
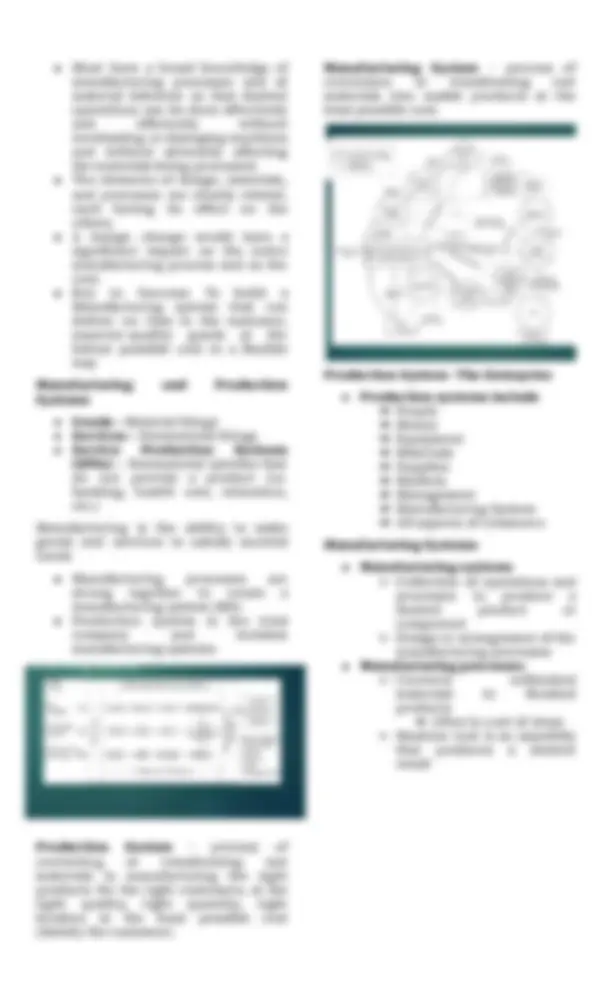
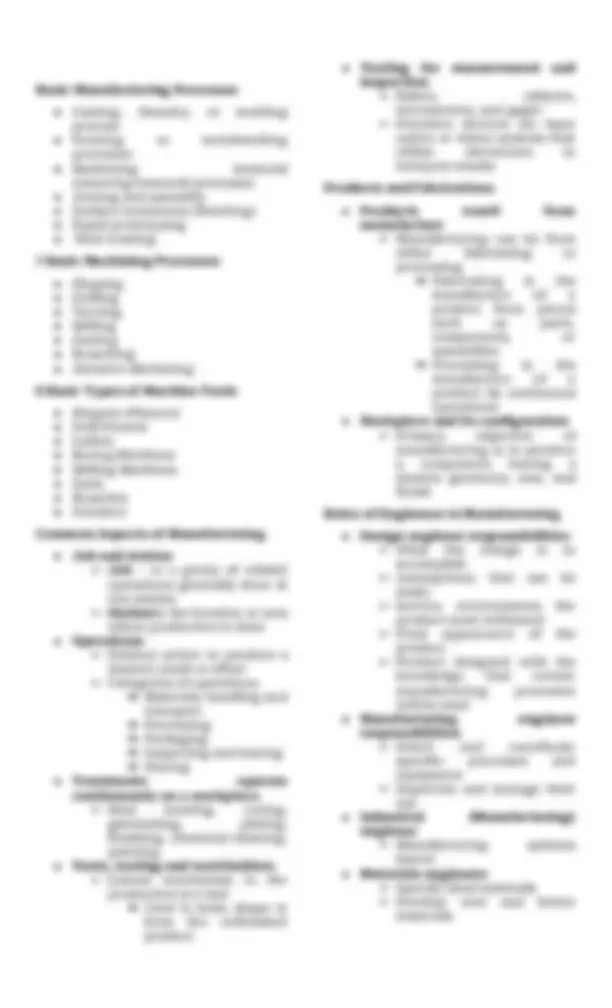
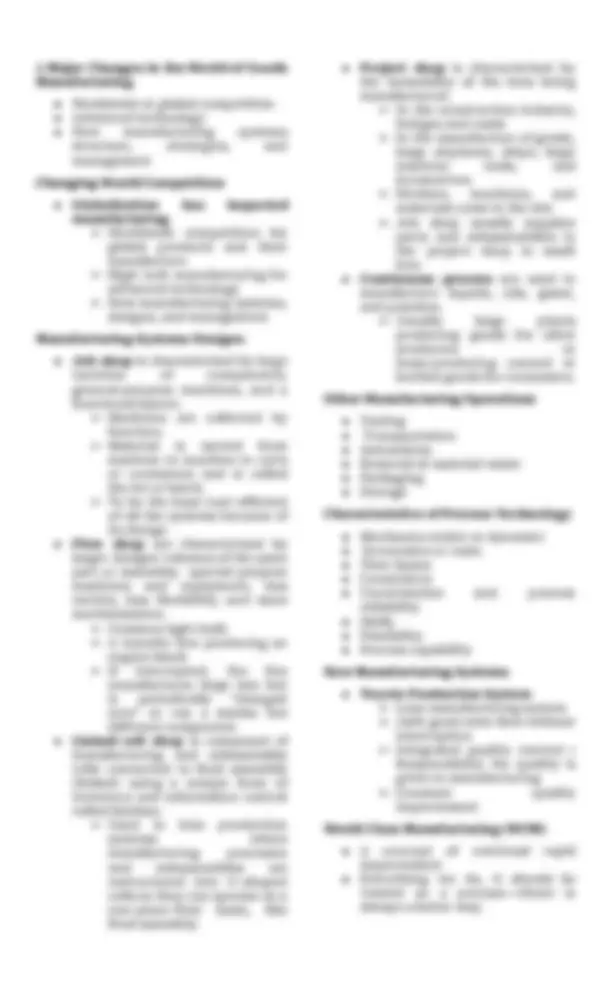
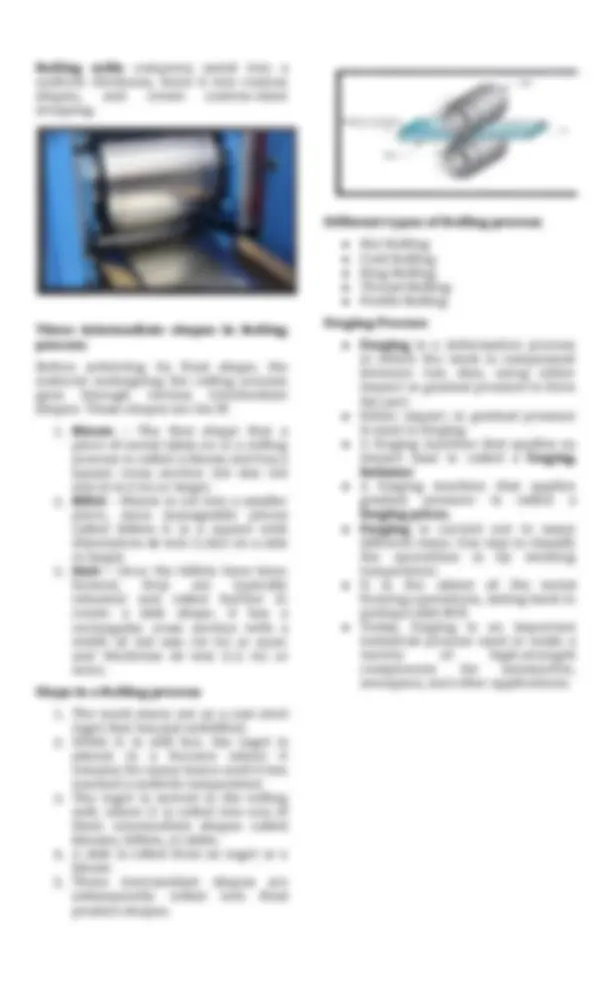
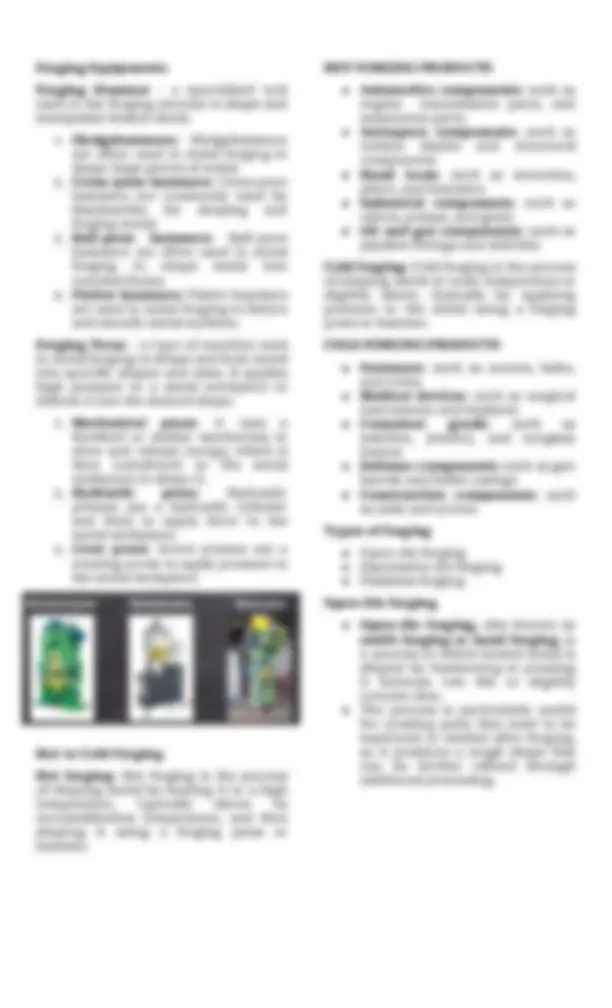
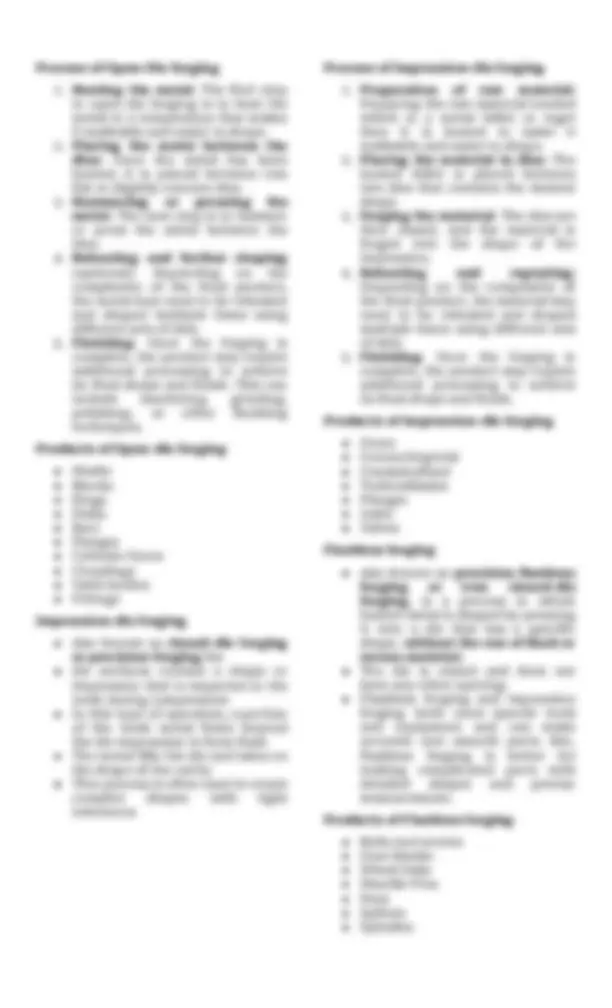
Study with the several resources on Docsity
Earn points by helping other students or get them with a premium plan
Prepare for your exams
Study with the several resources on Docsity
Earn points to download
Earn points by helping other students or get them with a premium plan
Community
Ask the community for help and clear up your study doubts
Discover the best universities in your country according to Docsity users
Free resources
Download our free guides on studying techniques, anxiety management strategies, and thesis advice from Docsity tutors
An overview of the key concepts and principles related to industrial materials and manufacturing processes. It covers topics such as the history of materials development, the relationship between materials, manufacturing, and standard of living, the product development lifecycle, and the interactive factors in manufacturing. The document also discusses the various manufacturing processes, machine tools, and the roles of different engineering disciplines in the manufacturing field. The content is aimed at providing a broad understanding of the materials and processes involved in industrial manufacturing, which is essential for decision-makers, engineers, and technical staff in the industry.
Typology: Lecture notes
1 / 10
This page cannot be seen from the preview
Don't miss anything!
LESSON 1: Introduction to Industrial Materials and Processes ● requires a sound and broad understanding of materials, processes, and equipment on the part of the decision makers, ● accompanied by an understanding of the manufacturing systems Introduction ● All of us live in a world of dynamic change, and materials are no exception. ● The advancement of civilization has historically depended on the improvement of materials to work with. ➔ Over time, they moved from the materials Stone Age into the newer Copper (Bronze) and Iron Ages ➔ Today's competitive manufacturing era of high industrial development and research, is being called the age of mechanization, automation and computer integrated manufacturing. ● Manufacturing is the backbone of any industrialized nation. Since products require materials, engineers should be knowledgeable about the internal structure and properties of materials so that they can choose the most suitable ones for each application and develop the best processing methods. ● Manufacturing and technical staff in industry must know the various manufacturing processes, materials being processed, tools and equipment for manufacturing different components or product with optimal process plan using proper precautions and speci ed safety rules to avoid accidents. ● Future engineers must know the basic requirements of manufacturing activities in terms of man, machine, material methods, money and other infrastructure facilities needed to be positioned properly for optimal shop layouts or plant layout and other support services effectively adjusted or located in the industry or plant with in a well planned manufacturing organization. ● In many cases what was impossible yesterday is a reality today! ➢ Thirty years ago, many people would not have believed that some day computers would become a common household item similar to a telephone or a refrigerator. ➢ And today, we still nd it hard to believe that some day space travel will be commercialized and we may even colonize Mars. History of Materials ● The development of materials and man's ability to process them is linked to the history of man ➔ Stone Age ➔ Copper and Bronze Age ➔ Iron Age ➔ Steel Age ● The current age is that of plastics, composite materials, and exotic alloys New Researchers in the Manufacturing Field ● The advancement has come to this extent that every different aspect of this technology has become a full- edged fundamental and advanced study in itself. ➢ This has led to introduction of optimized design and manufacturing of new products. ➢ New developments in manufacturing areas are deciding to transfer more skill to the machines for considerably reduction of manual labor. ➢ It speci es the need of greater care for man, machine, material and other equipment involving higher initial investment by using proper safety rule and precautions. Materials, Manufacturing, and the Standard of Living ● Standard of living of a society is determined by the goods and services that are available to its people
● Manufactured goods ➔ Producer goods - Intermediate goods used to manufacture either producer or consumer goods ➔ Consumer goods - Purchased directly by the consumer Product Development ● Sustaining technology ➢ Innovations bring more value to the consumer ➢ Improvements in materials, processes, and design ● Product growth normally follows the "S" curve Simpli ed Steps of the Product Life Cycle ● Start up - new product or new company, low volume, small company ● Rapid Growth - products become standardized and volume increases rapidly. Company's ability to meet demand stresses its capacity. ● Maturation - standard designs emerge. Process development is very important. ● Commodity or Declined ➢ Commodity - long-life, standard-of-the-industry type of product or ➢ Decline - product is slowly replaced by improved products The stage of the product life cycle affects ➢ the product design stability ➢ the length of the product development cycle ➢ the frequency of engineering change orders and ➢ the commonality of components Interactive Factors in Manufacturing ● Factors ➔ Product design ➔ Materials ➔ Labor costs ➔ Equipment ➔ Manufacturing cost ● Strategies to reduce cost ➔ Lean manufacturing ➔ Systems approach Manufacturing cost is the largest part of the selling price, usually around 40% The largest part of the manufacturing cost materials usually 50% Materials and Processes ● Manufacturing cost is the largest cost in the selling price. ➢ The largest manufacturing cost is material costs, not direct labor ● Materials, men, methods, and equipment are interrelated factors in manufacturing that must be combined properly to achieve low cost, superior quality, and on-time delivery. ● Materials to be used must be selected and speci ed to meet the design engineer's requirements.
Basic Manufacturing Processes ● Casting, foundry, or molding process ● Forming or metalworking processes ● Machining (material removing/removal) processes ● Joining and assembly ● Surface treatments ( nishing) ● Rapid prototyping ● Heat treating 7 Basic Machining Processes ● Shaping ● Drilling ● Turning ● Milling ● Sawing ● Broaching ● Abrasive Machining 8 Basic Types of Machine Tools ● Shapers (Planers) ● Drill Presses ● Lathes ● Boring Machines ● Milling Machines ● Saws ● Broaches ● Grinders Common Aspects of Manufacturing ● Job and station ➢ Job - is a group of related operations generally done at one station ➢ Station is the location or area where production is done ● Operations ➢ Distinct action to produce a desired result or effect ➢ Categories of operations ➔ Materials handling and transport ➔ Processing ➔ Packaging ➔ Inspecting and testing ➔ Storing ● Treatments operate continuously on a workpiece ➢ Heat treating, curing, galvanizing, plating, nishing. chemical cleaning, painting ● Tools, tooling and workholders ➢ Lowest mechanism in the production is a tool ➔ Used to hold, shape or form the un nished product ● Tooling for measurement and inspection ➢ Rulers, calipers, micrometers, and gages ➢ Precision devices are laser optics or vision systems that utilize electronics to interpret results Products and Fabrications ● Products result from manufacture ➢ Manufacturing can be from either fabricating or processing ➔ Fabricating is the manufacture of a product from pieces such as parts, components, or assemblies ➔ Processing is the manufacture of a product by continuous operations ● Workpiece and its con guration ➢ Primary objective of manufacturing is to produce a component having a desired geometry, size, and nish Roles of Engineers in Manufacturing ● Design engineer responsibilities ➢ What the design is to accomplish ➢ Assumptions that can be made ➢ Service environments the product must withstand ➢ Final appearance of the product ➢ Product designed with the knowledge that certain manufacturing processes will be used ● Manufacturing engineer responsibilities ➢ Select and coordinate speci c processes and equipment ➢ Supervise and manage their use ● Industrial (Manufacturing) engineer ➢ Manufacturing systems layout ● Materials engineers ➢ Specify ideal materials ➢ Develop new and better materials
3 Major Changes in the World of Goods Manufacturing ● Worldwide or global competition ● Advanced technology ● New manufacturing systems structure, strategies, and management Changing World Competition ● Globalization has impacted manufacturing ➢ Worldwide competition for global products and their manufacture ➢ High tech manufacturing for advanced technology ➢ New manufacturing systems, designs, and management Manufacturing Systems Designs ● Job shop is characterized by large varieties of components, general-purpose machines, and a functional layout. ➢ Machines are collected by function. ➢ Material is moved from machine to machine in carts or containers and is called the lot or batch. ➢ To be the least cost-efficient of all the systems because of its design ● Flow shop are characterized by larger designs volumes of the same part or assembly, special-purpose machines and equipment, less variety, less exibility, and more mechanization. ➢ Common light bulb ➢ A transfer line producing an engine block ➢ If interrupted, the line manufactures large lots but is periodically "changed over" to run a similar but different component. ● Linked-cell shop is composed of manufacturing and subassembly cells connected to nal assembly (linked) using a unique form of inventory and information control called Kanban. ➢ Used in lean production systems where manufacturing processes and subassemblies are restructured into U-shaped cells so they can operate on a one-piece- ow basis, like nal assembly. ● Project shop is characterized by the immobility of the item being manufactured. ➢ In the construction industry, bridges and roads ➢ In the manufacture of goods, large airplanes, ships, large machine tools, and locomotives ➢ Workers, machines, and materials come to the site ➢ Job shop usually supplies parts and subassemblies to the project shop in small lots. ● Continuous process are used to manufacture liquids, oils, gases, and powders. ➢ Usually large plants producing goods for other producers or mass-producing canned or bottled goods for consumers. Other Manufacturing Operations ● Testing ● Transportation ● Automation ● Removal of material waste ● Packaging ● Storage Characteristics of Process Technology ● Mechanics (static or dynamic) ● Economics or costs ● Time Spans ● Constraints ● Uncertainties and process reliability ● Skills ● Flexibility ● Process capability New Manufacturing Systems ● Toyota Production System ➢ Lean manufacturing system ➢ 100% good units ow without interruption ➢ Integrated quality control ▷ Responsibility for quality is given to manufacturing ➢ Constant quality improvement World Class Manufacturing (WCM) ● A concept of continual rapid improvement ● Everything we do, it should be viewed as a process-→there is always a better way.
What is Metal Forming?? ● Metal forming involves using mechanical, thermal or chemical methods to shape metals into different sizes and forms. Its main purpose is to create functional and useful products from raw materials like sheets, bars, or rods. ● Deformation results from the use of a tool, usually called a die in metal forming, which applies stresses that exceed the yield strength of the metal. ● This process can be classi ed into two basic categories: bulk deformation processes and sheet metalworking. Die - it is a special tool for forming metallic material, which uses the up-and-down movement of press machine. Advantages ● Cost-effectiveness ● Improved strength and durability ● Enhanced surface nish Disadvantages ● Limited to speci c materials ● High equipment costs ● Environmental concerns Bulk Deformation ● Bulk deformation is a manufacturing process in which a large amount of material is deformed through compressive or tensile forces, resulting in a change in shape or dimensions. ● A process where it re nes the starting shapes, sometimes improving mechanical properties, and always adding commercial value. ● Bulk deformation processes are performed as cold, warm, and hot working operations. ● There are several types of bulk deformation processes, including rolling, forging, extrusion, and drawing , among others. Types of Bulk Deformation ● Rolling ● Forging ● Extrusion ● Drawing Rolling Process ● Rolling is a deformation process in which the thickness of the work is reduced by compressive forces exerted by two opposing rolls. ● The rolls rotate to pull and simultaneously squeeze the work between them ● Most rolling processes are very capital intensive, requiring massive pieces of equipment, called rolling mills,to perform them. ● Most rolling is carried out by hot working, called hot rolling, owing to the large amount of deformation required.
Rolling mills compress metal into a uniform thickness, bend it into custom shapes, and create custom-sized stripping. Three intermediate shapes in Rolling process Before achieving its nal shape, the material undergoing the rolling process goes through various intermediate shapes. Those shapes are the ff:
Process of Open-Die forging