
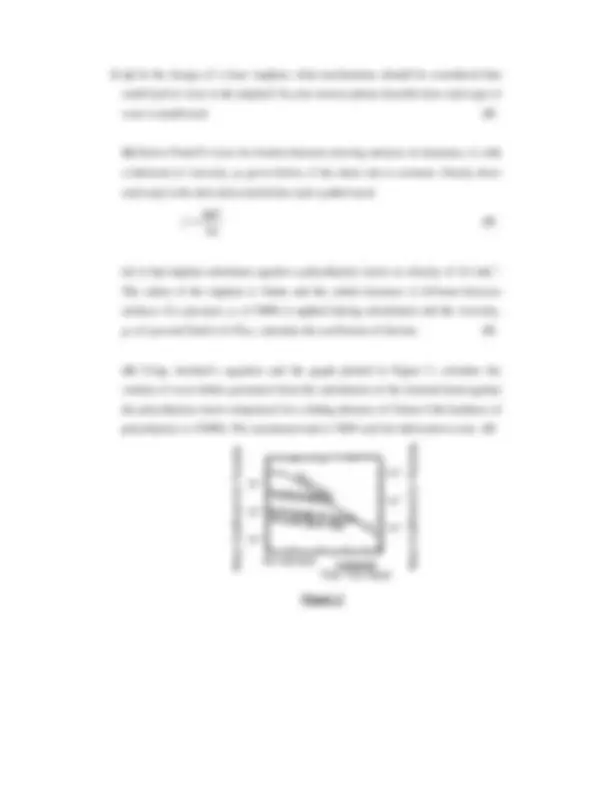
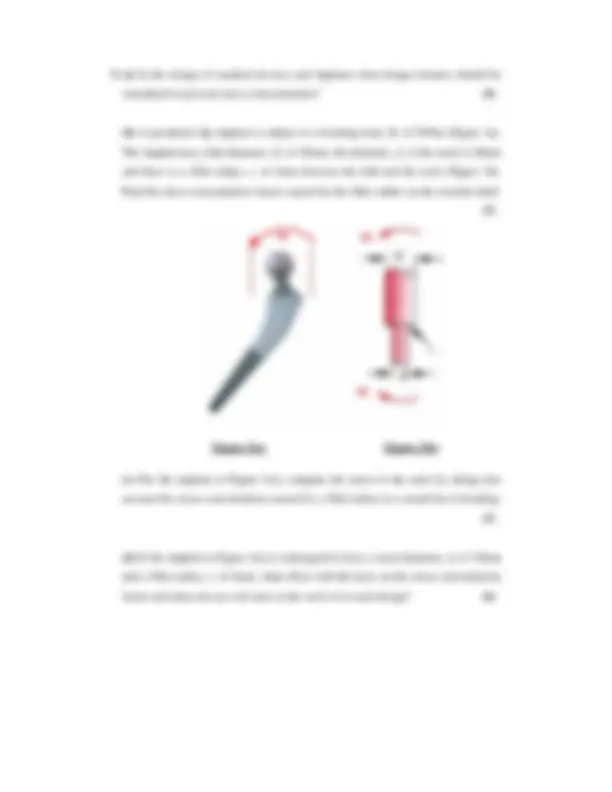
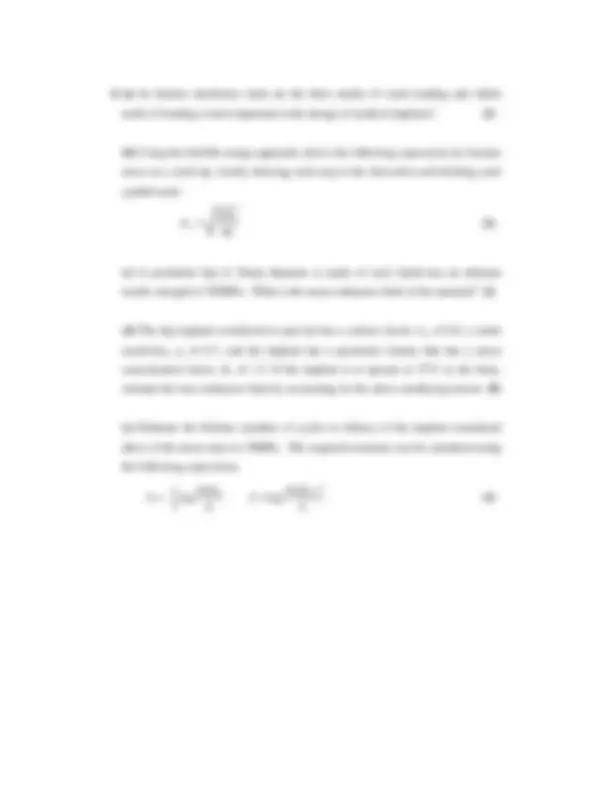
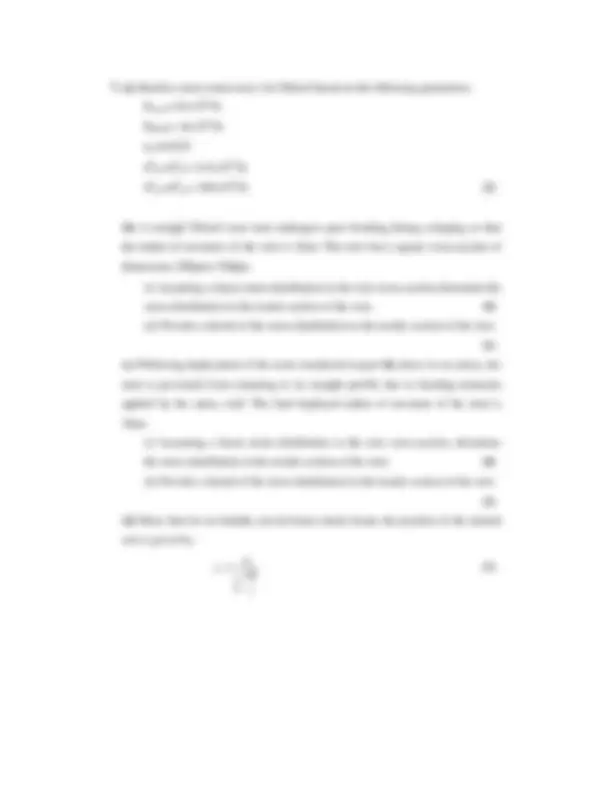
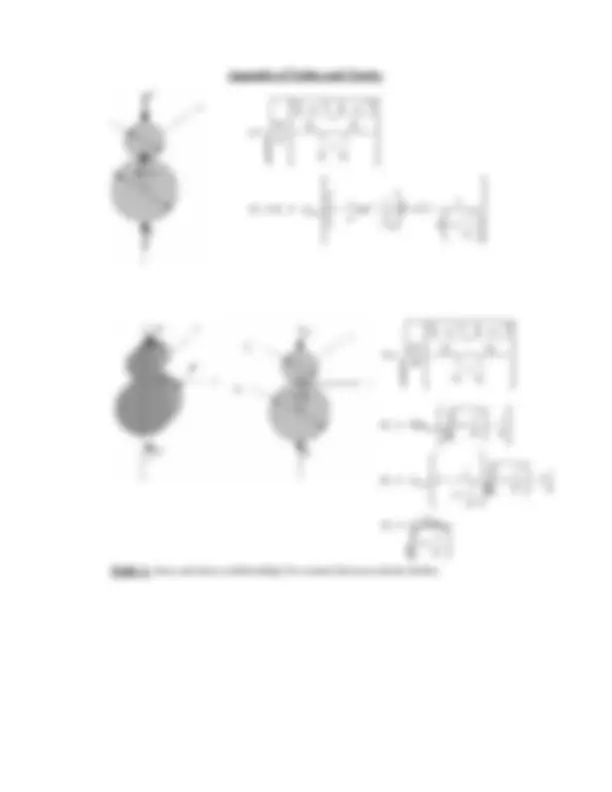
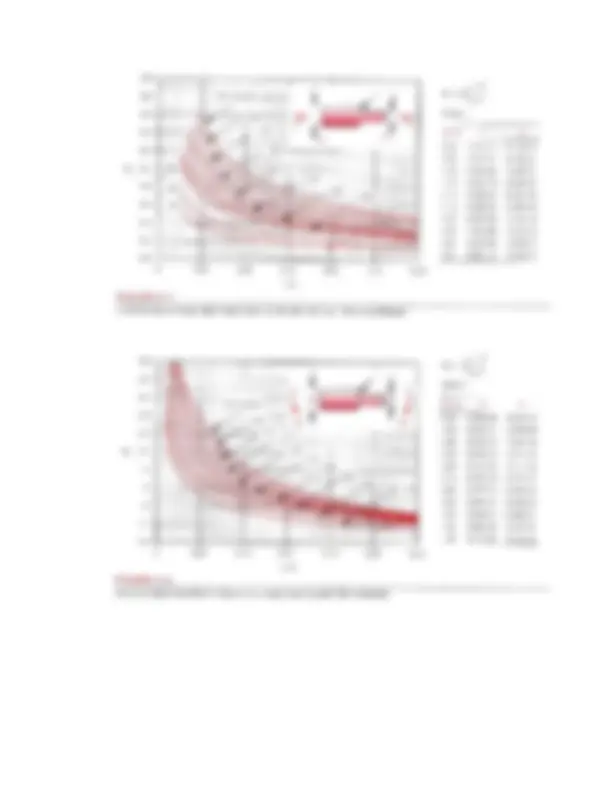
Study with the several resources on Docsity
Earn points by helping other students or get them with a premium plan
Prepare for your exams
Study with the several resources on Docsity
Earn points to download
Earn points by helping other students or get them with a premium plan
Community
Ask the community for help and clear up your study doubts
Discover the best universities in your country according to Docsity users
Free resources
Download our free guides on studying techniques, anxiety management strategies, and thesis advice from Docsity tutors
Main points of this past exam paper are: Design Criteria, Orthopaedic Implant, Mechanical Demands, Surgeon, Implant, Titanium Knee Prosthesis, Curved Polethylene Tibial Tray, Curvature, Radius, Internal Radius
Typology: Exams
1 / 11
This page cannot be seen from the preview
Don't miss anything!
Exam Code(s) 4BG Exam(s) 4 th Engineering – Biomedical
Module Code(s) ME Module(s) Medical Implant and Device Design
Paper No. I
External Examiner(s) Professor Brian Meenan Internal Examiner(s) Professor Peter McHugh *Dr. Laoise McNamara *Dr. Patrick McGarry
Instructions: The paper contains 7 questions. Answer 5 questions. Answer at least 1 question from Section A and 1 question from Section B. All questions will be marked equally. Use a separate answer book for each section.
Duration 3hrs
No. of Pages^11
Department(s) Mechanical and Biomedical Engineering
Requirements None
Section A
1. (a) Identify the main design criteria for an orthopaedic implant to meet the mechanical demands applied during everyday loading. (3)
(b) A surgeon chooses to implant a titanium knee prosthesis (E = 105 GPa, ν=0.32) of radius of curvature 60mm with a curved polethylene tibial tray (E = 20 MPa, ν=0.46) of internal radius of curvature of 60.1mm (Figure 1a). Calculate the contact area half width, b , if approximately four times body weight (70 Kg) will be supported during flexion and the thickness, l , of the contact between the knee and femoral component and the tibial tray is 15mm (Figure 1b). (4)
Figure 1(a) Figure 1(b)
(c) Determine the maximum pressure in the assembly considered in part (b) above. (3)
(d) Determine the maximum shear stress generated in the polyethylene tray at the point A located 0.75 b from the contact surface (Figure 1b). If the yield strength of polyethylene is 20MPa, will failure occur in the tibial tray due to the applied contact forces? (8)
0.75b
l
3. (a) In the design of medical devices and implants what design features should be considered to prevent stress concentrations? (4)
(b) A prosthetic hip implant is subject to a bending load, M , of 50Nm (Figure 3a). The implant has a ball diameter, D , of 45mm, the diameter, d , of the neck is 30mm and there is a fillet radius, r , of 2mm between the ball and the neck (Figure 3b). Find the stress concentration factor caused by the fillet radius on the circular shaft. (5)
Figure 3(a) Figure 3(b)
(c) For the implant in Figure 3(a), compute the stress in the neck by taking into account the stress concentration caused by a fillet radius in a round bar in bending. (5)
(d) If the implant in Figure 3(a) is redesigned to have a neck diameter, d , of 35mm and a fillet radius, r , of 4mm, what effect will this have on the stress concentration factor and what stresses will arise in the neck of revised design? (6)
4. (a) In fracture mechanics what are the three modes of crack loading and which mode of loading is most important in the design of medical implants? (2)
(b) Using the Griffith energy approach, derive the following expression for fracture stress at a crack tip, clearly showing each step in the derivation and defining each symbol used.
a
E (^) e f π σ = 2 γ (5)
(c) A prosthetic hip of 35mm diameter is made of steel which has an ultimate tensile strength of 450MPa. What is the mean endurance limit of the material? (2)
(d) The hip implant considered in part (c) has a surface factor, ka , of 0.8, a notch sensitivity, q , of 0.7, and the implant has a geometric feature that has a stress concentration factor, Kt , of 1.5. If the implant is to operate at 37°C in the body, estimate the true endurance limit by accounting for the above modifying factors. (8)
(e) Estimate the lifetime (number of cycles to failure) of the implant considered above if the mean stress is 50MPa. The required constants can be calculated using the following expressions.
e
ut S b log^0.^8 S 3
e
ut S C = log(^0.^8 S^ )^2 (3)
Section B
6. (a) What is the source of loading that can contribute to the fatigue failure of stents? (1) (b) What are the FDA requirements for the fatigue assessment of stents? (1) (c) In a finite element plane stress stent analysis, following simulation of deployment and recoil, a pressure load equivalent to 80mmHg is applied to a stent geometry. For two points, A and B, the stresses computed before and after the application of this load are given in Table 6. σxx (MPa) σyy (MPa) σxy (MPa) Point A before load 400 0 0 Point A after load 410 0 20 Point B before load -200 10 100 Point B after load 0 500 0 Table 6
(i) Construct a Goodman diagram for a cobalt chromium stent that includes Points A and B. Does failure occur? (8) (ii) Include the safety line for stainless steel on the same diagram. If the same stresses were computed for a stainless steel stent would failure occur? (2) (d) A post-deployment examination of the cobalt chromium stent analysed in part (c) above using a scanning electron microscope (SEM) reveals cracks of length 1μm on the stent surface. The Paris equation for the rate of fatigue crack growth is given as
where a is the crack length, N is the number of cycles, ∆ K is the change in the stress intensity factor and C and m are material parameter constants. You may assume that when units of m and MPa are used for crack length and stress respectively, for cobalt chromium m =2.5 and C =4.74x10-13. (i) From the maximum value of alternating stress computed in part (c) determine the expected lifetime of the stent (assume that stent failure occurs when a crack grows to a length of 20μ). (7) (ii) Are FDA requirements satisfied for the design? (1)
7. (a) Sketch a stress strain curve for Nitinol based on the following parameters: EAUS= 83x10^9 Pa EMAR= 18x10^9 Pa εL=0. σStL=σEtL= 414x10^6 Pa σStU=σEtU= 100x10^6 Pa (3)
(b) A straight Nitinol stent strut undergoes pure bending during crimping so that the radius of curvature of the wire is 2mm. The wire has a square cross-section of dimensions 200μm× 200 μm. (i) Assuming a linear strain distribution in the wire cross-section determine the stress distribution in the tensile section of the wire. (4) (ii) Provide a sketch of the stress distribution in the tensile section of the wire. (1) (c) Following deployment of the stent considered in part (b) above in an artery, the strut is prevented from returning to its straight profile due to bending moments applied by the artery wall. The final deployed radius of curvature of the strut is 3mm. (i) Assuming a linear strain distribution in the wire cross-section, determine the stress distribution in the tensile section of the wire. (4) (ii) Provide a sketch of the stress distribution in the tensile section of the wire. (1) (d) Show that for an initially curved linear elastic beam, the position of the neutral axis is given by.
A
n r
dA r A (7)