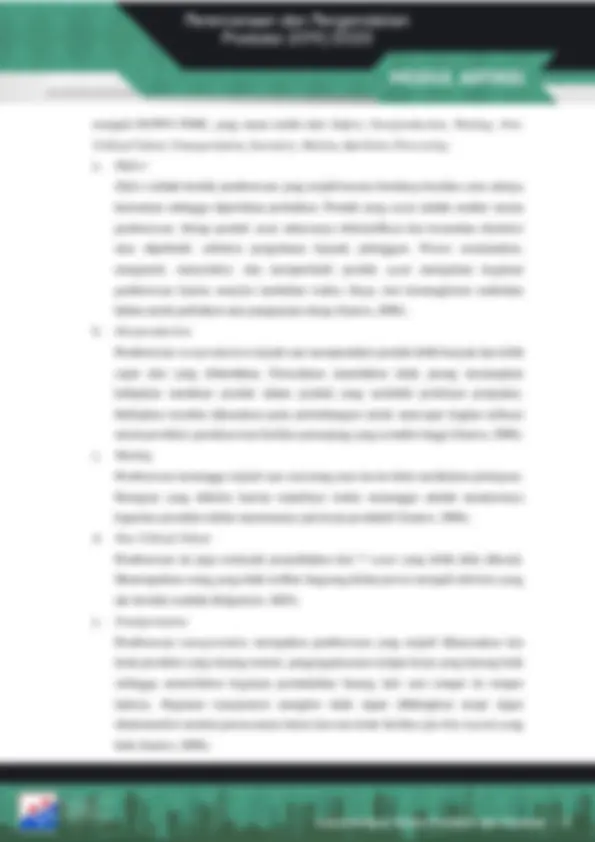
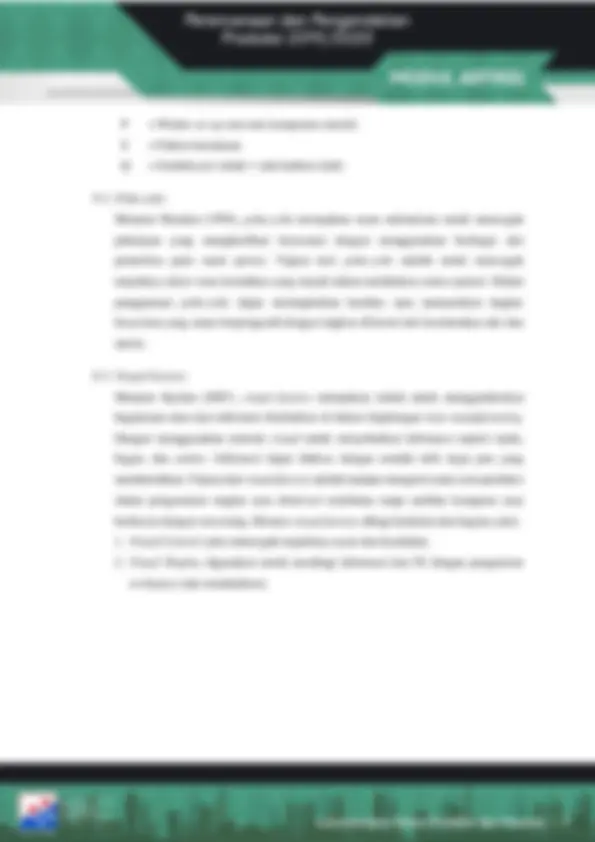
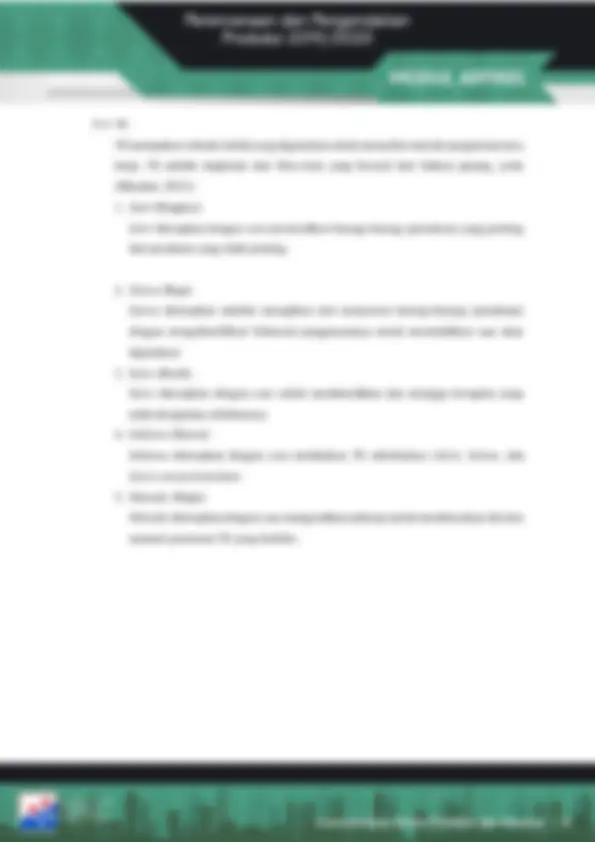
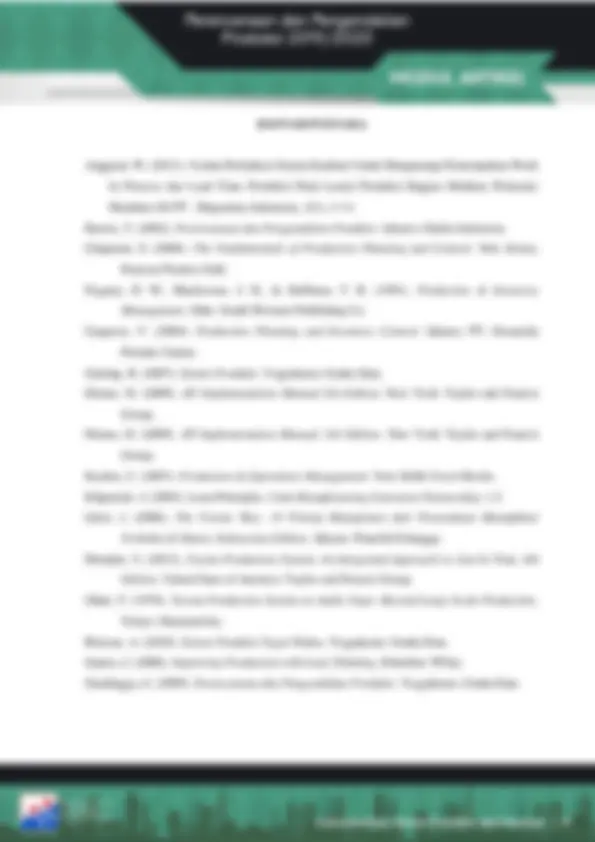
Study with the several resources on Docsity
Earn points by helping other students or get them with a premium plan
Prepare for your exams
Study with the several resources on Docsity
Earn points to download
Earn points by helping other students or get them with a premium plan
Community
Ask the community for help and clear up your study doubts
Discover the best universities in your country according to Docsity users
Free resources
Download our free guides on studying techniques, anxiety management strategies, and thesis advice from Docsity tutors
Just in Time Article Module SISPROMASI
Typology: Lab Reports
1 / 10
This page cannot be seen from the preview
Don't miss anything!
1. Pengertian Just In Time Just in Time (JIT) adalah suatu filosofi yang berfokus pada upaya untuk menghasilkan produk dalam jumlah yang sesuai dengan kebutuhan pelanggan, pada tempat dan waktu yang tepat (Monden, 2012). Konsep dasar dari sistem produksi JIT adalah memproduksi produk yang diperlukan pada waktu dan dalam jumlah yang dibutuhkan untuk setiap tahap proses dalam sistem produksi dengan cara yang paling ekonomis atau paling efisien melalui eliminasi pemborosan dan perbaikan terus-menerus (Ginting, 2007). 2. Prinsip Dasar JIT Menurut Sinulingga (2009), prinsip-prinsip dasar JIT adalah: a. Penyederhanaan ( Simplification ) Penyederhanaan adalah semua bentuk tindakan yang dilakukan untuk membuang atau mengurangi kegiatan yang tidak mengandung nilai tambah. b. Kerapian dan Keteraturan ( Cleanliness and Orderliness ) Menciptakan dan memelihara kerapian dan keteraturan di lantai pabrik, kantor, dan gudang-gudang merupakan keharusan untuk menumbuhkan lingkungan yang asri, nyaman, dan produktif. c. Kejelasan ( Visibility ) Kejelasan adalah untuk menyambungkan kembali atau mendefinisikan kembali informasi sehingga dapat terlihat oleh pekerja di lantai produksi dengan secepatnya. d. Optimasi Waktu Siklus ( Cycle Time Optimization ) Waktu siklus adalah waktu penyelesaian rata-rata selama pengukuran. Konsep waktu siklus merupakan suatu yang fundamental bagi JIT, terutama dengan menghilangkan pemborosan dari waktu siklus kerja yang sudah diperpendek dan mereduksi variasi kerja. Waktu siklus yang sudah diperpendek akan meningkatkan kapasitas produksi.
f. Mempertahankan komitmen tinggi untuk bekerja sama dengan pemasok dan pelanggan.
5. Strategi JIT Menurut Ristono (2010), strategi yang dapat dilakukan untuk mencapai sistem produksi JIT adalah sebagai berikut: a. Eliminasi pemborosan. b. Melibatkan tenaga kerja atau operator dalam pengambilan keputusan. c. Partisipasi dari supplier. d. Total Quality Control. 6. Sistem Push System dan Pull a. Sistem Dorong atau Push System Merupakan sistem yang mengendalikan hasil produksi berdasarkan pesanan yang diperkirakan ( forecast ) dan produksi dilakukan secara terus-menerus (Hirano, 2009). Kelemahan dari sistem tersebut adalah saat produk terus diproduksi tanpa melihat adanya permintaan aktual, maka akan terjadi terjadi penumpukkan barang di gudang ( inventory ) (Anggrait, 2013). b. Sistem Tarik atau Pull System Sistem yang menjalankan proses produksi yang berdasarkan permintaan konsumen (permintaan aktual) (Hirano, 2009). Perusahaan berperan sebagi produsen melakukan produksi tidak dengan cara mendorong produk kepada konsumen, melainkan memproduksi barangnya sesuai dengan permintaan dari konsumen. Keuntungan dari sistem ini adalah jumlah inventory yang sedikit (Anggrait, 2013). 7. Jenis Pemborosan ( Waste ) Menurut Hirano (2009), pemborosan adalah segala sesuatu yang tidak menguntungkan karena tidak memberikan nilai tambah. Prinsip mengurangi pemborosan ialah melaksanakan setiap kegiatan pada waktu yang tepat, dalam jumlah yang tepat dan mutu yang tepat. Prinsip ini dikenal sebagai Just in Time Principles. Sumber dan besarnya pemborosan pada setiap perusahaan pada umumnya berbeda antara satu dengan lainnya. Sumber-sumber pemborosan pada perusahaan manufaktur pada umumnya dapat disingkat
menjadi DOWN-TIME, yang mana terdiri dari Defect , Overproduction , Waiting , Non- Utilized Talent , Transportation , Inventory , Motion , dan Extra-Processing. a. Defect Defect adalah bentuk pemborosan yang terjadi karena buruknya kualitas atau adanya kerusakan sehingga diperlukan perbaikan. Produk yang cacat adalah sumber utama pemborosan. Setiap produk cacat seharusnya diidentifikasi dan kemudian diseleksi atau diperbaiki sebelum pengiriman kepada pelanggan. Proses menemukan, mengenali, menyeleksi, dan memperbaiki produk cacat merupakan kegiatan pemborosan karena menyita tambahan waktu, biaya, dan kemungkinan tambahan bahan untuk perbaikan atau pengerjaan ulang (Santos, 2006). b. Overproduction Pemborosan overproduction terjadi saat memproduksi produk lebih banyak dan lebih cepat dari yang dibutuhkan. Perusahaan manufaktur tidak jarang menetapkan kebijakan membuat produk dalam jumlah yang melebihi perkiraan penjualan. Kebijakan tersebut didasarkan pada pertimbangan untuk mencapai tingkat utilisasi mesin produksi, peralatan atau fasilitas penunjang yang semakin tinggi (Santos, 2006). c. Waiting Pemborosan menunggu terjadi saat seseorang atau mesin tidak melakukan pekerjaan. Kerugian yang diderita karena terjadinya waktu menunggu adalah menurunnya kapasitas produksi akibat menurunnya jam kerja produktif (Santos, 2006). d. Non-Utilized Talent Pemborosan ini juga termasuk penambahan dari 7 waste yang lebih dulu dikenal. Menempatkan orang yang tidak terlibat langsung dalam proses menjadi aktivitas yang tak bernilai tambah (Kilpatrick, 2003). e. Transportation Pemborosan transportation merupakan pemborosan yang terjadi dikarenakan tata letak produksi yang kurang teratur, pengorganisasian tempat kerja yang kurang baik sehingga memerlukan kegiatan pemindahan barang dari satu tempat ke tempat lainnya. Kegiatan transportasi mungkin tidak dapat dihilangkan tetapi dapat diminimalisir melalui perencanaan lokasi dan tata letak fasilitas ( facility layout ) yang baik (Santos, 2006).
c. Mencetuskan ide original d. Menyusun rencana penerapan e. Menerapkan rencana f. Mengevaluasi metode baru
9. Tools JIT 9.1 Kanban Menurut Ristono (2010), kanban merupakan sistem informasi yang menyelaraskan pengendalian produksi suatu produk yang diperlukan dalam jumlah yang diinginkan berdasarkan waktu yang dibutuhkan pada setiap proses produksi. Terdapat dua jenis kanban, yakni: a. Kanban Instruksi Digunakan untuk menunjukkan instruksi operasi pada proses tertentu. Terdapat dua macam kanban instruksi, yaitu production kanban ( non lot production ) dan triangular kanban ( for lot production ). b. Kanban Penarikan Digunakan untuk menunjukkan kapan banyak bagian harus dipindahkan ke lini produksi atau penarikan. Terdapat dua macam kanban penarikan, yaitui interprocess kanban dan supplier kanban. Untuk setiap komponen produk yang mengalir di dalam sistem produksi dengan kanban, harus disertai kanban sebagai bukti dan alat kontrol visual penarikan maupun perintah produksi. Untuk menghitung jumlah perputaran kanban tiap komponen digunakan persamaan berikut (Fogarty, Blackstone, & Hoffman, 1991): Keterangan: N = Jumlah kanban beredar (unit) D = Kebutuhan komponen per menit (unit) M = Waktu tunggu total (menit)
P = Waktu set-up rata-rata komponen (menit) S = Faktor keamanan Q = Jumlah part untuk 1 unit kanban (unit) 9.2 Poka - yoke Menurut Monden (1994), poka - yoke merupakan suatu mekanisme untuk mencegah pekerjaan yang menghasilkan kecacatan dengan menggunakan berbagai alat pemeriksa pada suatu proses. Tujuan dari poka-yoke adalah untuk mencegah terjadinya defect atau kesalahan yang terjadi dalam melakukan suatu operasi. Dalam penggunaan poka-yoke dapat meningkatkan kualitas atau menurunkan tingkat kecacatan yang mana berpengaruh dengan tingkat efisiensi dari keseluruhan alat dan mesin. 9.3 Visual Factory Menurut Kachru (2007), visual factory merupakan istilah untuk menggambarkan bagaimana data dan informasi disebarkan di dalam lingkungan lean manufacturing. Dengan menggunakan metode visual untuk menyebarkan informasi seperti tanda, bagan, dan andon. Informasi dapat diakses dengan mudah oleh siapa pun yang membutuhkan. Tujuan dari visual factory adalah mampu mengerti status area produksi dalam pengamatan singkat atau observasi sederhana tanpa melihat komputer atau berbicara dengan seseorang. Elemen visual factory dibagi kedalam dua bagian yaitu:
Anggrait, W. (2013). Usulan Perbaikan Sistem Kanban Untuk Mengurangi Penumpukan Work In Process dan Lead Time Produksi Pada Lantai Produksi Bagian Medium Prismatic Machines Di PT. Dirgantara Indonesia, 2 (1), 1–11. Baroto, T. (2002). Perencanaan dan Pengendalian Produksi. Jakarta: Ghalia Indonesia. Chapman, S. (2006). The Fundamentals of Production Planning and Control. New Jersey: Pearson Prentice Hall. Fogarty, D. W., Blackstone, J. H., & Hoffman, T. R. (1991). Production & Inventory Management. Ohio: South-Western Publishing Co. Gaspersz, V. (2004). Production Planning and Inventory Control. Jakarta: PT. Gramedia Pustaka Umum. Ginting, R. (2007). Sistem Produksi. Yogyakarta: Graha Ilmu. Hirano, H. (2009). JIT Implementation Manual 2th Edition. New York: Taylor and Francis Group. Hirano, H. (2009). JIT Implementation Manual, 3rd Edition. New York: Taylor and Francis Group. Kachru, U. (2007). Production & Operations Management. New Delhi: Excel Books. Kilpatrick, J. (2003). Lean Principles. Utah Manufacturing Extension Partnership , 1-5. Liker, J. (2006). The Toyota Way: 14 Prinsip Manajemen dari Perusahaan Manufaktur Terhebat di Dunia, Indonesian Edition. Jakarta: Penerbit Erlangga. Monden, Y. (2012). Toyota Production System: An Integrated Approach to Just In Time, 4th Edition. United State of America: Taylor and Francis Group. Ohno, T. (1978). Toyota Production System on Audio Tape: Beyond Large Scale Production. Tokyo: Diamond.Inc. Ristono, A. (2010). Sistem Produksi Tepat Waktu. Yogyakarta: Graha Ilmu. Santos, J. (2006). Improving Production with Lean Thinking. Hokoben: WIley. Sinulingga, S. (2009). Perencanaan dan Pengendalian Produksi. Yogyakarta: Graha Ilmu.