
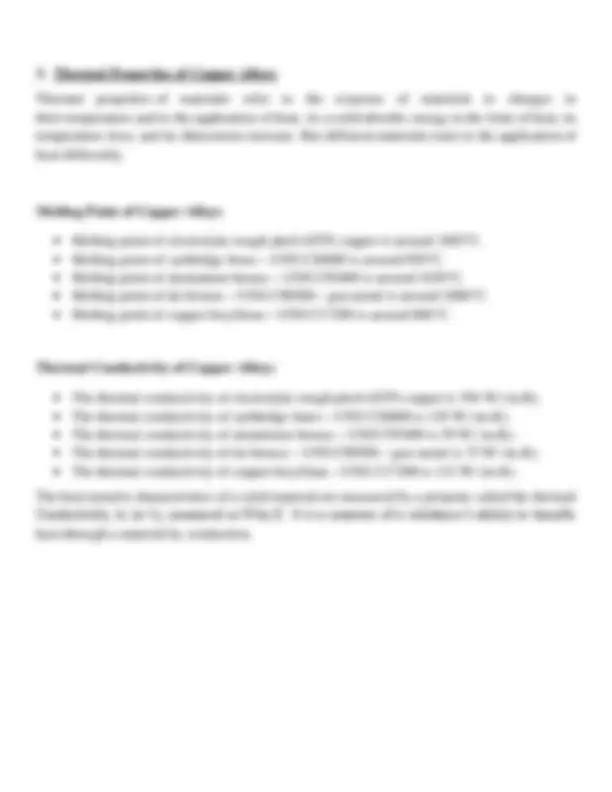
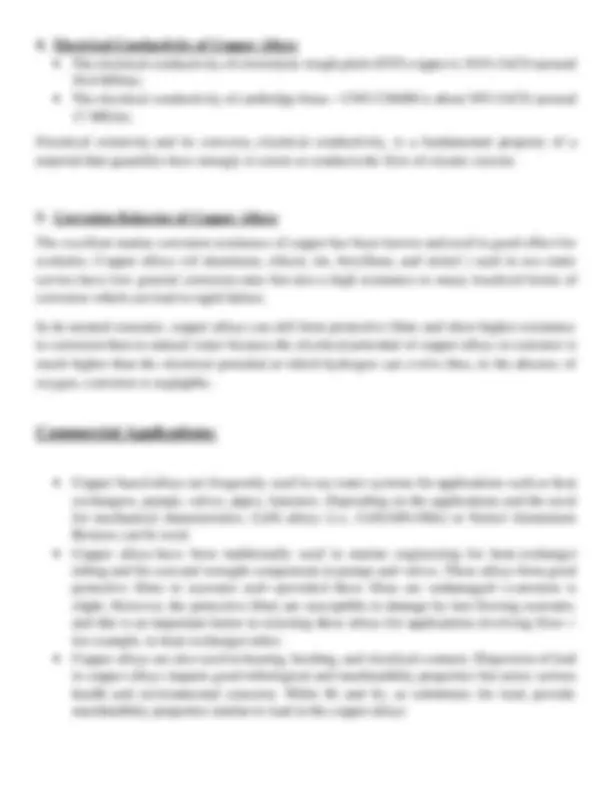
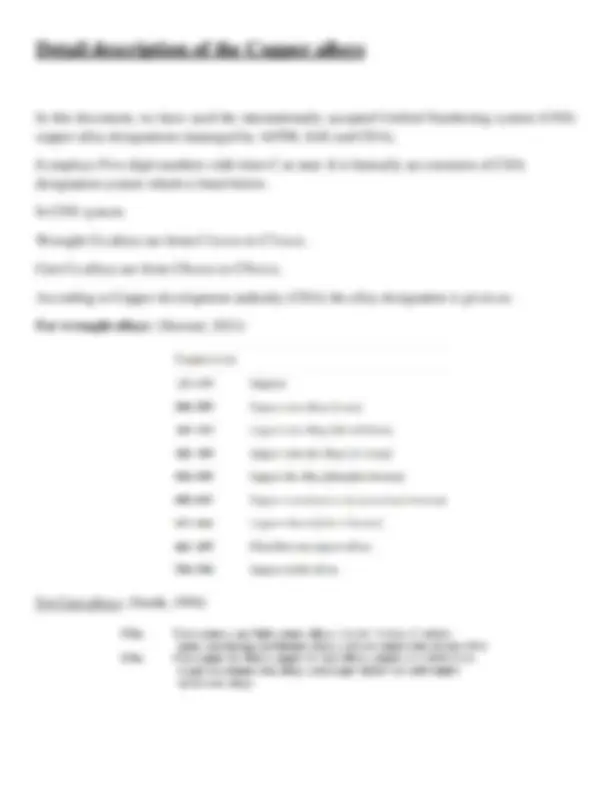
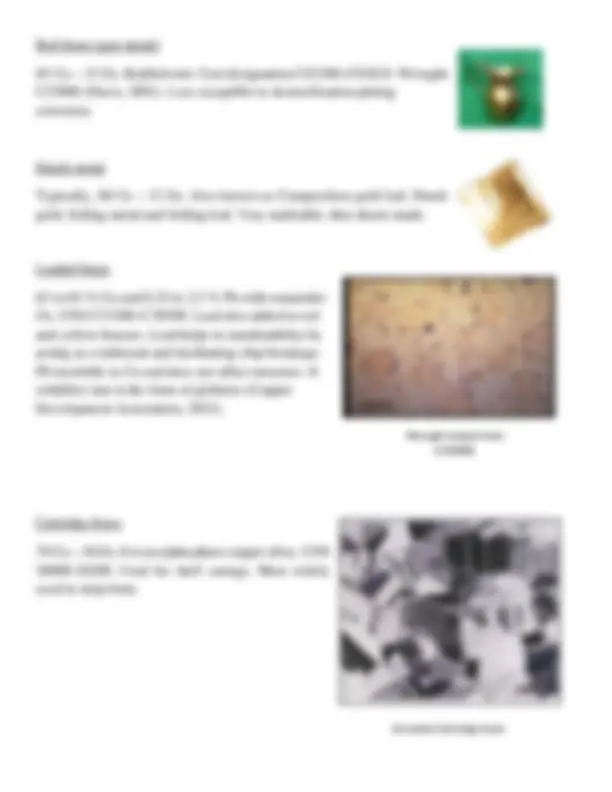
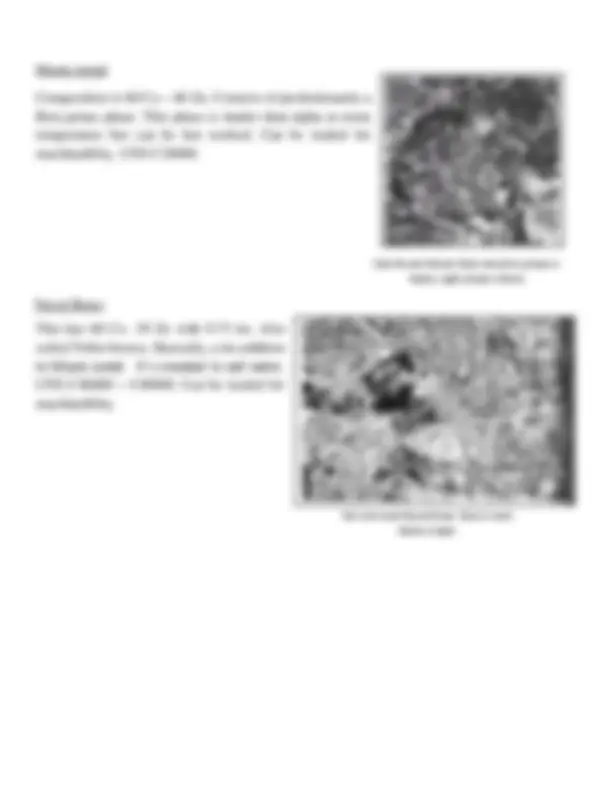
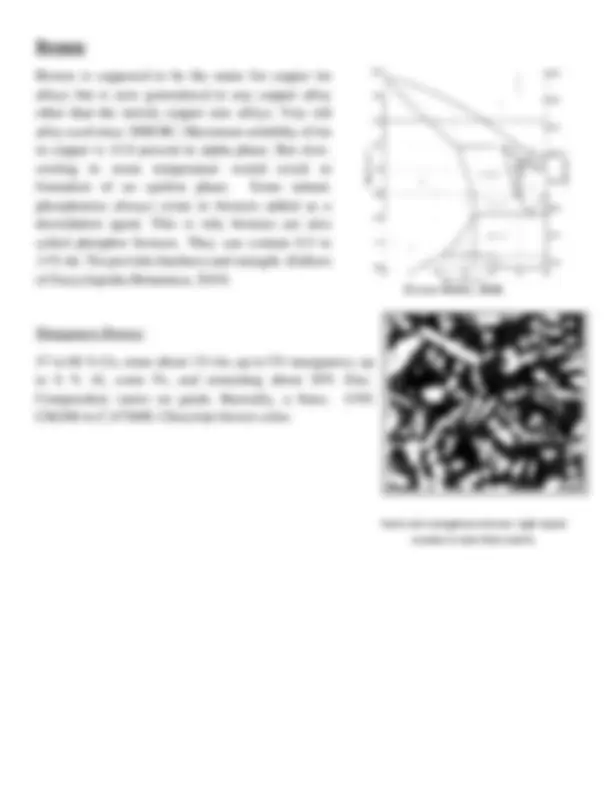
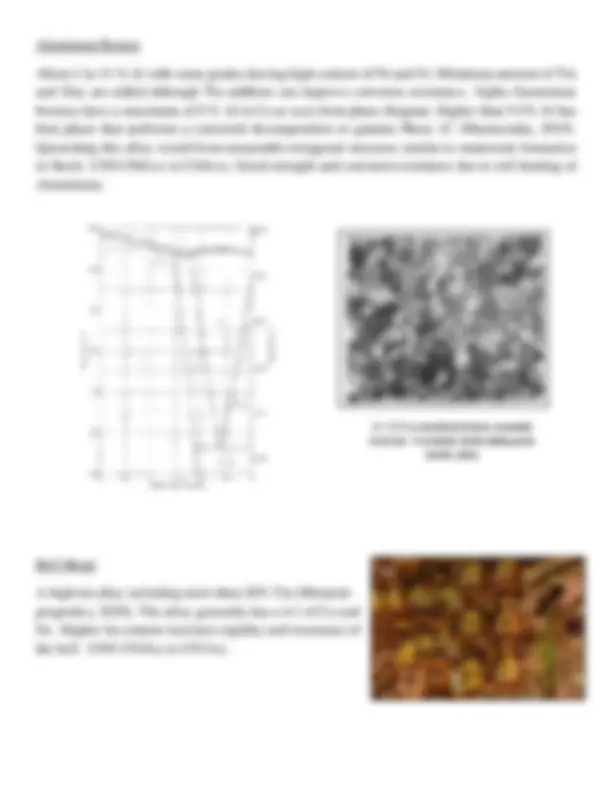
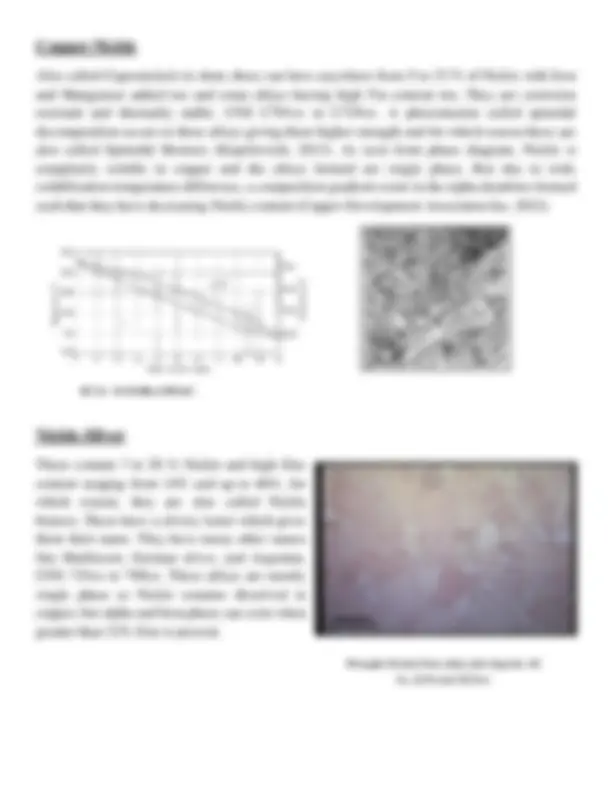
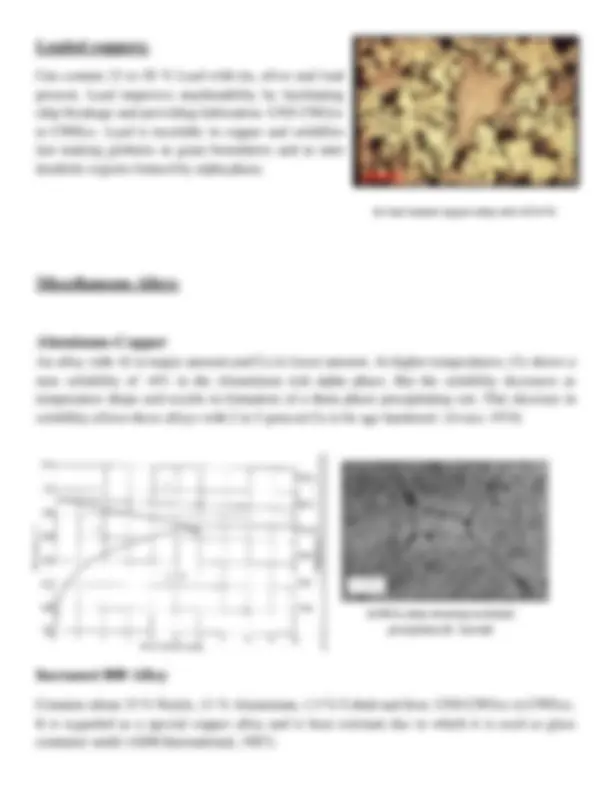
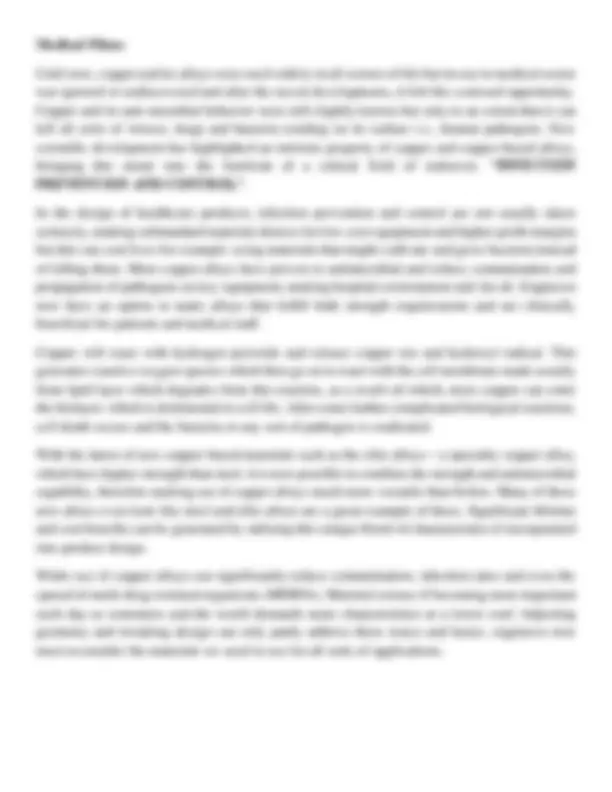
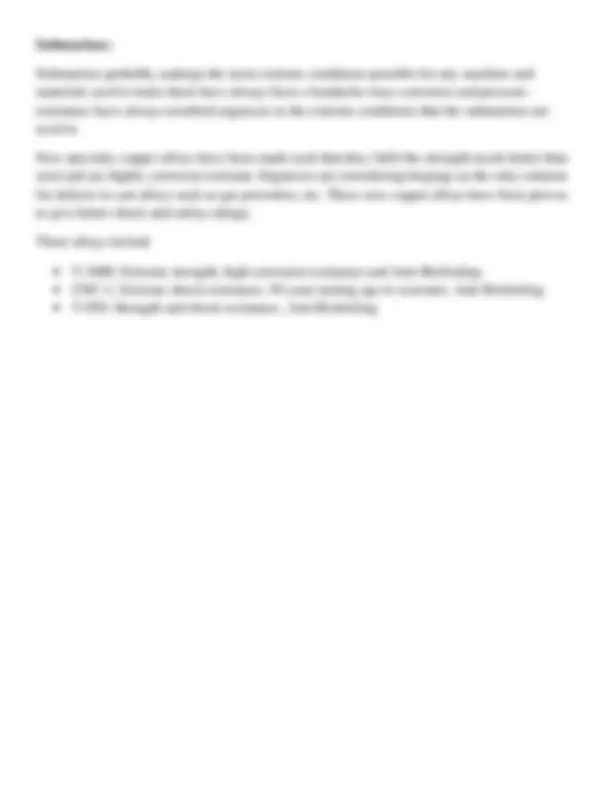
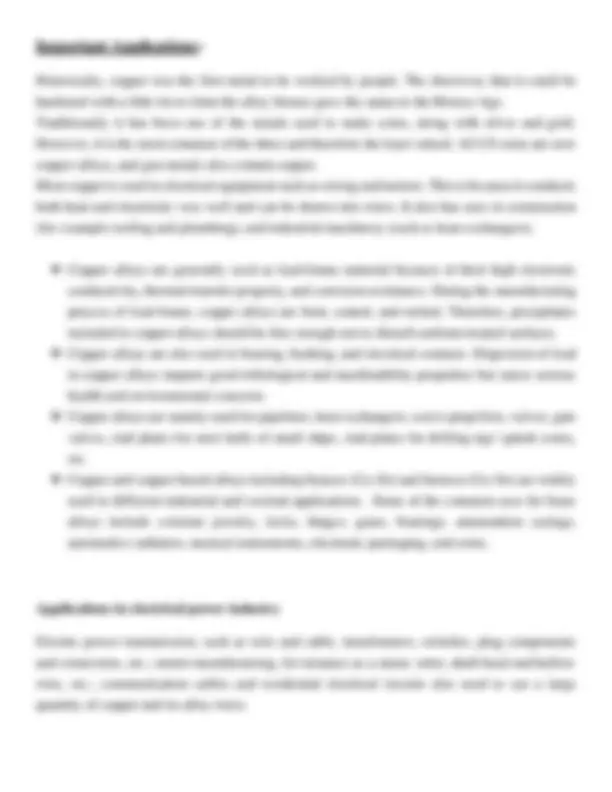
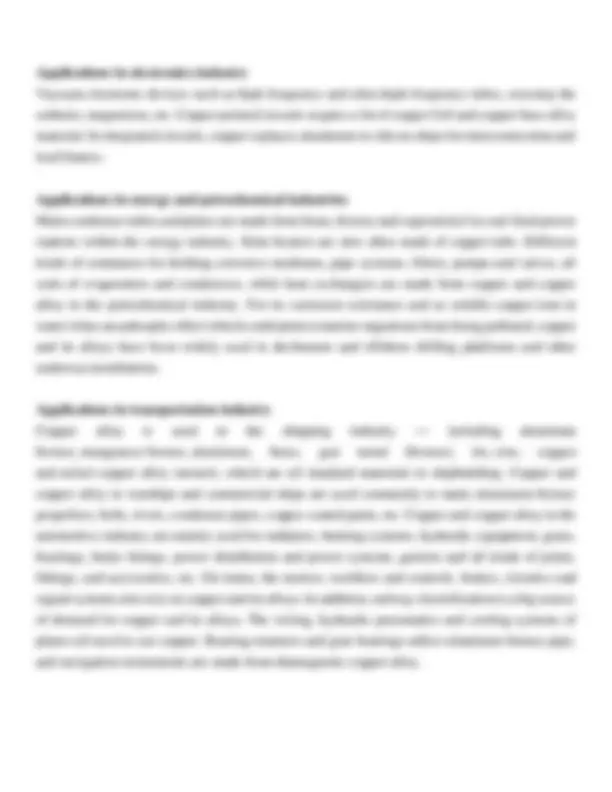
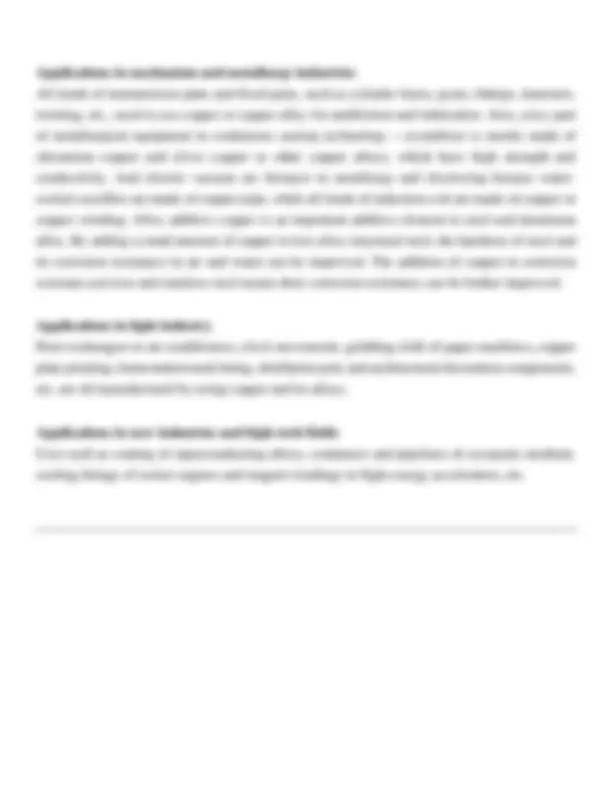
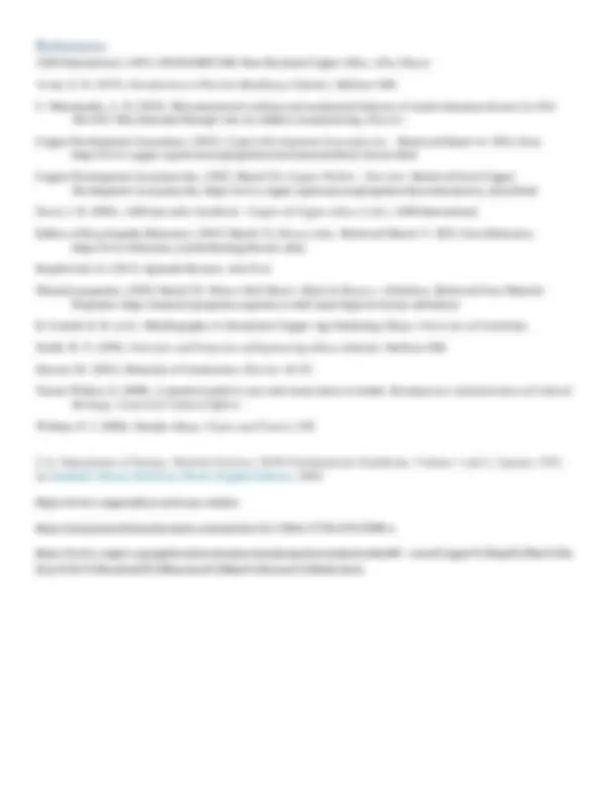
Study with the several resources on Docsity
Earn points by helping other students or get them with a premium plan
Prepare for your exams
Study with the several resources on Docsity
Earn points to download
Earn points by helping other students or get them with a premium plan
Community
Ask the community for help and clear up your study doubts
Discover the best universities in your country according to Docsity users
Free resources
Download our free guides on studying techniques, anxiety management strategies, and thesis advice from Docsity tutors
Copper alloys & their grades are discussed along with their applications in industry. Copper alloys like Brass, Bronze etc are discussed.
Typology: Study Guides, Projects, Research
1 / 23
This page cannot be seen from the preview
Don't miss anything!
Arsalan Muhammad Khan, Amjad Ali, Ihsan Ullah, Istiqlal Hassan & Muhammad Talha Khan
Characteristics and Properties of Copper alloys
1. Mechanical Properties of Copper Alloys Strength of Copper Alloys Strength of a material is its ability to withstand this applied load without failure or plastic deformation. Ultimate Tensile Strength - Ultimate tensile strength of carthridge brass – UNS C26000 is about 315 MPa. - Ultimate tensile strength of aluminium bronze – UNS C95400 is about 550 MPa. - Ultimate tensile strength of tin bronze – UNS C90500 – gun metal is about 310 MPa. - Ultimate tensile strength of copper beryllium – UNS C17200 is about 1380 MPa. The ultimate tensile strength is the maximum on the engineering stress-strain curve. Yield Strength - Proof strength of electrolytic-tough pitch (ETP) copper is between 60-300 MPa. - Yield strength of aluminium bronze – UNS C95400 is about 250 MPa. - Yield strength of tin bronze – UNS C90500 – gun metal is about 150 MPa. - Yield strength of copper beryllium – UNS C17200 is about 1100 MPa. The yield point is the point on a stress-strain curve that indicates the limit of elastic behavior and the beginning plastic behavior. 2. Hardness of Copper Alloys - Vickers hardness of electrolytic-tough pitch (ETP) copper depends greatly on the temper of the material, but it is between 50 – 150 HV. - Brinell hardness of carthridge brass – UNS C26000 is approximately 100 MPa. - Brinell hardness of aluminium bronze – UNS C95400 is approximately 170 MPa. The hardness of aluminum bronzes increases with aluminum (and other alloy) content as well as with stresses caused through cold working. - Brinell hardness of tin bronze – UNS C90500 – gun metal is approximately 75 BHN. - Rockwell hardness of copper beryllium – UNS C17200 is approximately 82 HRB.
4. Electrical Conductivity of Copper Alloys - The electrical conductivity of electrolytic-tough pitch (ETP) copper is 101% IACS (around 58.6 MS/m). - The electrical conductivity of carthridge brass – UNS C26000 is about 30% IACS (around 17 MS/m). Electrical resistivity and its converse, electrical conductivity, is a fundamental property of a material that quantifies how strongly it resists or conducts the flow of electric current. 5. Corrosion Behavior of Copper Alloys The excellent marine corrosion resistance of copper has been known and used to good effect for centuries. Copper alloys (of aluminum, silicon, tin, beryllium, and nickel ) used in sea water service have low general corrosion rates but also a high resistance to many localized forms of corrosion which can lead to rapid failure. In de-aerated seawater, copper alloys can still form protective films and show higher resistance to corrosion than in natural water because the electrical potential of copper alloys in seawater is much higher than the electrical potential at which hydrogen can evolve thus, in the absence of oxygen, corrosion is negligible.
Detail description of the Copper alloys In this document, we have used the internationally accepted Unified Numbering system (UNS) copper alloy designations (managed by ASTM, SAE and CDA). It employs Five-digit numbers with letter C at start. It is basically an extension of CDA designation system which is listed below. In UNS system: Wrought Cu alloys are from C1xxxx to C7xxxx. Cast Cu alloys are from C8xxxx to C9xxxx. According to Copper development authority (CDA) the alloy designation is given as: For wrought alloys : (Stewart, 2021) For Cast alloys: (Smith, 1994)
Chromium Copper: About 0.6 to 1.2 % Chromium is added in copper. These alloys are also age hardenable and can achieve a strength twice as much as pure copper can have. They are also more corrosion resistant compared to pure copper. If the alloy is quenched after solution treatment, the microstructure would be the same as pure copper, but aging treatment can be used to form precipitates of Chromium in alpha Cu matrix.
Brass Composition can be anywhere between 50 to 96 % Cu. Must contain zinc. Alpha and Beta phase form. Alpha is an FCC phase while Beta is BCC. The max solubility of zinc in alpha phase is 39 % (Avner, 1974). This large solubility can be justified by the fact that zinc atom is only 8. % bigger than copper atom. Gilding Metal 95 Cu – 5 Zn. Deep yellow golden color. Used for gilding or electroplating. UNS C Yellow brass 65 Cu – 35 Zn. Clearer color. Used in instruments. UNS cast designation C85200– C85800. Wrought C26800, C27000, and C
Red brass (gun metal) 85 Cu – 15 Zn. Reddish tint. Cast designation C83300–C83810. Wrought C23000 (Davis, 2001). Less suceptible to dezincification pitting corrosion. Dutch metal Typically, 88 Cu – 12 Zn. Also known as Composition gold leaf, Dutch gold, Schlag metal and Schlag leaf. Very malleable, thin sheets made. Leaded brass 62 to 65 % Cu and 0.25 to 2.5 % Pb with remainder Zn. UNS C31200–C38500. Lead also added in red and yellow brasses. Lead helps in machinability by acting as a lubricant and facilitating chip breakage. Pb insoluble in Cu and does not affect structure. It solidifies last in the form of globules (Copper Development Association, 2022). Cartridge brass 70 Cu – 30 Zn. It is an alpha phase copper alloy. UNS 26000 - 26200. Used for shell casings. Most widely used in strip form. Annealed Cartridge brass Wrought leaded brass (C36000)
Bronze is supposed to be the name for copper tin alloys but is now generalized to any copper alloy other than the strictly copper zinc alloys. Very old alloy used since 3000 BC. Maximum solubility of tin in copper is 15.8 percent in alpha phase. But slow. cooling to room temperature would result in formation of an epsilon phase. Some minute phosphorous always exists in bronzes added as a deoxidation agent. This is why bronzes are also called phosphor bronzes. They can contain 0.5 to 11% tin. Tin provides hardness and strength. (Editors of Encyclopedia Britannica, 2019) Manganese Bronze 57 to 68 % Cu, some about 1% tin, up to 5% manganese, up to 6 % Al, some Fe, and remaining about 30% Zinc. Composition varies on grade. Basically, a brass. UNS C66300 to C 675600. Chocolate brown color. Sand cast manganese bronze. Light alpha needles in dark Beta matrix. (Turner-Walker, 2008)
Silicon Bronze Silicon bronzes is a general name given to Silicon copper alloys. Silicon content ranges from 0.4 to 4 % while tin is around 1.5 %, Manganese, Nickle and Iron are present and lead is kept to a minimum. Leaving behind about 95 % Copper. Silicon has a max solubility of about 5 percent in primary Cu phase and by keeping Si composition low and avoiding slow cooling, single phase Cu-Si alloys are formed. Strongest and most work-hardenable copper alloys. UNS C647xx to C661xx. Copper-Bismuth Bronze 0.7 to 5.5 % Bismuth with typically 2 to 4 % Zinc and Lead mixed with Cu. Similar to lead, bismuth is hardly soluble in copper, and forms globules. Bismuth aids in machinability. Serves as substitute to hazardous leaded copper alloys. Selenium is also added to strengthen properties of Bismuth. UNS C89300 to C89900.
Aluminum Bronze About 2 to 15 % Al with some grades having high content of Ni and Fe. Minimum amount of Tin and Zinc are added although Tin addition can improve corrosion resistance. Alpha Aluminium bronzes have a maximum of 8 % Al in Cu as seen from phase diagram. Higher than 9.5% Al has beta phase that performs a eutectoid decomposition to gamma Phase (C. Dharmendra, 2019). Quenching this alloy would from metastable tetragonal structure similar to martensite formation in Steels. UNS C60xxx to C64xxx. Good strength and corrosion resistance due to self-healing of Aluminium. Bell Metal A high tin alloy including more than 20% Tin (Metarial- properties, 2020). The alloy generally has a 4:1 of Cu and Sn. Higher tin content increases rigidity and resonance of the bell. UNS C910xx to C913xx. Al - 5 % Cu Aluminium bronze annealed structure. Twin bands inside alpha grains (Smith, 1994)
Wrought Nickle Silver alloy with Approx. 60 Cu, 12 Ni and 28 Zinc
Also called Cupronickels in short, these can have anywhere from 9 to 33 % of Nickle with Iron and Manganese added too and some alloys having high Tin content too. They are corrosion resistant and thermally stable. UNS C701xx to C729xx. A phenomenon called spinodal decomposition occurs in these alloys giving them higher strength and for which reason these are also called Spinodal Bronzes (Kopeliovich, 2013). As seen from phase diagram, Nickle is completely soluble in copper and the alloys formed are single phase. But due to wide solidification temperature difference, a composition gradient exists in the alpha dendrites formed such that they have decreasing Nickle content (Copper Development Associaton Inc, 2022).
These contain 7 to 20 % Nickle and high Zinc content ranging from 14% and up to 46%, for which reason, they are also called Nickle brasses. These have a silvery luster which gives them their name. They have many other names like Maillecort, German silver, and Argentan. UNS 735xx to 798xx. These alloys are mostly single phase as Nickle remains dissolved in copper, but alpha and beta phase can exist when greater than 32% Zinc is present. 85 Cu – 15 Ni alloy chill cast
Cu-Mn-Al Heusler alloy showing magnetic domain walls
This name was used for copper alloys in old ages. Today it is not clearly defined and can contain varying amounts of copper, tin, lead, and zinc and can be regarded as a general name for brass and bronze. In medieval English, the name was used to denote impure Copper.
Heusler alloys contain two parts Cu, one part Mn, and one part Tin. Other additions may include Aluminium, Arsenic, Bismuth, or Boron. This alloy is composed of metals that are not ferromagnetic but the alloy itself is ferromagnetic (Webster, 2006). These alloys are regarded as ternary intermetallic alloys.
Antimicrobial effect of copper: An increased proportion of Gram-negative bacteria have recently been reported among etiologic agents of infection. In Poland, “ Acinetobacter baumannii” is a big problem for hospitals, especially intensive care units, leading to numerous germ-infected diseases being spread to patients and visitors and the numbers are increasing exponentially. Touch surfaces made from materials with antimicrobial properties, especially copper alloys, are recommended as a supplementary method of increasing biological safety in the hospital environment. Antimicrobial copper-alloy touch surfaces can prevent frequently touched surfaces from serving as reservoirs for the spread of pathogenic microbes. This is especially true in healthcare facilities, where harmful viruses, bacteria, and fungi colonize and persist on doorknobs, push plates, railings, tray tables, tap (faucet) handles, IV poles, HVAC systems, and other equipment. These microbes can sometimes survive on surfaces for more than 30 days. Copper-touch Australia commissioned the Doherty Institute at the Melbourne University Australia to test its Antimicrobial Copper adhesive film. Lab tests proved a 96% kill rate of Influenza A virus with the film as compared to non-treated surfaces. The surfaces of copper and its alloys, such as brass and bronze, are antimicrobial. They have an inherent ability to kill a wide range of harmful microbes relatively rapidly – often within two hours or less – and with a high degree of efficiency. These antimicrobial properties have been demonstrated by an extensive body of research. The research also suggests that if touch surfaces are made with copper alloys, the reduced transmission of disease-causing organisms can reduce patient infections in hospital intensive care units (ICU) by as much as 58%. Several companies have developed methods for utilizing the antimicrobial functionality of copper on existing high- touch surfaces. New technologies utilize cold-spray antimicrobial copper coating technology to apply antimicrobial coatings to surfaces.
Submarines: Submarines probably undergo the most extreme conditions possible for any machine and materials used to make them have always been a headache since corrosion and pressure- resistance have always troubled engineers in the extreme conditions that the submarines are used in. New specialty copper alloys have been made such that they fulfil the strength needs better than steel and are highly corrosion resistant. Engineers are considering forgings as the only solution for defects in cast alloys such as gas porosities, etc. These new copper alloys have been proven to give better shock and safety ratings. These alloys include
Historically, copper was the first metal to be worked by people. The discovery that it could be hardened with a little tin to form the alloy bronze gave the name to the Bronze Age. Traditionally it has been one of the metals used to make coins, along with silver and gold. However, it is the most common of the three and therefore the least valued. All US coins are now copper alloys, and gun metals also contain copper. Most copper is used in electrical equipment such as wiring and motors. This is because it conducts both heat and electricity very well and can be drawn into wires. It also has uses in construction (for example roofing and plumbing), and industrial machinery (such as heat exchangers). ❖ Copper alloys are generally used as lead-frame material because of their high electronic conductivity, thermal transfer property, and corrosion resistance. During the manufacturing process of lead frame, copper alloys are bent, coated, and etched. Therefore, precipitates included in copper alloys should be fine enough not to disturb uniform treated surfaces. ❖ Copper alloys are also used in bearing, bushing, and electrical contacts. Dispersion of lead in copper alloys imparts good tribological and machinability properties but raises serious health and environmental concerns. ❖ Copper alloys are mainly used for pipelines, heat exchangers, screw propellers, valves, gate valves, clad plates for steel hulls of small ships, clad plates for drilling rigs' splash zones, etc. ❖ Copper and copper-based alloys including brasses (Cu-Zn) and bronzes (Cu-Sn) are widely used in different industrial and societal applications. Some of the common uses for brass alloys include costume jewelry, locks, hinges, gears, bearings, ammunition casings, automotive radiators, musical instruments, electronic packaging, and coins. Applications in electrical power industry Electric power transmission, such as wire and cable, transformers, switches, plug components and connectors, etc.; motor manufacturing, for instance as a stator, rotor, shaft head and hollow wire, etc.; communication cables and residential electrical circuits also need to use a large quantity of copper and its alloy wires.