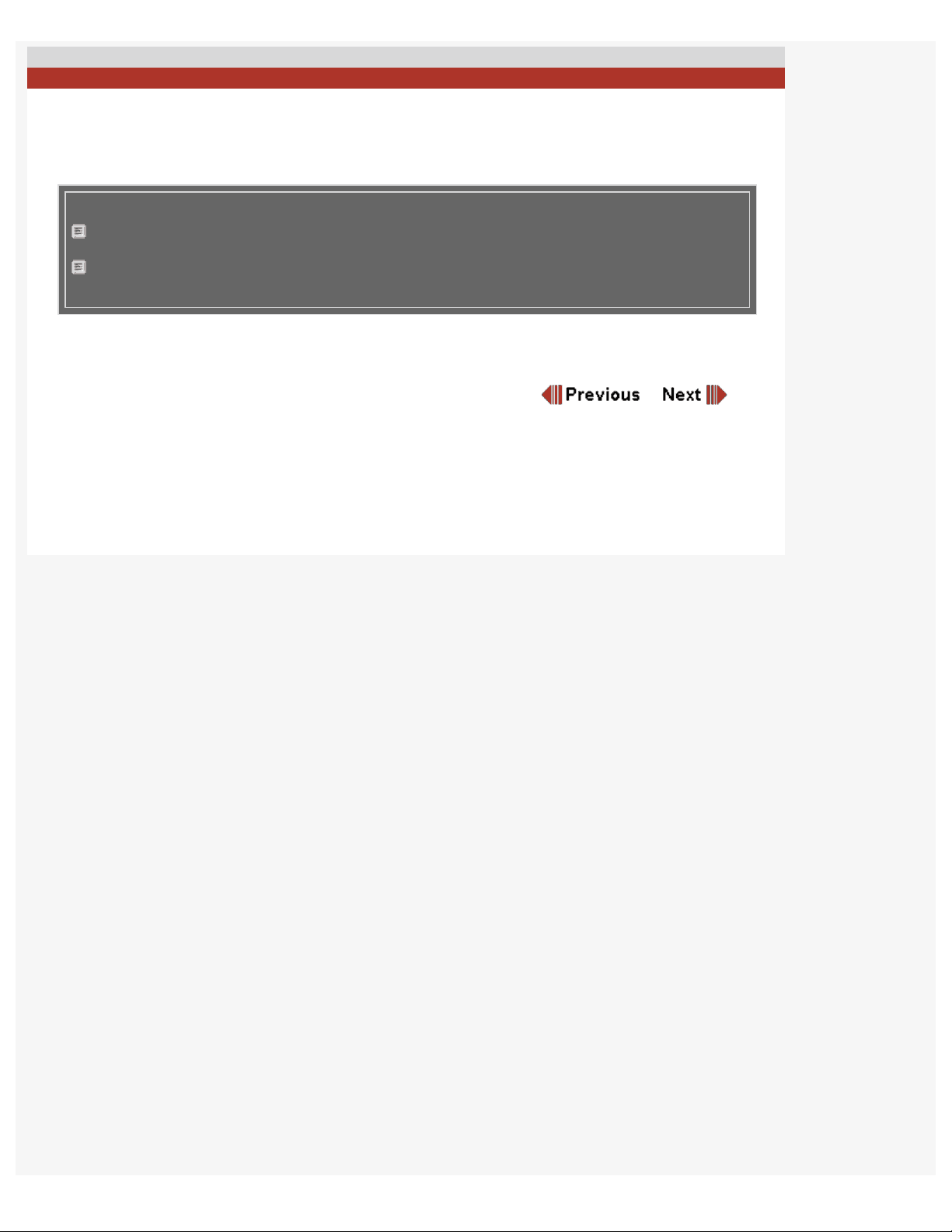
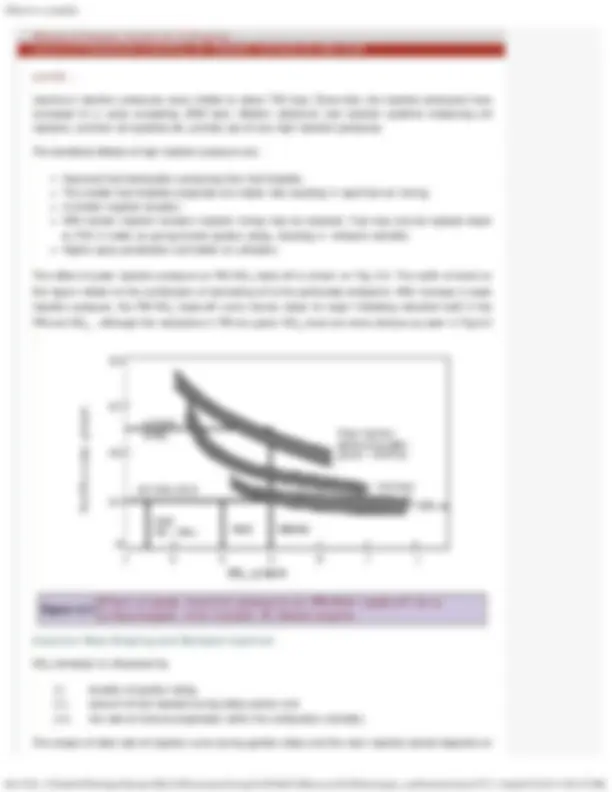
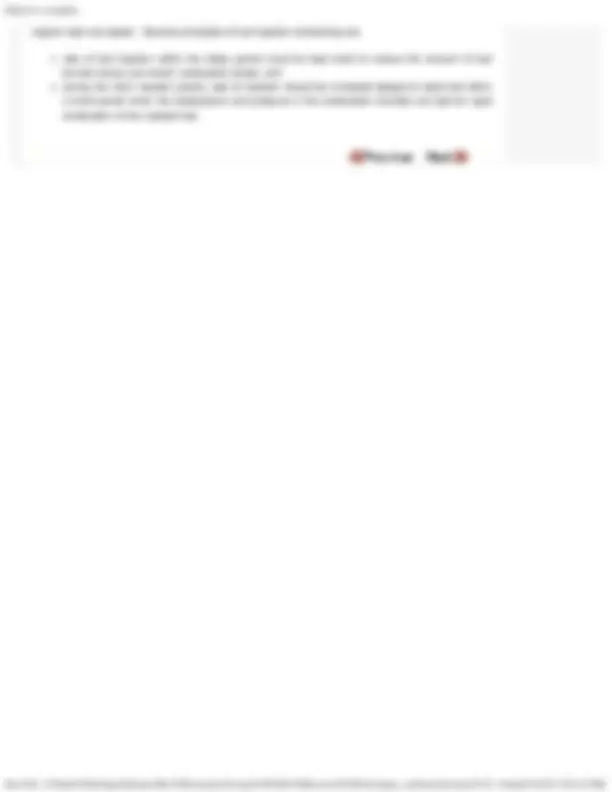
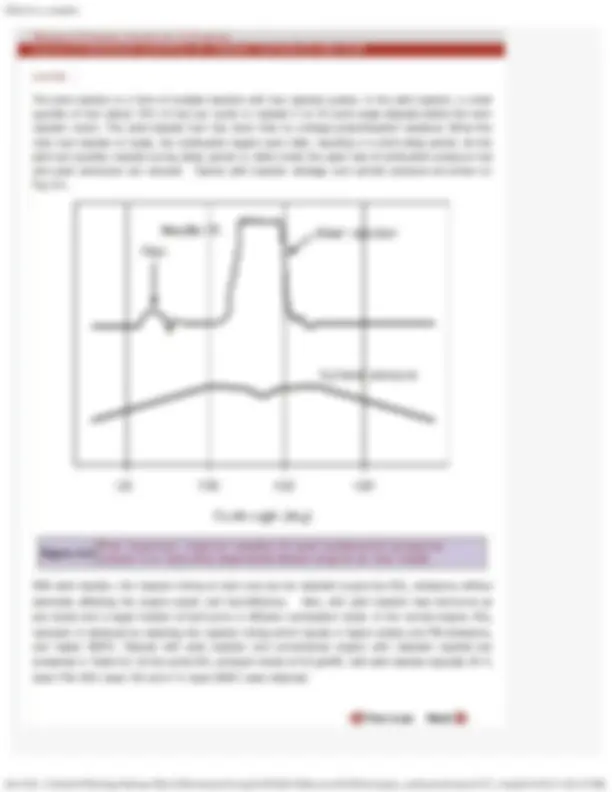
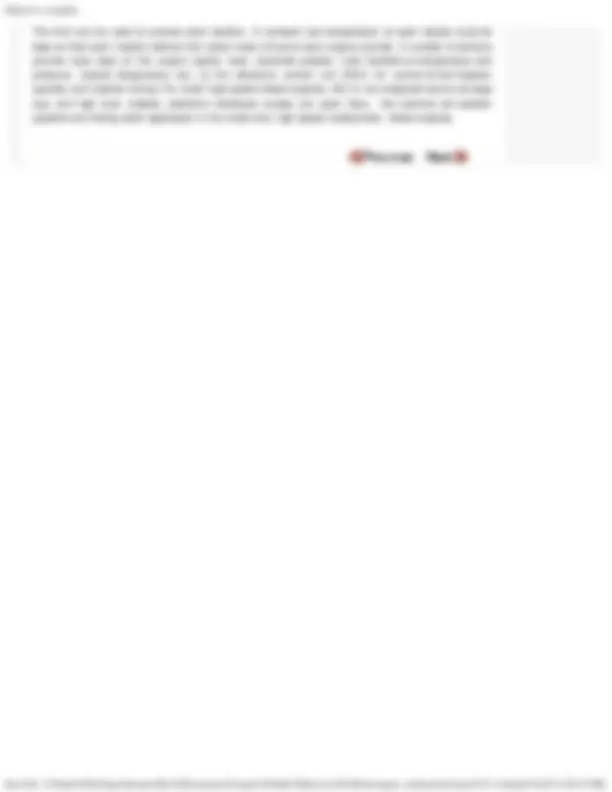
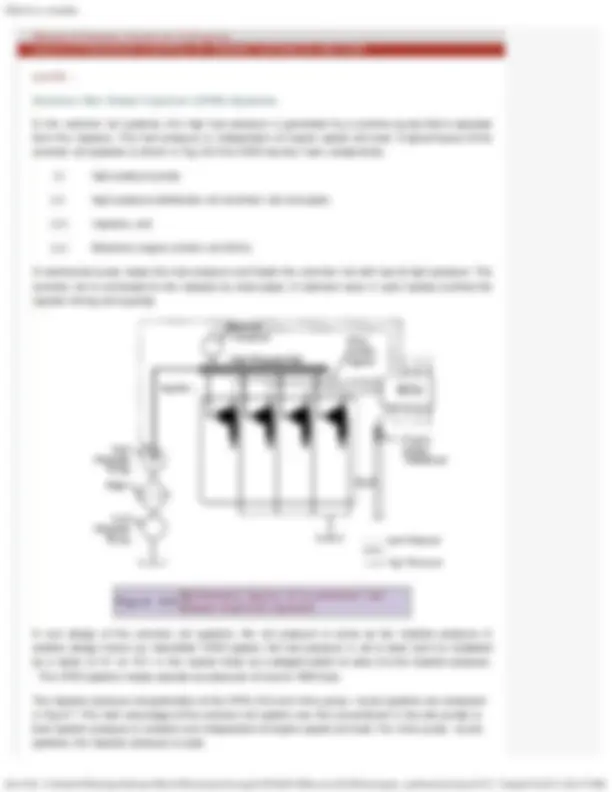
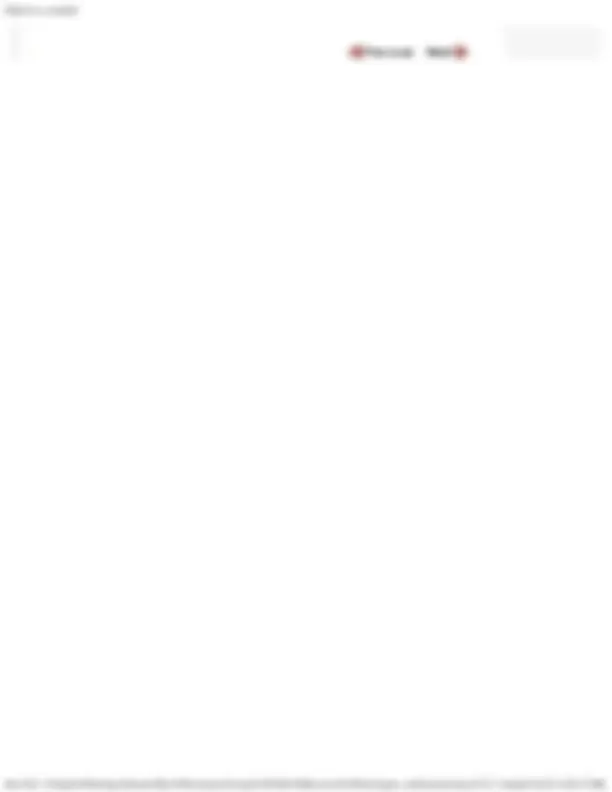
Study with the several resources on Docsity
Earn points by helping other students or get them with a premium plan
Prepare for your exams
Study with the several resources on Docsity
Earn points to download
Earn points by helping other students or get them with a premium plan
Community
Ask the community for help and clear up your study doubts
Discover the best universities in your country according to Docsity users
Free resources
Download our free guides on studying techniques, anxiety management strategies, and thesis advice from Docsity tutors
The objectives of lecture 27 in the module 6 of emission control for ci engines. The lecture focuses on emission control by engine variables and exhaust gas recirculation (egr). Fuel injection variables, electronic fuel injection systems, and the benefits of high injection pressures. It explains how high injection pressures improve fuel atomization, reduce injection duration, and impact the pm-nox trade-off.
Typology: Study notes
1 / 11
This page cannot be seen from the preview
Don't miss anything!
Demands Made on Injection System
To achieve low soot formation, rates of fuel-air mixing are to be enhanced. Fuel injection and air motion in the cylinder are key parameters to achieve rapid fuel-air mixing. The following strategy is adopted to improve fuel air mixing and the diesel engine combustion, which leads to reduction both in the soot and NO (^) x formation:
Use of high fuel injection pressures and smaller nozzle hole size to produce very fine fuel atomization for rapid fuel evaporation and mixing with air. Fuel spray not to impinge on walls but fuel to be distributed mainly within the air inside the combustion chamber. Matching of injection spray configuration and development with in-cylinder air motion for rapid fuel-air mixing throughout the injection duration period Use of variable injection timing, multiple –injection and injection rate shaping technology
High Injection Pressures
The mass flow rate of fuel injected, m (^) f is given by:
where C (^) d is coefficient of discharge, A (^) n is nozzle flow area in m 2 , ρf is fuel density in kg / m 3 , ( P (^) inj - P (^) cyl ) is the pressure drop across nozzle orifice in Pascals, Δθ is the injection duration in degrees crank
angle and N is the engine speed in RPM.
Generally, P (^) inj >> P (^) cyl .,
Thus, for a given injection rate and injection duration Δθ in crank angles, the injection pressure
should vary with speed as,
The speed of engines for road vehicles from lowest working speed to rated speed may vary by a factor of; N (^) max /Nmin = 4 to 5..To achieve similar injection duration and spray penetration from the lowest
to rated engine speed, the injection pressure therefore, is required to vary by a factor of 16 to 25. This of course is not possible in practice but it has led to use of as high an injection pressure as possible. In the pre-1990 engines,
engine load and speed. General principles of fuel injection scheduling are;
rate of fuel injection within the delay period must be kept small to reduce the amount of fuel burned during ‘pre-mixed’ combustion phase, and during the main injection period, rate of injection should be increased steeply to inject fuel within a short period when the temperature and pressure in the combustion chamber are high for rapid combustion of the injected fuel.
The pilot injection is a form of multiple-injection with two injection pulses. In the pilot injection, a small quantity of fuel (about 10% of fuel per cycle) is injected 3 to 10 crank angle degrees before the main injection event. The pilot-injected fuel has more time to undergo precombustion reactions .When the main fuel injection is made, the combustion begins soon after, resulting in a short delay period. As the pilot fuel quantity injected during delay period is rather small, the peak rate of combustion pressure rise and peak pressures are reduced. Typical pilot injection strategy and cylinder pressure are shown on Fig. 6.4.
With pilot injection, the injection timing of main fuel can be retarded to give low NO (^) x emissions without
adversely affecting the engine power and fuel efficiency. Also, with pilot injection less fuel burns as pre-mixed and a larger fraction of fuel burns in diffusion combustion mode. In the normal engine, NO (^) x
reduction is obtained by retarding the injection timing which results in higher smoke and PM emissions, and higher BSFC. Results with pilot injection and conventional engine with retarded injection are compared in Table 6.2. At the same NO (^) x emission levels of 5.5 g/kWh, with pilot injection typically 23 %
lower PM, 50% lower HC and 4 % lower BSFC were obtained.
injector nozzle and the fuel is injected. Opening of the solenoid valve releases the fuel pressure and the injection ends. Another design of EUI developed by Cummins Engine Company, Inc. consists of two plungers in the same unit injector, one controls injection timing and the other controls the injection quantity. As the dead volume between the pumping plunger and injector nozzle is very small, very high injection pressures can be used with a high reliability and injection efficiency. Operation of the EUI at more than 2500 bars has been demonstrated.
The EUI can be used to provide pilot injection. A constant fuel temperature at each injector must be kept so that each injector delivers the same mass of fuel to each engine cylinder. A number of sensors provide input data on the engine speed, load, camshaft position, inlet manifold air temperature and pressure, coolant temperature etc., to the electronic control unit (ECU) for control of fuel injection quantity and injection timing. For small high-speed diesel engines, EUI is not employed due to its large size and high cost. Instead, electronic distributor pumps are used. Now, the common rail injection systems are finding wider application in the small size, high speed multicylinder diesel engines.
low at low engine speeds which increase due to inertia effects at high speeds. It is therefore, difficult to obtain the required engine performance with low emissions throughout the engine speed range with inline fuel injection systems. Electronic unit injectors are better than the inline systems but the CRDI provides more flexibility as a constant injection pressure is maintained at all engine speeds. In the common rail systems, the injection timing and rate can be varied precisely depending upon the engine requirements. As very high injection pressures are possible with electronically controlled CRDI, its benefits are available through out the engine speed range. Because of reduction in particulate emissions due to high injection pressures, higher EGR rates can be used at part loads to reduce NO (^) x emissions, which lead to
a better NO (^) x -particulate trade off. With the common rail systems, injection rate shaping and pilot
injection are also easier to implement.